Videos
Loading the player ...
Product Portfolio
Markets
- The diversification of our business model makes us independent of the development of individual market sectors and gives us important advantages in global competition.
Market conditions can change quickly and often cannot be controlled even by their own participants. We see these developments as an opportunity, because this is where the great strengths of our company lie. Thanks to our wide footprint and successful cross-industry technology transfer, we can compensate for temporary weakness in one branch by positively developing others. This reduces our dependence on single industries, and creates synergies that greatly benefit our customers.
We focus on fast-growing future markets with short product cycles. With our innovative products, we are trailblazers for future development and the emergence of key technologies for our era. Countless components for smartphones, tablet computers, electric vehicle batteries, consumer electronics, stationary energy storage and solar modules are produced with our high-efficiency machines.
Our technologies significantly contribute to lowering the production cost of end products and to making them globally accessible to large groups of buyers.
-
-
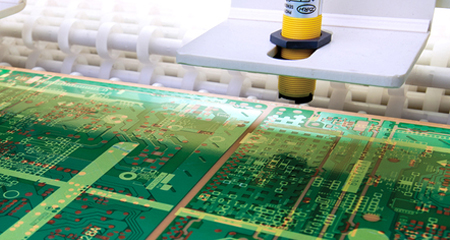
Electronic Components
-
- We lay the groundwork for continuously increasing end product performance while reducing production costs with our solutions for producing displays, printed circuit boards as well as automobile and industrial electronics.
DISPLAYS
Whether computer screens, TVs, smartphones, tablet computers or operating displays at industrial workstations, important components of these products have been produced for many years on our equipment. In the manufacturing of LCD and (AM)OLED flat screens as well as touch sensors, our production technology has established us as a long-term partner for customers worldwide.
PRINTED CIRCUIT BOARDS
For the production of printed circuit boards and chip carriers, Manz offers wet chemical process technologies and equipment for laser direct imaging of printed circuit boards.
AUTOMOBILE & INDUSTRIAL ELECTRONICS
With more than 30 years of experience in automation, measurement technology and process technologies, we understand our customers' needs and offer modular solutions for a variety of assembly and process steps in the manufacturing of automobile and industrial electronics.
-
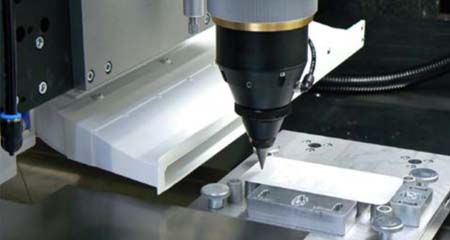
Electronic Devices
-
- With our modular, fully automated production systems, Manz can precisely meet the needs of the consumer electronics industry. For this we employ our decades of technological expertise in robotics, automation, image processing and screen printing, as well as control and laser technology.
Electronic devices, such as smartphones, tablet computers and laptops are known for their extremely short life cycle. Fast product development and a continuous succession of new features in the end product are crucial to manufacturers’ survival. In countless customer projects we have already shown impressive capabilities in this field.
Our customers — renowned manufacturers of smartphones, tablet computers and laptops, as well as their suppliers — use Manz high-tech equipment to meet the existential challenges of their markets: increasing wage costs in countries like China, demand for consistent high quality in end products, and protection of intellectual property.
When Manz is integrated in the design phase for new products, we can ensure that our customers’ intellectual property is protected as early as in the development stage.
Moreover, with our simultaneous engineering capabilities, we can considerably reduce development time while significantly lowering production costs by recognizing and eliminating error sources early.
-
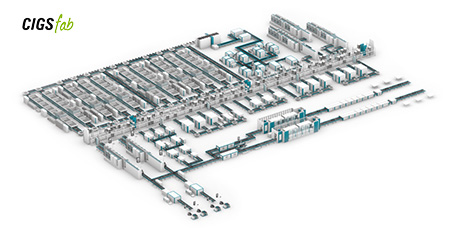
Solar
-
- As a pioneer in designing and building photovoltaic machines, we have over 25 years’ experience in taking photovoltaics from the laboratory to the factory floor. Our solutions have helped solar companies offer their products at a fraction of their original cost and bring them to market faster and faster.
As energy requirements increase worldwide, the percentage of renewable energy sources in the overall energy mix is also growing. Photovoltaics — direct conversion of light energy to electrical energy — plays a crucial role in this development.
In more than 50 % of the countries worldwide, solar energy has reached grid parity. This means that solar energy costs are now at the same level as conventionally produced electricity, or even lower. This will make photovoltaics increasingly attractive — even without subsidies — in countries that are heavy energy users. The result will be strong growth worldwide.
We offer customers globally the latest production equipment for manufacturing thin-film solar modules. Our goal in the area of thin-film technology is to cover all relevant processes along the value creation chain with technology we develop in house.
Our product portfolio sets international standards in terms of efficiency increase while reducing production costs. We cover the following areas:
- Production solutions for manufacturing thin-film solar modules
- The world’s only provider of turnkey production lines for CIGS thin-film solar modules (CIGSfab)
In contrast to crystalline solar technology, the deposition of the semiconductor in thin-film solar technology occurs on a glass substrate. The name of this technology is due to the fact that the conducting layer is about 100 times thinner than in the case of crystalline technology.
-
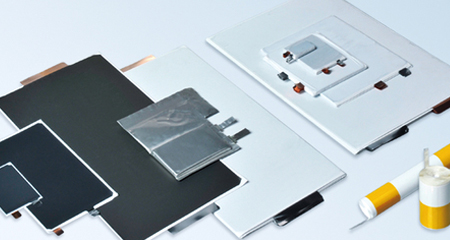
Energy Storage
-
- Manz AG是producti的主要提供者之一on equipment for lithium-ion battery cells, modules and packs as well as for capacitors. In this area, we have been setting standards worldwide for 30 years.
The storage of energy is a hot topic for the future. Successful energy transition requires an efficient storage medium, just as emission-free mobility does. Even in consumer electronics the quality of the battery determines the lifespan of the final product.
With our globally unique technology portfolio for the production of all current cell concepts — from wound button cells to stacked pouch cells — we play a major role in the continued development of lithium-ion battery technology.
We offer our customers individual machines for laboratory production, equipment for pilot and small series production, complete assembly lines and turnkey solutions for battery manufacturing. All system concepts are distinguished by their high production speed, high precision and reliability.
Our product portfolio covers the following range:
- Production solutions for lithium-ion batteries, super-caps and capacitors in e-mobility
- Production solutions for lithium-ion batteries and capacitors in stationary energy storage for private households and large photovoltaic systems
- Production solutions for lithium-ion batteries in electronic devices, such as tablet computers, mobile phones and laptops
Our services range from battery cell production — reel/sheet to cell — to assembly of individual battery cells in a battery system — cell to pack.
-
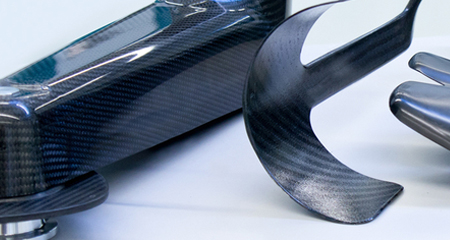
New Business
-
- What today is unimaginable or prohibitively expensive, may be a mass-market item tomorrow. Manz is always tracking the latest trends that open the way to the future. Our New Business unit is the nucleus for innovative, trailblazing technologies in a number of industries.
Besides development of machines and processes in lightweight design and work on solutions for fuel cell production, the New Business unit also identifies the latest growth markets of the size and potential to be the basis of a new Manz business segment.
For this reason market developments and trends are intensively watched and evaluated for their potential. The goal is further diversification of the customer and product portfolio to sustainably strengthen our company. For this, it is crucial that a technological, market-related business idea matches the company’s strategic orientation. If this is the case, the New Business area collaborates with customers to develop prototypical production machines and innovative processes.
-
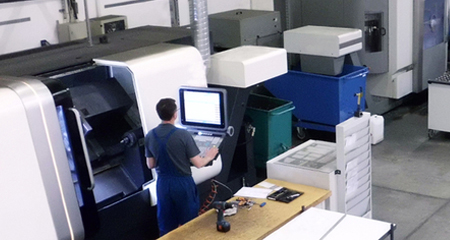
Contract Manufacturing
-
- With innovative ideas, our expert teams with decades of know-how, as well as state-of-the-art and extremely well-equipped production facilities in Europe and Asia we are a leading high-tech partner for mechanical and systems engineering, assembly, and parts manufacturing for a variety of customers in various branches.
As an engineering specialist, Manz has nearly 30 years of experience in
- planning and designing,
- building customized and standard machines,
- assembly and clean room assembly,
- manufacturing parts.
在世界范围内,我们的客户,主要的汽车and semiconductor industries, rely on our skills and our global production network.
Increasing the efficiency - not only in bottleneck situations - and the reduction of internal complexity are decisive factors for cooperation with Manz in the field of contract manufacturing for our customers.
For us, the strategic importance of this segment is to increase the flexibility within our own core business by balancing the volatile development of our growth markets.
Technologies
- Manz has expertise in six technology sectors: automation, metrology, laser processing, wet chemistry, coating, as well as roll-to-roll processes. With this comprehensive expertise, we offer customers in many industries efficient system solutions for demanding applications. In this way we contribute to lowering the production cost of end products and to making them available to large buyer groups worldwide.
-
Automation
- Automation is a critical factor for production success. Only excellent automation solutions make it possible to achieve consistent high quality, high throughput, low production cost — and as a result — competitive prices. With almost 30 years of experience in countless applications, Manz has become a market leader in this area. Manz solutions handle sensitive materials, such as silicon wafers or glass, ceramics, plastics and even paper.
In 1990, after developing a pick-and-place handling system with SCARA robots for electronic components, Manz developed the first automation solution for crystalline silicon solar cells using SCARA kinematics. In 1994, the first 6-axis LCD handling robot was introduced to the Asian market. The automation system was designed to vertically load PVD equipment under cleanroom conditions.
We provide various types of robots with fast, precise handling and minimal breakage rates, but we also offer much more: Thanks to our outstanding capabilities in production planning, our customers worldwide rely on our complete cluster and total-fab automations with conveyor segments and robots. These are offered inclusive development, software and final assembly.
-
-
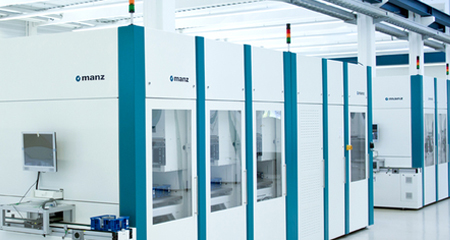
Assembly
-
- Manz offers efficient systems and equipment for fully automated assembly, optimally tailored to the needs of a broad range of industries. Especially in Asian countries, we have seen an increasing trend toward automated production. Factors driving this include the rising cost of wages, improvement of working conditions, demand for consistently high product quality and even issues like protection of intellectual property.
Our modular and fully automatic assembly systems build on our decades of technological experience in robotics, automation, image processing, and control and laser technology.
Our customers are producers and their suppliers and largely come from the consumer electronics and automotive industry.
Manz’s standardization of machine components offers an excellent cost/benefit ratio and short delivery times. At the same time, our equipment’s modular structure makes it simple to reuse machines over several generations of end products. These qualities are crucial to our customers’ investment decisions, because short product cycles are a given in their market.
Our high-precision, fully automated assembly systems have an integrated alignment function. During loading, transport and unloading, the components are fastened to workpiece carriers and transported through the system.
In combination with other process systems, our equipment is also designed for the following production steps:
- Input and output monitoring of components and completed devices
- Automatic component matching for achieving maximum quality
- Screwing or adhering components
- Applying labels (such as barcodes)
- Laser marking
- Laser welding
-
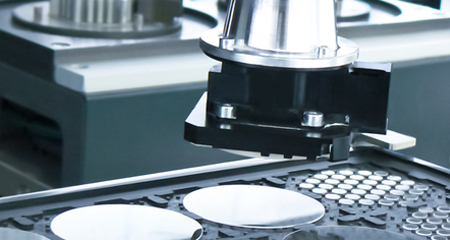
Robotics & Mechatronics
-
- With several thousand robotics systems installed, Manz has a long, successful history of automation solutions in the display and touch panel, solar and lithium-ion battery industries. And Manz has successfully transferred this expertise to many other industries and applications.
Manz’s product portfolio includes sophisticated, innovative solutions for substrate handling that stand out due to their low maintenance and high process quality. Thanks to low cycle times and minimal breakage rates, the systems’ low operating cost and high productivity are important factors in successful production.
Our services range from inline automation for loading and unloading process machines to complete automation and conveyor solutions with integrated buffer systems and built-in master production computer systems. Using high-performance image processing systems, we guarantee the lowest breakage rates along with the maximum machine availability. This also makes our automation solutions optimally suited for use under cleanroom conditions.
Our systems are mainly used for handling the following substrates, but can also be adapted to many other applications:
Handling glass panels
- 6- or 7-axis robot for vertical and horizontal handling of substrates
- 3- or 4-axis robot for horizontal handling of substrates or cassettes
- Cassette buffer system (FIFO, FILO, LIFO, etc.); substrates can be rinsed with inert gas or dry air to achieve longer storage times.
Handling small substrates, such as silicon wafers or glass
- smartphone covers
- Special Bernoulli gripper systems (Manz SpeedPicker) or delta robots
- Built-in optical control systems for alignment and inspection make mechanical alignment a thing of the past.
-
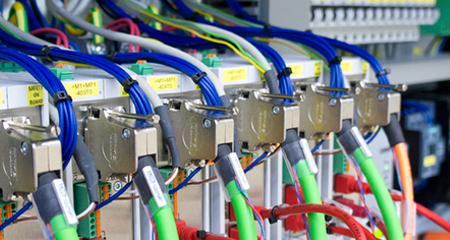
Machine Control & SCADA
-
- Manufacturing perfect products is only possible with precisely controllable, reliable production processes. High-tech production equipment from Manz has movement and robot controls, along with SCADA and HMI solutions, optimally tailored to the relevant production processes — plus, they are easy to operate.
Whether it is a robotics system for OEM customers or a fully integrated automation or process solution, the Manz group is your contact for comprehensive drive and control solutions. We develop, in close coordination with our customers, industry-specific solutions that are installed worldwide.
Our trend-setting solutions in robot and motion control for precise, dynamic applications include:
- Motion control for single- and multi-axis systems
- Various motion functions, such as flying saw, camming and gearing
- Robot controls (various kinematics)
- Control of roll-to-roll processes
- Servo and stepper motor drives, frequency converter technology
- Conveyor tracking
- Integrated image processing systems
For monitoring, controlling and visualizing production processes, Manz’s SCADA (supervisory control and data acquisition) and HMI (human machine interface) solutions offer:
- Configurable HMI and SCADA functions for
- Machine setup
- Machine operation
- Machine maintenance
- Order processing
- Recipe management
- Process monitoring
- Process and machine data management
- Analysis of historical data
- A manufacturing execution system (MES) interface
- A high-performance database and measuring technology interface
- An integrated visualization setup for HMI
- Scalable system for
- High-end SCADA (PC-based)
- HMI (PC-based)
- Mobile devices (tablet computer, smartphone)
-
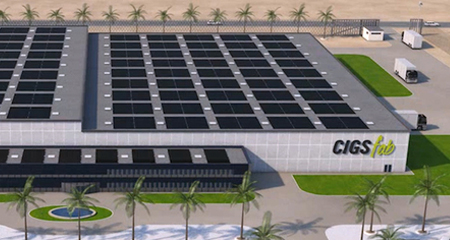
Simulation & FAB Planning
-
- Linked, multi-part production processes are highly complex. The consequences of individual events and parameter changes are often difficult or impossible to predict or evaluate. Using material flow simulation, processes can be optimized early and subjected to dynamic analysis. This helps to significantly improve the quality of production and machine design.
Simulation & Fab Planning
As a provider of integrated production lines and turnkey factories, Manz has plenty of experience in material flow simulation and analysis. Not only do we call on this expertise when designing our high-tech production equipment, we also offer it as a service: We assist our customers as early as the design phase or during analysis of existing production processes.
A dynamic simulation accompanies planning of production lines and factories throughout the project. The latest tools and methods are used to combine event-discrete and agent-based models. Even before a production line is commissioned, countless production years can be simulated.
A simulation’s results can show improvement potential and point out possible optimizations.
A material flow simulation and analysis can cover the following points:
- Stochastic modeling of key performance indicators (KPIs) of each individual piece of equipment
- Detection of bottlenecks and simultaneity factors
- Tests of critical situations (such as material blockages or bottlenecks, machine failure)
- Interactive control and observation of logistical issues
- Reliable design of buffer sizes and dimensioning of automation in a very early project phase
- Testing and optimization of operating concepts and maintenance plans
- Modeling of setup times and product changes
- Measurement of product-specific metrics, such as overall equipment efficiency (OEE) and overall factory efficiency (OFE) before production even begins
- Testing and development of production logics, significantly shortening the design, adjustment and commissioning of a manufacturing execution system (MES)
-
Patch Placement
-
- Using the flexible, fully automated patch placement method from Manz, various materials are fed from a roll, cut into contours – the so-called patches – using lasers and additively bound together into a component.
The patches are generally combined using a surface weld. Thus it is possible, similar to the 3D printing process, to generate a wide variety of component geometries from different materials. However, compared to 3D printing the patch placement method has higher material throughput and shorter production cycle times.
In addition, this method allows for the production of optimized fiber structure. The fibers are deposited accurate to the contour where they are needed with the lowest possible material cut. Components produced using this method are characterized by their low weight with uniform performance and reduced material usage.
The following roll material is suitable for the patch placement method:
- Plastic sheet
- Textiles
- Semi-finished fiber products
- Flexible materials
The Manz patch placement method is flexible: modified or even new products can be produced on a machine, without the need for costly retooling or even replacements.
Our flexible production technology thus faciliitates simple, fast product development as well as a highly flexible, automated production process. Complex component geometries can be produced economically with this – from one-off to series production.
There are many applications for the patch placement method, including aeronautics and aerospace, automotive manufacture, medical technology and also the consumer goods industry (for example: sports items).
Roll-to-Roll
- Ultra-thin, flexible, lightweight and cost effective is the trend for many of our customers in various industries. We are increasingly confronted with flexible OLED displays, circuits or solar cells that are integrated into everyday equipment, high-performance battery packs or catch phrases such as "Wearables" or "Internet of Things". Flexible electronics are an inherent part of these developments and one of the key technologies of the next decade.
In order to meet these challenges, the electronics industry is replacing conventional substrate materials, like the traditional glass and silicon wafers, by flexible materials such as thin glass, metal foils, and plastic substrates, which are generally referred to as flexible electronics (or flex circuits).
Manz在发展几十年的经验and construction of winding and stacking systems for the production of Li-ion batteries and capacitors. Our subsidiary Manz Italy (formerly Arcotronics) is a worldwide market leader for production lines of capacitors and batteries.
With this expertise we successfully established a Roll-to-Roll (R2R) process platform, which can be integrated in existing processing solutions and widely applied to various industries.
-
-
-
-
Flexible Material Handling
-
- Mainly driven by the consumer electronics and display industries, the handling of flexible materials becomes more and more important. Manz offers advanced roll-to-roll and roll-to-sheet solutions that can be integrated in various production technologies.
Flexible materials are indispensable in the production of flexible printed circuits (FPC), printed electronics, flexible thin glass, flexible solar cells, lithium-ion batteries, power caps, flexible OLED displays and more.
因此,精密卷绕对位(R2R)技术是一个雨淑缇al component for the process automation of flexible materials. Manz provides a highly integrated and scalable R2R system for different process applications that is equipped with standardized interfaces.
Advantages of our roll-to-roll technology:
- Coverage of a wide range of load, speed, material width and dynamic motion profiles
- Quick exchange of roll material
- Precise and highly dynamic process control capability for stable production processes (excellent tension control, even of ultra-thin foils)
Our highly integrated R2R process equipment solutions can be used in:
- R2R wet chemical processing
- R2R chemical bath deposition
- R2R slit coating
- Roll-to-Sheet (R2S) cutting
- R2R lamination and encapsulation processes
- Laser scribing and -ablation on flexible substrates
- Optical inspection of flexible substrates
- Packaging, sealing and welding of flexible substrate stacks
- Drying and curing of flexible substrates
Following flexible materials can be wound and unwound:
- Plastics and synthetic materials like PET, PE, PEN, PP…
- Metal foils
- Paper
- Wood
- Fabrics (e.g. textile, composite fibers)
- Prepregs (preimpregnated fibers) like carbon fibers or glass fibers
Metrology
- A core competence of Manz is the development of image processing systems. For over 25 years our customers have relied on our integrated optical control systems, physical measurement systems and integrated analytical instruments.
With Manz, the entire solution comes from one source: Process technology, including automation and integrated measurement technology. In this way we ensure high speed and precision, such as in positioning substrates, quality monitoring in the production process and in automatic optimization.
Our metrology solutions cover all relevant steps within a process chain:
- Testing after material feed
- Monitoring of integrated materials during production processes
- Final inspection
Manz has expertise in developing image processing systems: from the design of suitable optics, lighting and camera systems to programming the image processing algorithms. Thus, we can create optimally adapted measuring processes to significantly improve manufacturing. We operate a fully equipped metrology laboratory and can even perform studies on short notice. In addition, with fast experiment setups we can achieve short development times.
For years, our customers in various industries, such as entertainment electronics, lithium-ion batteries or photovoltaics, have trusted our products for:
- Camera-based and 2D and 3D geometric inspections, such as for tablet PCs and displays
- Surface inspection for scratches, breakouts, contamination or color errors
- Sensor-based 1D and 2D surface profile measurement, such as for laptop keyboards
- Measuring the hardness and layer thickness of chemically hardened glass
- X-ray fluorescence analysis
- Weighing electrolyte content and cell weight of batteries
We have comprehensive experience with a broad range of test objects, such as fluids, films and other flexible materials, glass, ceramics, plastic, semi-conductors, metals.
-
-
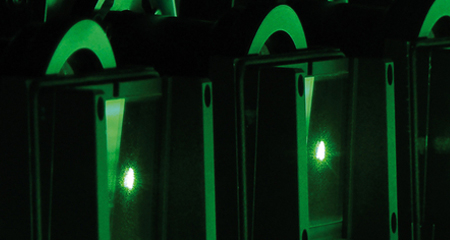
Vision & Optical Inspection
-
- Optical inspection of intermediate and end industrial products is indispensable when monitoring the quality of production processes. Manz delivers top-level image processing systems. They ensure maximum efficiency in a single system or an entire production line by immediately optimizing upstream and downstream processes. Higher quality and yield significantly reduce manufacturing costs.
Manz offers many means of image processing and optical inspection of a broad range of components or materials.
Part and position recognition
- Recognition of component positions for precise placement
- Easy teach-in of a broad range of product geometries
- Integrated joining processes with online regulation in the µm range
- 综合监管过程最大的precision when processing small-format substrates such as smartphone glasses
Dimension measurement
- High-precision measurement of stiff components such as smartphone components (< 10 µm precision incl. proof to a coordinated measurement machine) and flexible materials, such as carbon fiber patches
- High-precision measurement of process results (such as printing or laser processing)
- Measurement of gap dimensions (such as leaks between keys and housings)
Surface inspection and defect recognition
- Highly reliable surface inspection of a wide range of materials: glass, aluminum, thin-film solar modules
- Detection of defects or spots, such as missing coatings, contamination, remains from wet chemical processes, micro-cracks
Coating inspection
- Full-surface measurement of silicon nitride layers on solar cells in nm resolution (cell coloration reflects layer thickness)
- Measurement of wavelength-dependent transmissions of filter layers on small-format glass substrates (such as smartphone cover glasses) for inline quality control and regulation of the printing process
3D measurement
- 3D measurement of components for assembly with the smallest possible height offset
- Measurement of heights and levels of components (such as keyboards and laptop housings) for quality assurance at the end of a production line
-
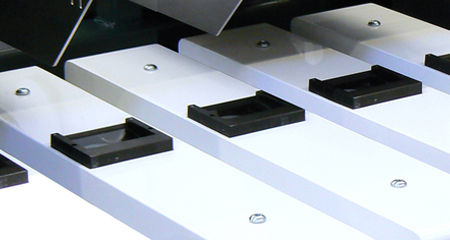
Physical Measurement
-
- In addition to image processing and optical inspection, Manz also has many years of experience in physical measurement technology. Our high-precision integrated solutions stand for optimal product quality and ensure zero-defect components.
Manz offers many physical measuring processes for a wide range of components and materials:
Electrical measurement technology
- Measuring the hardness and layer thickness of chemically hardened glass
- Measuring insulation resistance, such as in lithium-ion batteries
Weighing
- Automated weighing in the milligram range for e.g. battery electrolyte content
Spectral measurement technology
- Inline X-ray fluorescence analysis (RFA) for highly precise measurement of element concentrations or analysis of layer thicknesses and composition
- Spectrally resolved transmission measurement of filter layers in small-format glass substrates, such as smartphone cover glasses
Geometric measurement technology
- 2D profile measurement of gap dimensions and protrusions of laptop keyboards
- Tactile difference measurement in the micrometer range, such as for sealing seam thicknesses of battery pouch cells
- Depth measurement and stage measurement
- Thickness measurement and deflection measurement of substrates with optical 1D distance sensors (laser triangulation)
Force measurement technology
- Measuring the sealing force on film seals
- Force measurement for regulating robotic joining processes, such as of laptop components
Laser Processing
- Whether as a standalone system or part of a fully integrated production line: Manz laser processing equipment is the first choice — both for special applications and for mass production.
Our engineers draw on years of experience to develop the most current laser technologies and processes that help customers from many industries significantly increase the efficiency of their production processes.
In this way, we have carved out a leading market position in laser micro-processing for a wide range of applications. This includes cutting, drilling, structuring and welding many materials, such as glass, metal, ceramics, textiles and plastics, as well as ablation of layers such as compound semiconductors, metals and dielectric layers on large surfaces.
Our broad spectrum of processing techniques can be combined as desired: removing, applying, separating, joining, modifying — with Manz, you get it all from one source.
Like all of our machines, our laser processing equipment has optical systems for online alignment and quality control. Along with our intelligent automation solutions for parallel loading and unloading, and our equipment’s superior user-friendliness, we ensure our customers high productivity.
Our experienced R&D team works closely with the leading German laser research institutes in the fields of laser sources and optics. With their expertise and our modular machine designs, we can quickly develop new processes and systems for new applications.
After all, one of our greatest strengths is implementing precisely what the customer wants.
-
-
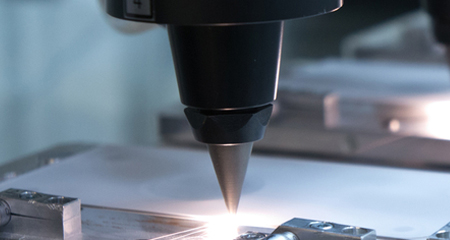
Cutting
-
- Manz offers fast, high-precision laser processes for cutting hard, brittle, flexible and plate -shaped materials.
Our laser cutting spectrum includes: cutting and slitting flexible material such as electrode foils and separators, cutting hard, brittle material such as glass (including float glass and thermally or chemically hardened glass) or sapphire, as well as plate-shaped materials such as printed circuit boards.
Cutting of hard, brittle materials
- Silicon
- Sapphire
- Glass
- Ceramics
Cutting (2D) and slitting non-rigid materials
- (Electrode) foils
- Separators
- Flexible printed circuit boards (FPC)
- Textiles, leather
- GRP fabrics and knits
Cutting of plate-shaped materials
- Sheet metal (ferrous and non-ferrous metals)
- Plastics
- Printed circuit boards (PCB)
衬底材料的大小是进程d can range from 2 inch wafers to Generation 8.5 glasses (2.200 mm x 2.500 mm). Workpiece sizes can range from square millimeters up to square meters.
-
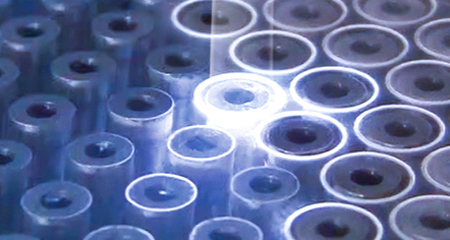
Drilling
-
- Manz covers a wide array of drilling processes for holes and openings with user-defined shapes in hard, brittle or flexible materials. Our offerings range from individual and in-line laser drilling equipment for architectural glass and photovoltaic substrates, to high-throughput systems for drilling holes in housings of electronic devices, such as smartphones, to equipment for drilling film.
Depending on the process, the following substrates can be processed:
Micro-drilling of hard, brittle and flexible materials
- Silicon
- Sapphire
- Glass
- Ceramics and ceramic films
- Printed circuit boards and flexible printed circuit boards
Macro-drilling of hard, brittle materials
- Sapphire
- Glass (float glass, hardened glass): mounting holes, bushings, pressure equalization holes
- Ceramics
Manz also has both the process expertise and the optical process technology for high-precision drilling at maximum throughput. In a recent project, 2,500 holes were drilled per second with a positional precision of ±2 µm on a 130 mm square machining area.
-
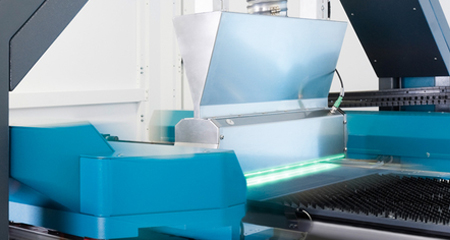
Scribing & Marking
-
- Laser-supported scribing and marking can be done on Manz equipment with high precision. Customers who have been with Manz for years value the equipment’s high throughput and optimal efficiency. Additionally, parallel process control contributes to reduced cycle times while maintaining the high quality.
Our many years of experience in laser processing technology, and our competent, flexible development team, allow us to offer individual and in-line equipment for selective removal of thin layers as part of scribing and marking. These can meet a wide range of requirements for use on substrates and workpieces.
- Monolithic series connection of thin film solar modules (including active position control by the Manz Inline Precision Control System - IPCS)
- Selective exposure of functional layers on glass or film (such as for electrochromic components, flat panel displays or touch panels)
- Marking with symbols or barcodes, such as on the back of smartphones or tablet computers
- Repair of color defects on anodized aluminum surfaces
- Workpiece marking with barcodes or dot matrix codes
- Internal laser marking of transparent workpieces
-
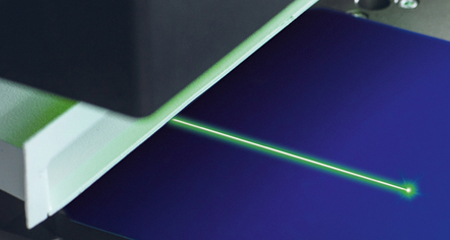
Ablation
-
- Thin-layer removal processes play a major role in many industries. Manz offers a complete portfolio of laser ablation equipment featuring very high throughput, maximum precision and stability for improving the quality and application rate of the end product.
Our ablation processes can be used on glass and flexible films, and for many other wafer-sized materials in small formats.
Processing steps that can be performed with our laser equipment include:
- Flat edge ablation on thin-film solar modules
- Partial ablation of thin film solar modules for use in building-integrated photovoltaics (BIPV)
- Exposure of coated electrodes before welding during battery production.
Further possibilities include partial ablation of electrically conductive layers on glass, such as windshields for IR and high-frequency reading applications or on glazing to prevent radar reflections.
-

Welding
-
- Manz已经发展成熟的焊接过程that produce unsurpassed seam quality with minimal use of energy. Possible applications range from spot welding of supporting structures in electronic devices, such as smartphones, to high-precision micro or macro welding of battery arrester contacts.
WOBBLING
Mixing of the molten metal is critical, particularly in the case of bimetallic compounds, because brittle phases can result. For that reason, in addition to conventional laser welding, Manz also offers a welding process that almost completely stops the molten metal from mixing, resulting in very high-strength weld seams: laser welding in the overlap using high-frequency local modulation, or “wobbling.”
Using wobbling the depth and width of weld seams are configured in the micrometer range independently of each other. Results with a welding penetration depth that is constant down to a fraction of a millimeter can be achieved in continuous operation with high wobbling frequencies and high intensities in the laser focus. At the same time, material inclusions can be reduced.
A fully calibrated 3D scanner, camera technology and topographical measurements ensure high precision in all spatial directions during processing, paired with the speed and flexibility of remote operations. In order to absorb component tolerances or to enable processing on different operational levels, the processing heads also have an optical Z-axis. This allows highly precise positioning of the operational level of the scanner in the Z-direction in less than 10 ms.
SHORT-PULSE LASER WELDING
In addition to wobbling, Manz offers an additional welding process for bimetals which is based on high-frequency temporal modulation of the peak power of up to several hundred kHz.
Short-pulse laser welding allows even greater stability in controlling welding penetration depth. By the inherent nature of the process, it is possible to create any weld seam or weld spot geometries of any shape, from 50 µm wide micro-seams to weld spots of several millimeters in diameter. The very low levels of input energy and the highly efficient process design result in minimal thermal load, which plays a particularly crucial role in thermally sensitive components.
Nearly any combination of materials can be welded, including aluminum, copper, steel, Hilan, brass, stainless steel, etc. The extremely stable and precisely adjustable welding penetration depth also makes overlap welds possible with sub-materials of 300 µm thickness and less. The welding process is also very flexible with respect to surface quality. For example, highly reflective materials, such as chemically etched or polished copper, silver or gold, or extreme contaminations and oil and alkaline residues pose no problems whatsoever. The use of conventional laser welding processes would be impossible in these cases.
In addition to conventional laser welding, Manz also offers a welding process that almost completely stops the molten metal from mixing, resulting in very high-strength weld seams. Laser welding in the overlap using high-frequency local modulation, or “wobbling”.
Using wobbling the depth and width of weld seams are configured in the micrometer range independently of each other. Our automatic calibration method for a two-axis scanner system allows a wobble frequency up to 4 kHz in continuous operation with constant welding depth to micrometer accuracy while simultaneously reducing material inclusions.
-
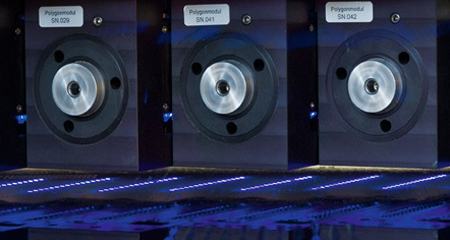
Laser Direct Imaging (LDI)
-
- With SpeedLight 2D Manz offers a laser direct imaging platform for the efficient production of high-resolution premium and XL printed circuit boards.
EFICIENT PRODUCTION OF PCBS WITH LASER DIRECT IMAGING
Manz拥有超过25年的开发经验ing high-tech equipment for the manufacture of high-efficiency printed circuit boards. A s a provider of wet chemical processing equipment Manz has earned a market leading position. Recently, the first systems were successfully installed at customers in Germany.
With the acquisition of KLEO Halbleitertechnik GmbH we could expand our technology portfolio with laser direct imaging of printed circuit boards. Our platform Manz SpeedLight 2D and its integration in the existing solutions for the manufacture of printed circuit boards make – in comparison with the conventional photolithographic process – an increase in the efficiency and flexibility of the product and the production process as well as significant cost savings of up to 75 %.
Wet Chemistry
- With more than 3,000 systems installed and almost 30 years of experience, Manz is the wet chemistry leader in Taiwan and China for production of displays and touch panels for substrate sizes ranging from smartphones to a format of 3,370 × 2,940 mm (Gen 10.5). Moreover, Manz offers the photovoltaic industry wet chemical processes for thin-film technology.
清洁Manz提供解决方案、涂料、plating (galvanic metallization), etching and stripping of various substrates and for reworking or removing complete coating systems for reclaiming valuable materials. This comprehensive spectrum of services is completed by high-level expertise in handling processes with potentially dangerous chemicals, such as hydrofluoric acid, nitric acid or lye. The fully automatic Inline Chemistry Analyzer ICA 001 also enables a real-time analysis and subsequent dosing of up to five chemicals for consistently high production results in wet-chemical processes.
The modular design of our systems and the transferability of the processes to other industries provide an outstanding cost/benefit ratio. Optimal productive time and process reproducibility ensure excellent returns with consistent product quality.
Our wet chemical process systems are designed for all inline processes. They are outstanding for processing glass substrates and printed circuit boards, and also flexible films (reel-to-reel process).
During development of the processes, machines and associated components, the main focus is on high process functionality. Additionally, we also consider the use of robust components, easy operation, high reliability and safety standards, as well as production yield. Even at high throughput, minimal breakage rates are achieved through material and chemical transport optimized to the process and substrate, while at the same time minimizing contamination or spreading in the system.
Our wet chemical technologies have proven themselves over decades in mass production. This means that we can offer process development and optimization, system design, simulation and construction all from one source.
-
-
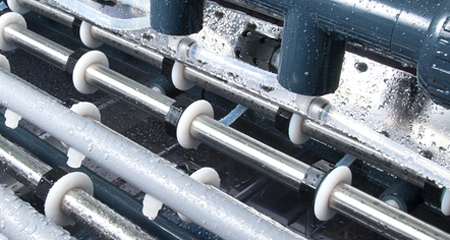
Cleaning
-
- Optimal cleaning of sensitive substrates is a prerequisite for the best results in downstream processes. Manz offers wet chemical cleaning systems for stiff and flexible substrates. The systems are highly effective, but gentle on materials.
Ever higher resolution structures lead to ever greater demands for substrate cleanliness. Manz cleaning systems reliably remove the smallest particles, dust and organic contaminants and therefore provide optimal conditions for further processing stages.
Our product line includes flow-through systems for cleaning a wide range of different substrates (e.g. glass, flexible materials).
这涉及到使用清洁中欧的多样性ologies, such as:
- Brushes
- Ultrasound
- Megasound
- High-pressure rinsing
Our systems therefore cover a broad spectrum of cleaning processes and possible substrates. These range from input cleaning of raw glass in display and touch panel production to cleaning substrates already coated (such as oleophobic coated glasses or semiconductor or PC substrates before copper deposition). Therefore substrate sizes from smartphones to a format of 3,370 × 2,940 mm (Gen 10.5) can be processed.
To properly supply the processes with the necessary cleaning chemical, we also provide the corresponding supply systems.
-
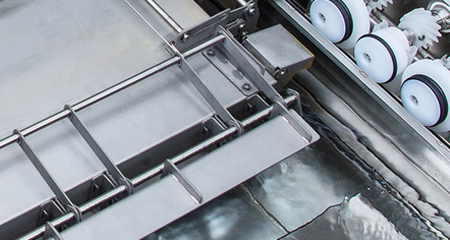
Coating & Plating
-
- Manz offers various coating and plating processes. Starting with copper galvanic and electroless plating in PCB production up to chemical bath deposition (CBD) in photovoltaics in the production of thin-film solar modules.
COATING
Chemical Bath Deposition (CBD) is an effective way to deposit thinner layers of CdS (cadmium sulfide) or alternative buffer substances, e.g. ZnS (zinc sulfide), onto glass substrates. Therefore, the CBD method is an important step in the production of CIGS or CdTe thin-film solar modules.
In the production of CIGS solar modules, the deposition of CdS serves as a very efficient surface passivation of the CIGS layer, establishes the CIGS/CdS hetero-junction (band alignment), covers shunts, and finally, protects the hetero-interface from damage caused by the highly energetic ZnO-sputtering process.
Based on our more than 20 years’ experience in the research and development of buffer layers, we created a fully automated inline CBD tool. With its compact design and footprint, the Manz ICBD (Inline Chemical Bath Deposition) system is a reliable and scalable tool for the use both in pilot and in mass production.
Our patented Butterfly Wobbling System provides an optimal mixing of chemicals and ensures exceptional process uniformity and the worldwide fastest process time (156 s for 50 nm CdS).
Highest tool uptime as well as the best process yield and uniformity ensure perfect processing results for high-quality, thin-film solar modules, while at the same time keeping costs at a very low level.
PLATING (METALLIZATION)
The metallization of through holes in the production of printed circuit boards (PCB) is traditionally done by a preparatory horizontal Desmear (DSM) process, followed by an electroless PTH (Plated-Through Holes) process and vertical plating. This process combination normally requires a complicated switch from horizontal to vertical goods transport within a limited timespan, to ensure that the substrates do not oxidize if they remain in the production process for too long.
佼佼者为了避免这种耗费时间处理,Manz developed a horizontal flash plating tool. In combination with the horizontal Desmear and PTH processes, our horizontal flash plating process makes metallization possible in one continual horizontal production line. Thus, handling and change from horizontal to vertical transport of substrates between the three processes is no longer necessary. The continuous goods transport not only saves process time, but also prevents damage of the surface during handling. By means of a single, integrated control panel, the three processes of DSM, PTH and flash plating can be easily controlled.
Our unique clamping devices ensure good mechanical conduct of the printed circuit boards and facilitate smooth transportation, while the current of each anode set is controlled independently.
Due to the height adjustable upper anodes for a quick initial metallization and the modular design, the machine can easily be adapted to the customers' request and is maintenance friendly with a minimized lead and installation time.
Equipped with a precise tension and edge position control, our flash plating tool is also suitable for the production of thin flexible printed circuit boards (FPCB).
-
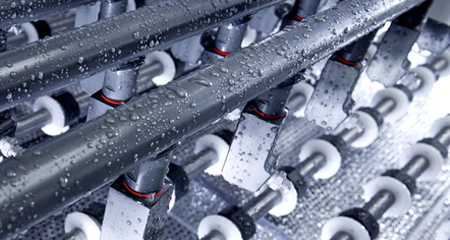
Developing, Etching, Stripping & Reworking
-
- Wet chemical processes for lithography development, etching and stripping are used in PCB as well as in display and touch panel production. Processes are also very important, in photovoltaic production etching. The product range of Manz covers all these important process steps and also includes wet chemical processing equipment for reworkingand/or cleaning.
Manz offers fully automated processing solutions for developing, etching and stripping of substrates. Our product range also covers wet chemical processing equipment for reworking – namely, the complete removal of all layers – so that expensive materials can be regained and substrates recycled back into the production process.
With decades of experience Manz has unique expertise in etching processes. They range from texturing to polishing (e.g. polishing of metal surfaces) to metal etching (e.g. copper etching on PCBs). All these processes are also available for single-sided etching (e.g. chemical edge isolation).
Many dangerous chemicals are used in etching processes. In case a central supply of chemistries like hydrofluoric acid, sulphuric acid or potassium hydroxide solution is not available, we also offer fitting chemistry supply cabinets.
Our etching processes can be applied to various substrates, such as glass or PCBs.
For the stripping of the photoresist we provide caustic processes (e.g., NaOH, KOH) as they are commonly used in PCB production, as well as organic processes (e.g. MEA, BDG) as often used in display production.
Services
- Service from Manz does not just begin with delivery of the equipment or its production start-up. We see ourselves as a development partner that works out solutions with our customer. That is why we support you ahead of time, during the many stages of development and construction.
-
-
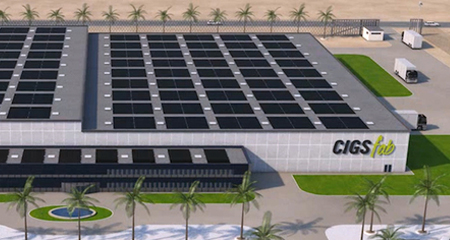
Simulation & FAB Planning
-
- As a provider of integrated production lines and turnkey factories, Manz has plenty of experience in material flow simulation and analysis. We also offer this expertise as a service: We assist our customers as early as the design phase or during analysis of existing production processes.
A dynamic simulation accompanies planning of production lines and factories throughout the project. The latest tools and methods are used to combine event-discrete and agent-based models. Even before a production line is commissioned, countless production years can be simulated.
A simulation’s results can show improvement potential and point out possible optimizations.
A material flow simulation and analysis can cover the following points:
- Stochastic modeling of key performance indicators (KPIs) of each individual piece of equipment
- Detection of bottlenecks and simultaneity factors
- Tests of critical situations (such as material blockages or bottlenecks, machine failure)
- Interactive control and observation of logistical issues
- Reliable design of buffer sizes and dimensioning of automation in a very early project phase
- Testing and optimization of operating concepts and maintenance plans
- Modeling of setup times and product changes
- Measurement of product-specific metrics, such as overall equipment efficiency (OEE) and overall factory efficiency (OFE) before production even begins
- Testing and development of production logics, significantly shortening the design, adjustment and commissioning of a manufacturing execution system (MES)
-
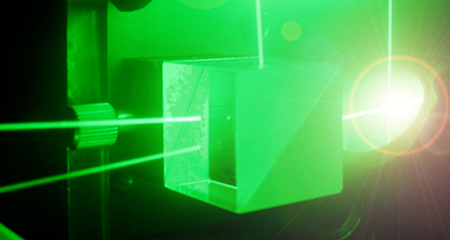
Process Development & Prototyping
-
- Would you like to optimize your production processes? Do you have solutions, but don’t know how to implement them quickly? Do you lack the opportunity to test new processes under realistic conditions? Manz is there for you, as a trustworthy, innovative development partner.
PROCESS DEVELOPMENT AND OPTIMIZATION
Manz can analyze your current and future production challenges and develop custom solutions for them.
Taking a complex look at materials, systems technology and process management, our specialists in six core technologies can quickly make processes successful — both new processes and those that have been tried but did not work well.
Moreover, we can perform complex process data evaluations and visualize them clearly – with the aim of automating and documenting reliable, reproducible and efficient processes. In the spirit of industry 4.0.
PROTOTYPE DEVELOPMENT & FEASIBILITY STUDIES
At our worldwide development sites, we can perform feasibility studies and develop prototypes to manufacture small unit runs semi-automatically and under realistic production conditions. We can provide feedback to actively support your product development process.
That is because designing a product early for automated production is crucial to its economic success.
Through the intensive collaboration of our specialist teams with the customer, process experience is gathered and the processes are quickly made ready for mass production.
If necessary, for a limited time end products can be produced at our sites on 24/7 shifts to support market introduction programs or to produce large batches for statistical process control that verifies the processes and equipment.
We are accustomed to maintaining strict confidentiality. This allows you to innovate while maintaining your head start on the competition.
We make mass production equipment at our production sites in Europe and Asia, depending on expense and characteristics. With our networked purchasing, logistics and equipment production, we can deal with challenging ramp-up schedules.
-
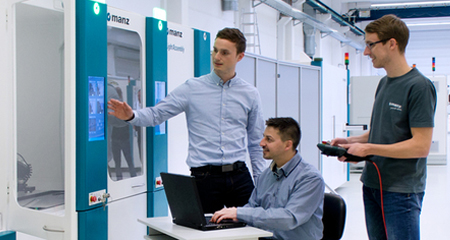
Customer Training
-
- High-tech equipment places high demands on personnel, whether it’s an individual machine, a whole line or a complex technological solution. This is true not only during start-up, but also during the production phase.
The better your people are trained, the more efficiently our machines work. For this reason, Manz offers a comprehensive training program that is avidly used, not only by our customers, but even by our own employees.
Our international training team has local trainers on site to conduct sessions in the respective national language both at our training
facilities and on the system — based on training concepts “Made in Germany”. Depending on the target audience, we offer various levels of training — from machine operators to process engineers to maintenance employees.
-
After-Sales Services
-
- Our close relationship with our customer does not end once our machines are delivered — it is only just beginning. Because wherever our machines are, you will also find Manz employees on site, making sure the machine does precisely what it was made for: Working efficiently.
Our round-the-clock customer service and quick delivery of replacement parts and accessories are just two important aspects of our customer support. Preventive maintenance and inspection, and machine reconditioning and upgrading round out our after-sales service.
Preventive maintenance and inspection
- Personal care — even after the sale
- Comprehensive, customer-specific maintenance contracts with specified intervals and individually customized maintenance components
- Customer service and consultation right at your site
- Qualified service technicians in Germany, the US, India, China, Taiwan and Korea
- Quick reaction times through local resources and close cooperation with our suppliers
- Repairs within two days after parts are delivered and available
Spare/consumable parts and accessories
- Advice on parts identification and recommendation of appropriate spare parts packages
- Worldwide replacement part management network via local service subsidiaries close to customers
- Large pool of used parts
- Repair and refurbishment service (also in local Manz repair centers in Europe, USA and Asia)
Modification and upgrade
- Increase of throughput
- Modifications of product dimensions
- Quality increases
- Cost savings
- Software updates
- Retrofitting
- Production relocation
Full Service
Upon request, we take over the complete maintenance of your machines and systems, including spare parts supply, over a specified period of time.
Build Operate Transfer (BOT) model
We operate your systems, organize production, take over all process including maintenance, entirely according to your requirements.