Vrije Universiteit Brussel
Videos
Loading the player ...
- Offer Profile
- The Multibody Mechanics Group of the Department of Mechanical Engineering at the Vrije Universiteit Brussel (VUB) started its research activities on computer-aided analysis of rigid and flexible mechanical systems in 1990. Its main research is focused on kinematical and dynamical simulations and on the development and use of new actuators as well as on the control of mechanical systems.
Product Portfolio
Probo - intelligent huggy robot
- 整理是一个智能huggy机器人发展ped as research platform to study cognitive human-robot interaction (cHRI) with a special focus on children. The robot Probo is designed to act as a social interface, providing a natural interaction while employing human-like social cues and communication modalities. The robot has a fully actuated head, with 20 degrees of freedom, capable of showing facial expressions. A remarkable feature is the moving trunk and the soft and huggable jacket. A user friendly Robotic User Interface (RUI) enables the operator to control the robot.
-
-
-
Lucy - bipedal walking robot
- The goal of this project is to create a lightweight biped which is able to walk in a dynamical stable way. The configuration of this biped is anthropomorphic focusing on the lower walking part which is composed of two articulated legs. The robot, all included, weighs about 30 kg and is 150cm tall. This robot is restricted to move only in the sagittal plane due to it’s one dimensional joints of which each of them are powered by an antagonistic pair of Pleated Pneumatic Artificial Muscles. These muscles are lightweight pneumatic actuators which work at low pressures and can be directly coupled without complex gearing mechanisms. The adaptable passive behaviour of these actuators will be exploited in the walking algorithms.
One of the key ideas in the design is modularity which resulted in nearly the same configuration for each structural element as well as the mechanical, electronic and low-level controlsoftware part. The joint design itself allows easy changes in actuator characteristics which creates a flexible experimental platform.
-
-
-
Pneumatic artificial muscles
- 气动人工肌肉,从本质上讲,一个我mbrane that will expand radially and contract axially when inflated, while generating high pulling forces along the longitudinal axis. Different designs have been developed. The best known is the so called McKibben muscle (example is the Air Muscle of the Schadow Robot Company). This muscle contains a rubber tube which will expand when inflated, while a surrounding netting transfers tension. Hysteresis, due to dry friction between the netting and the rubber tube, makes control of such a device rather complicated. Typical of this type of muscles is a threshold level of pressure before any action can take place. The main goal of the new design was to avoid both friction and hysteresis, thus making control easier while avoiding the threshold. This was achieved by arranging the membrane into radially laid out folds that can unfurl free of radial stress when inflated. The membrane's stiff longitudinal fibres transfer tension.
-
-
-
Soft Arm
- Repetitive manual handling of heavy loads is common in assembly and is a frequent cause of lower back disorders. This can have a significant impact on the quality of life and has a serious economic cost. Manipulators are robotic systems designed to avoid these problems. They assist people in performing heavy-duty tasks.
Most of the commercially available manipulators use a counterweight, which limits their use to handling loads of a specific mass. Others are electrically or hydraulically actuated. This usually makes them heavy, complex and expensive.
The use of the PPAM actuator allows us to tackle these issues and develop a manipulator that combines ergonomics, operator safety, low cost, low weight and ease of operation.
The goal of our research is to develop a proof-of-concept manipulator that will be used in direct contact with an operator, without expensive force or torque sensors and without user interaction through control elements (such as joysticks). We are working towards a system that behaves as follows: when the operator wants to move a load attached to the manipulator, he/she starts moving it as if there were no manipulator. By measuring the muscle gauge pressures, the system can estimate the forces applied by the operator and assist him in accomplishing the desired load movement. Ideally, moving a 30 kg load would feel like moving a 3 kg load. The direct interaction between operator and load (without intermediary control tools) allows for very precise positioning.
-
-
-
AMPfoot
- Walking with classical protheses is very difficult and energy consuming and is like Hugh Herr says "like walking with closed ski boots". Out of our technology of compliant actuators and bipedal walking robots like the biped Lucy we developed the AMP foot. It is a passive prosthesis (so no energy is supplied in the walking gait), but energy is stored and released trying to mimic as best as possible a normal ankle.
-
-
MACCEPA: The Mechanically Adjustable Compliance and Controllable Equilibrium Position Actuator
- Besides the development and implementation of the Pleated Pneumatic Artificial Muscles, our research group developed a second actuator with adaptable compliance. The MACCEPA (The Mechanically Adjustable Compliance and Controllable Equilibrium Position Actuator) is a straightforward and easy to construct rotational actuator, of which the compliance can be controlled separately from the equilibrium position. Each of these parameters is set by a position controlled servo motor. Moreover, the torque is a linear function of the compliance and of the angle between equilibrium position and actual position. Thus this actuator can be seen as a fully adaptable torsion spring, where one motor sets the stiffness of the torsion spring, and another set the equilibrium position. Since this actuator has a spring it can store and release energy. This makes this actuator perfectly suitable for dynamic walking and human-robotic interfaces.
-
-
-
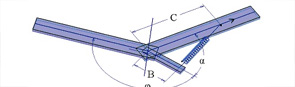
- As can be seen there are 3 bodies pivoting around one rotation axis. To visualize the concept, the left body in figure 1 can be seen as an upper leg, the right body as the lower leg and the rotation axis, which goes through the knee joint. Around this rotation axis, a lever arm is pivoting, depicted as a smaller body in figure 3. A spring is attached between a fixed point on the lever arm and a cable running around a fixed point on the right body to a pretension mechanism.