Videos
Loading the player ...
- Offer Profile
- plasmo Industrietechnik GmbH is the market leader in the field of quality assurance solutions for automated metalworking production. We are an innovative company that is absolutely specialized in the area of quality assurance.
While our headquarters are based in Vienna, we maintain a worldwide network of plasmo branches and partners.
Our customers receive from us solutions in the area of quality assurance that enable them to implement a secure, efficient and cost-optimized production.
Product Portfolio
Applications
- Produce Quality. Always.
我们发现质量保证溶解tions for automated metalworking production processes. Our solutions are independent from the plant or laser manufacturer. This is important because our customers wish to obtain the best solution for their own application.
Automotive
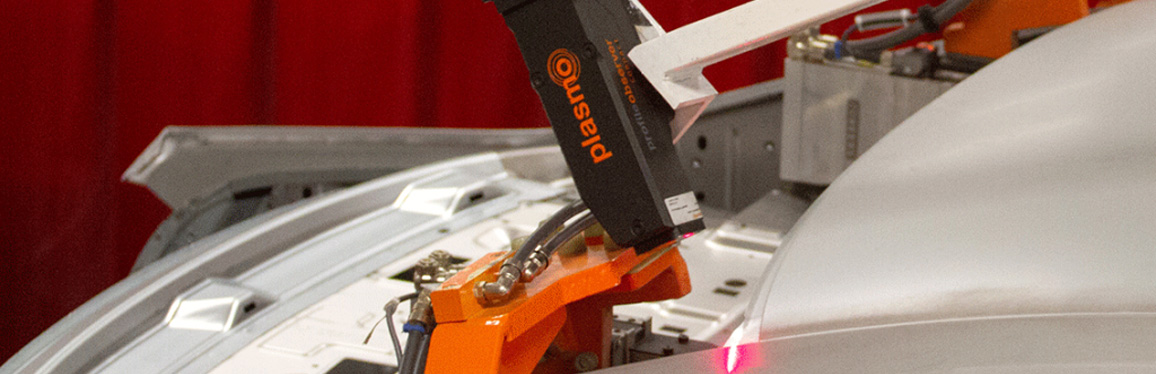
- SEAM INSPECTION FOR LASER BRAZING
At a glance
Seam Inspection for safety-relevant components, e.g. on roof seams, rear trunk lids and water channels of vehicles
Challenge
Automated welding and soldering is essential within industrial production for countless industries. Guaranteeing perfect quality through testing of high volume weld seams and an increasing number of variants require 100% error-free processes. Especially for brazed seams by robots, as there are for too few trained employees available for the visual inspection. Also, the requirements are particularly high when the “just-in-time monitoring systems” have to check the seam sections with traces of powder or smoke.
plasmo’s solution
Quality inspection plays a key role for repeatable and reliable product quality for metalworking manufacturing. To monitor and optimize laser brazing or laser welding seams, the plasmo profileobserver offers the perfect solution. The system recognizes, captures, analyzes and documents the seams as well as geometry and surface. Depending on the manufacturer, fault types and individual tolerances are defined according to internal and external standards. If the profile reading exceeds the specified tolerances, the profileobserver signals that the corresponding assembly (soldered seam) must go to the rework station and the error is displayed directly on the screen.
- Immediate result = no lost time or wasted cost
- Non-destructive
- Efficient
- Unproblematic integration into serial processes
- Features for additional evaluations
- Ease of use
- Flexibility
- Low-maintenance
Result – seam inspection
Through the use of an optical seam inspection system, it is possible to detect existing defects in the seam quickly to minimize cost and optimize the production process. This ensures that only parts with perfect quality are in the downstream production process. Also, all results are documented and stored for the further development and optimization of the soldering process while ensuring guaranteed quality assurance at all times.
-
Tubes and pipes
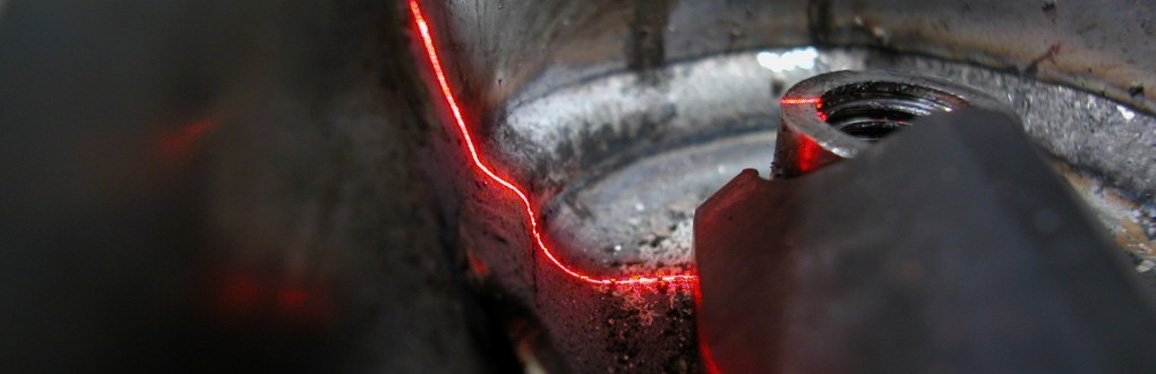
- QUALITY ASSURANCE FOR PIPES AND PROFILES
At a glance
Quality assurance for standard and endless pipes, tailored tubes and profiles requires innovative solutions. These can dramatically reduce manufacturing costs and rejects. Everyone knows the negative impact resulting from component failure – expensive production loss, extended downtimes, long inspection intervals or even safety risks are only some examples. In this context, process-monitoring systems can produce technologically relevant highlights.
Challenge
Continuously increasing requirements for quality and economic efficiency challenge customers to optimize products and production processes on an ongoing basis. In view of high productivity and the precision as a tool, these extremely fast processes are becoming constantly more significant in modern manufacturing technology. The implementation of high-tech systems for quality assurance in the production process can result in dramatic savings in weight and costs for simultaneously higher quality standards.
Our customers, for instance in the automotive sector, are among the major innovation drivers and an important sales market for pipes and profile manufacturers. Every vehicle includes many meters of (endless) pipe or pipe-like profiles (tailored tubes), even though invisible. The specifications defined by the EU for a reduction of CO2 emissions have resulted in significant additional challenges for manufacturers and suppliers.
plasmo’s solution
During the welding of pipes and endless profiles, the aspects of ease of welding must additionally be considered. Many issues are relevant, from the design of complex profiles and suitable materials through to the ease of the manufacture. Practical quality assurance is particularly important in this context. In many pipe/profile systems, the weld is no longer visible and any control must be performed inline. In addition, it is crucial that any defects are identified immediately so that the cause can be remedied as quickly as possible. As a result, rejects can be reduced significantly.
的plasmotest sequences are as follows:
- Process visualization: Identifying the potential for production increase and statistical analysis of the processes. In addition, improvement of the process understanding by system operators as well as detection of systematic errors.
- Fault detection through OK/NOK decision: This involves the definition of faults, the elimination of defective parts directly during or after the process. The goal is a 100 percent fatigue-free and objective control of the entire weld.
- Accurate meter-by-meter traceability: Continuous control of interrelations of multiple productions steps ensures subsequent analysis and definition of critical sections.
Selection of the testing equipment
Sensor- and camera-based test procedures as well as ultrasound offer solutions for a wide range of technological challenges for processing speeds of up to 80 -120 m/min, in- and online. From the visualization of the processes and fault detection through to the traceability of components and production steps. Modern online systems are used to ensure early detection of cracks, damage, edge offset, pores or pressure of rollers, etc., that might be produced during the welding process.
Result – quality control
Cracks and damage produced in the welding process are detected early by an online monitoring system and are identified by a time-delayed marking system on the profile or pipe in endless processes. Particularly in the case of stainless steel pipes, these online systems could under certain circumstances reduce the extent of eddy current or radiographic tests, which in some cases are required by law, as rework can be completed beforehand.
An online monitoring system detects cracks and damage from the welding process at an early stage and is characterized by a time-delayed marking system on the profile or pipe during continuous processes. Due to these online systems, the partly legally prescribed tests with eddy current or x-ray can be reduced, especially for stainless steel tubes, since a post-processing can take place first.
-
Additive Manufacturing
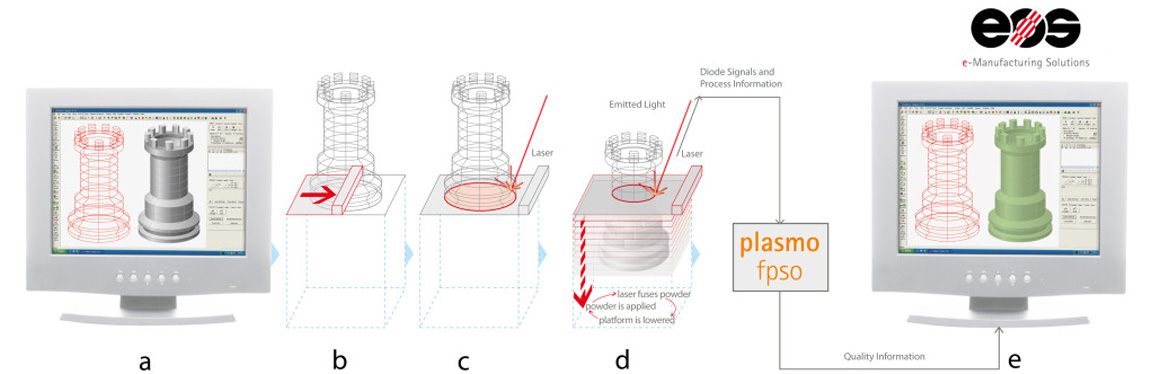
- ADDITIVE MANUFACTURING
At a glance
Engineers have always aspired to design parts without having to take the restrictions of conventional manufacturing methods into account. 3D printing using metals offers new possibilities with high geometric freedom. Even though the market for this manufacturing technology is currently relatively small, this technology is predicted to offer great future potential. Sales of 3D printing systems, the service of these and the respectively required materials are expected to quadruple to € 6.8 billion in the next 10 years.
Challenge
For optimal utilization of the manufacturing process even in safety-critical applications, such as, for example, in medical technology or in astronautics, essential requirements must be fulfilled. These include an understanding of the manufacturing process, the knowledge of the achievable, directional mechanical-technological properties as well as the use of appropriate quality assurance systems. The 3D printing systems for metals currently available in the market are exclusively controlled, resulting in an increasing demand for controlled systems in the industry.
As part of the PAM project, the in-situ process monitoring for injection molding applications was developed, among others, which is a manufacturing process that produces components by horizontally or vertically joining volume elements, mostly in layers. The 3D printing process represents the shortest way for developing a product, from the idea through to market maturity. The process allows for unproblematic manufacture of even the most complicated geometries. Conventional manufacturing methods, such as turning or milling, quickly reach their limits. As a result, there are almost no more restrictions in the design, thanks to which the geometric freedom is among the most important strengths his process has to offer.
The basis for making components from powdered metal are 3D CAD data that are used for generating the physical layers. Following application of a new powdered layer, the metal particles are solidified by application of energy in the form of laser radiation, which produces a locally restricted weld pool.
As presently only controlled systems are available and it is presently not possible to detect the above-described fusion defects in the construction process, the industry has a growing demand for controlled systems. The area of use of metal 3D printing is restricted due to the lack of quality assurance in many industries. Based on the detected fusion defects, a fault pattern could be defined for the quality assurance system to be developed. One approach towards implementing this process monitoring consists in the use of a photodiode-based measuring system that detects the process light produced when melting on the powdered metal. The thus determined measured values together with additional machine parameters represent the basis for monitoring the welding process.
Solution
所有工作相关的实现过程ss monitoring system are carried out on a laser sintering system for EOSINT M 280 type metal parts from the manufacturer EOS. Application of energy is by 200 W ytterbium fiber laser with 1064 nm wavelength. The overall installed size of this system is 250×250×325 mm.
The photodiode-based plasmo fastprocessobserver measuring system is implemented at two different measuring positions. One of the measuring positions is located within the process chamber while the second one is situated outside on the camera adapter of the scanning optic. In the process chamber, the reflected light is captured by four fiber optic cables of a quadruple fiber oriented towards the construction platform. At the camera adapter, the reflections are detected directly in the laser beam path, also by fiber optic cables. The fiber optic cables of both measuring positions ultimately lead to the measuring system comprising the plasmo fastprocessobserver, which converts the optical signals of the fiber optic cables via photodiodes into corresponding electrical signals. These are then recorded via high-speed modules of a data acquisition system. Aside from the process light, this data acquisition system also records other machine data, such as for example the scanner position. One measured data file is produced for each layer and is used as the basis for evaluations.
The recorded process data is evaluated using specifically developed algorithms that include statistical evaluations for every layer. These comprise, for instance, mean value and standard deviation of the reflected radiation, relative distribution of the voltage readings of the process light for a division into voltage ranges, current welding angle, etc.
A CT scan of the samples was produced to assign the recorded process data to the produced component. This shows a significant increase in the number of inclusions in layers exposed to reduced laser output. Based on the evaluation algorithms, in particular the algorithm used for allocating the recorded process light to the corresponding scanner position, this inclusion should then be recovered in the logged process data.
Result
The following procedure was applied to find the imperfections, which were present according to the CT scan, in the recorded process data: As it was not known beforehand what made up the inclusion in the recorded process light at the two measuring positions, the area where the fault could be found had to be restricted first. Owing to the high resolution of the CT scan, the area could be restricted to a few layers having a thickness of 0.03 mm in the direction of the design height. According to the CT scan, the inclusion to be found extended over 6 layers. By investigating the time sequences of the recorded process light, it was eventually possible to detect the air inclusion in 5 layers.
Once the fault had also been identified in the process data, the measured scanner position was used to allocate the time signals locally – referred to as localization – so as to determine its recorded position on the construction platform. This could successfully be done through appropriate parametrization of the algorithm.
-
Customized solutions
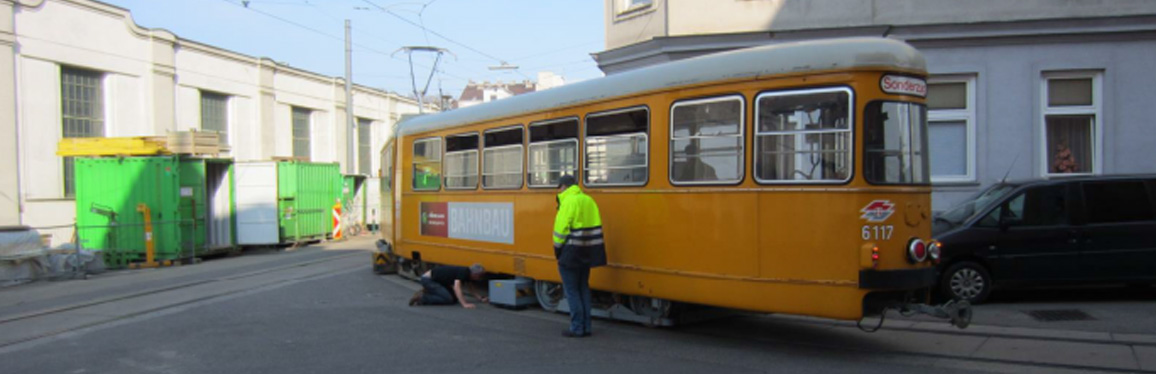
- RAIL MEASUREMENTS
At a glance
的plasmorailobserver was developed with various project partners as part of the research cooperation project “plasmaTram”. The defined task was to measure the entire rail network of Vienna tramway with unprecedented accuracy to achieve early detection of any abrasion or defective spots that place high stress on the rails and, time and again, result in interruptions in tramway traffic.
Thanks to a very fast camera technology, the geometry of the rail can be measured with the highest accuracy at a driving speed of 60 km/h.
Challenge
The control of any rail damage requires absolute precision, repeat accuracy and stability. The measurement and evaluation software required for the measurement system was developed. Several criteria had to be fulfilled in the process.
On the one hand, it had to be ensured that the staff driving in the measuring vehicle received live values displayed on the monitor during the measurement travel to be able to detect any significant defects on the rails immediately.
This task required the processing of large data amounts and the calculation of the necessary measured variables in real time. In addition, these data amounts had to be displayed and saved in real time to facilitate subsequent archiving in a maintenance database and availability for further analyses.
Solution
的plasmorailobserver was integrated into the measuring vehicle of Wiener Linien. It was thus possible to test the measuring system repeatedly in the urban environment under real-world conditions and to adapt the thus derived findings and general conditions to achieve the best possible measurement results. A special bracket had to be developed and manufactured for optimal integration of the measuring system in the measuring vehicle. In addition, the entire wiring was integrated and a separate measuring station for the system was created. In order to achieve the required high accuracies, the prototype used lasers operating at a high light energy.
In addition, a special compression algorithm was developed that compressed the data in real-time and without any loss by about 90% to a tenth of its original size and that allowed for efficient access to individual profiles even in ranges of hundreds of gigabytes.
To ensure that the plasmo railobserver met the requirements in the road network, the optical system was designed to withstand the dynamic challenges. In addition, special calibration elements were developed with the goal of achieving an absolute calibration of the measuring system and, in subsequent continuous operation, to provide the operator with the option to check the necessity for re-calibration at periodic intervals. Furthermore, an accurate optical measurement was required to measure and to compare the two rail tracks on an absolute basis. The thus derived measured variables (e.g. track width) were crucial. Thanks to the high resolution of the system, it was discovered in the course of the project that elements left and right of the rail could also be recorded and measured.
Result
The system will provide an even greater benefit in future. In particular, the prototype now permits reliable detection and measurement of rail track structures, such as e.g. switches, switch tongues, crossings, etc. As a next step, continuous monitoring of these elements will in future be automated with unprecedented accuracy. The goal is to utilize the findings gained in this project to contribute towards an automated maintenance schedule and to consider subsequent development steps with regard to potential use in the subway area. The long-term goal is to establish a rail monitoring system for the urban area capable of covering various rail types also at international level. (e.g. grooved and flat-bottom rail).
-
Process Chains
- 从pl生产线综合测试系统asmo guarantee the currently highest possible quality in industrial production in real time. While camera-based systems are predominantly used in the pre- and post-weld sectors, diode-based solutions have become the standard for inline tests.
-
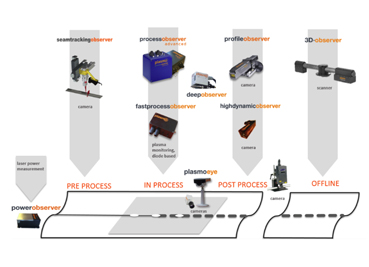
Quality assurance products for joining processes
-
- 从pl生产线综合测试系统asmo guarantee the highest possible quality in industrial production in real time. While camera-based systems are predominantly used in the pre- and post-weld sectors, diode-based solutions have become the standard for inline tests.
-
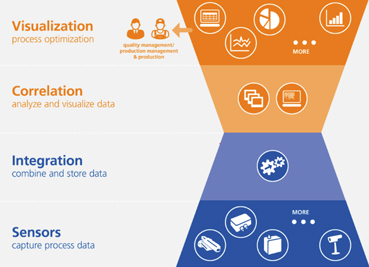
plasmo Quality Suite
-
- We work on the individual problems of our customers and find solutions. The plasmo Quality Suite comprises 3 levels.
-
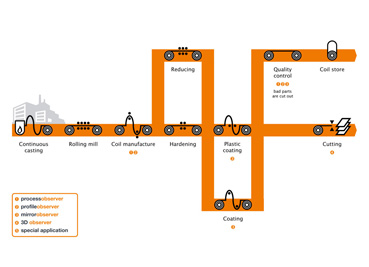
Coil manufacture process chains
-
- The visual presentation shows the process of chain of coil manufacture and processing. From the delivery via diverse production steps through to the finished products. Example of the application of plasmo solutions are also listed.
-
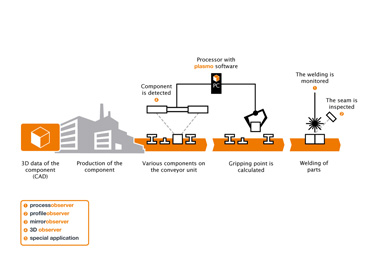
Automated component handling
-
- This graph illustrates the process chain in automated production on the example of the manufacture of a steel girder used for bridge construction. Based on the 3D CAD data of the respective, freely selectable component, the position of these is detected on the conveyor of units following production (plasmo solution: 3Dobserver). Testing of the subsequent welding process can be done either during welding (plasmo solution: processobserver series) or after completed process (plasmo solution: profileobserver series)
-
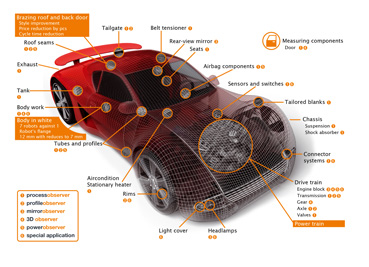
Automotive
-
- You can find an overview of our solutions and thei possible applications on the vehicle here. The indicated numbers refer to the plasma product that can be used for the corresponding application or solution.
PRODUCE QUALITY. ALWAYS.

- Depending on the material and product specification we use for testing the joints different technologies. Metals, mixed compounds and plastic parts are welded or glued, assembled and mounted. Metal parts are soldered, screwed, welded or pressed into the plastic compound. The respective testing method depends on the product and the request.
-
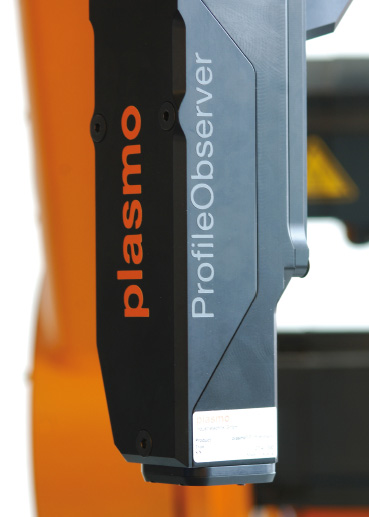
profileobserver compact
-
- 的plasmoprofileobserver product family stands for highest precision in the fast and reliable detection of surface defects such as seam elevation, edge notches, cracks, splashes, seam width, seam position pores and other geometric forms.
Features/Benefits
- Non-contact and non-destructive (NDA)
- High-speed vision system (max. 30,000 images/s)
- Precise measuring results with high dynamics
- Almost independent of the surface
- Reduction of the production costs through early detection of defects.
- Reliable detection of the surface defects:
- 焊缝高度/下降
- Edge notches
- Cracks
- Splashes
- Seam width
- Seam position
- Pores
- Changes in laserpower
- 焊接速度的变化
- Statistics modules and trend analysis modules
- Subsequent traceability up to the seam
- Seamtracking
-
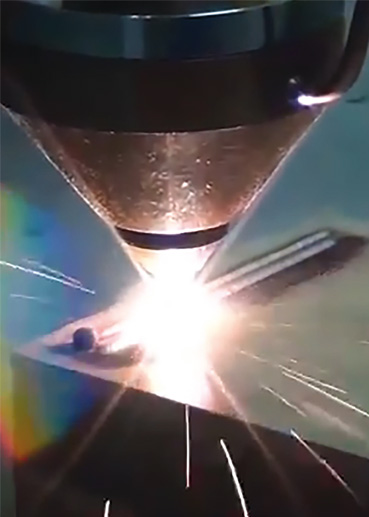
fastprocessobserver
-
- Fast Quality Inspection
- Extremly fast: Quality inspection for very fast laser processes
- High adaptablility: Customized software development
- QS for new ranges: Laser cutting, additive manufacturing, laser cleaning, pulsed laser welding, powder coating, cladding, …
- Improved production by self-learning process
-
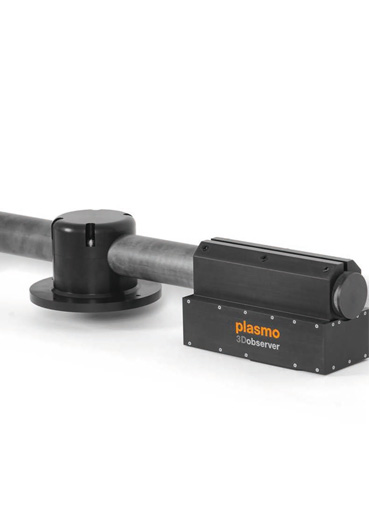
3D observer
-
- The 3D observer is an optical sensor system capable of fully identifying, capturing and measuring three-dimensional objects and their location in a space (in relative or absolute coordinates). It then supplies these data to a robot or linear axis system, for example, as commonly employed in many automated production processes. The 3D observer provides information regarding the location, the 3D contour or gripping point of objects in the production chain. It is also capable of solving tasks which require the simultaneous use of both 3D and 2D optical technology. The process is flexible, extremly quick and does not depend on the material or the colour and is almost independent from the surface. Thanks to the high processing speed, this unique 3D scanning process allows 100% control of the production process.
-
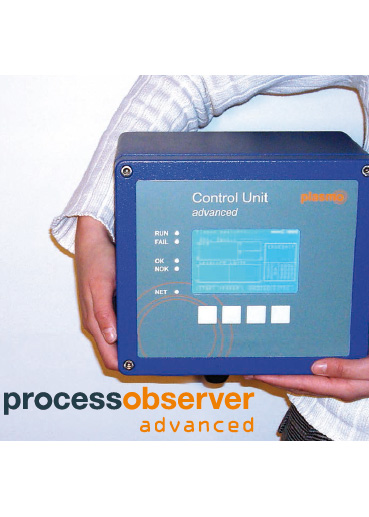
processobserver advanced
-
- 的plasmoprocessobserver advanced offers you a hi-tech device that monitors and documents welding, cutting and drilling processes in real-time without damaging the workpiece. All data recorded is available for a detailed offline analysis.
The advantages
- An automatic quality control system is integrated into the production process.
- Failures are recognised immediately; whithout damaging the workpiece during the analysis.
- All production data is comprehensively recorded and documented in accordance with ISO 9001/2.
- Any quality defect is traceable.
- Statistics modules and trend analysis modules are used to evaluate the data.
- The long-term statistical evaluation functions of the processobserver advanced are an effective way to optimise your processes!
- The entire welding process can be optimised to reduce production costs.
- The offlinereader and offlinesimulation- software can be used to diagnose systematic welding errors.
- The person responsible is able to monitor and control the process, allowing to reduce the number of defects produced considerably.
-
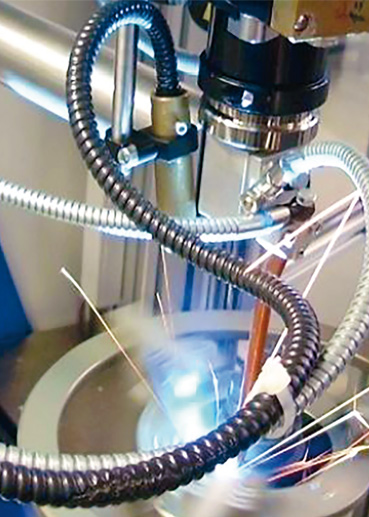
processobserver basic
-
- Easy Quality Control
- Plug & play: Fast and easy system setup
- Complete solution: Sensor, data storage, software, offl ine tools
- Process inspection: Where the process happens
- Real time monitoring: Using fi bers on the welding head, contact free, non destructive
-
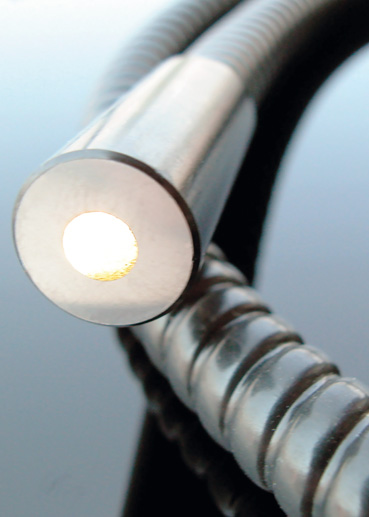
fiberobserver
-
- 的plasmofiberobserver checks the quality of optical fibers which are used for example in the plasmo processobserver series. The easily transportable hardshell service case (dimensions approx. 33 x 27 cm/13 x 11 inch) contains:
- Camera with adjusting device
- Different fi ber adapters for all types of fi bers
- Software for description, administration and data storage of the test results
- Appropriate tools for the use of plasmo fi berobserver
- The check is based on the transmitted light method. The smooth quality assurance
- process of plasmo processobserver series is reliable supported by the plasmo fi berobserver.
-
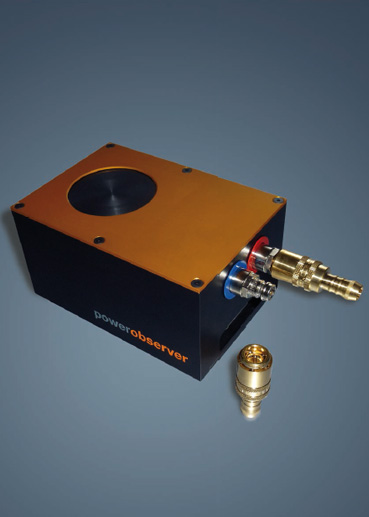
powerobserver advanced
-
- The powerobserver advanced is a new innovative measurement system for inline laser power measurement.Its compact construction makes it easy to integrate into a wide range of laser systems. Its design enables short repeat measurements. It is thus possible to check the laser power during the production process using a short-time measurement. Long-time measurements allow the visualisation and examination of the performance over a longer time range. These measurement programmes rate the measured performance as OK or NOK. The results and the determined performance can be displayed on the laser system monitor and made available to the device via various field bus systems.
-
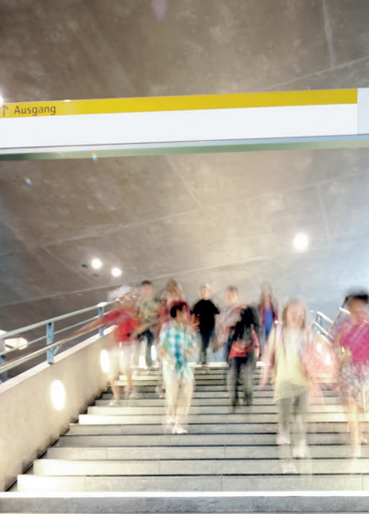
visplore专家
-
- Controlling a production – statistical
process control
Preparing information from data and an appropriate aggregation of these information allows to control processes at offline work stations. In many cases it is useful to visualize quality control cards online which enables a fast and direct intervene for corrective
action.
-
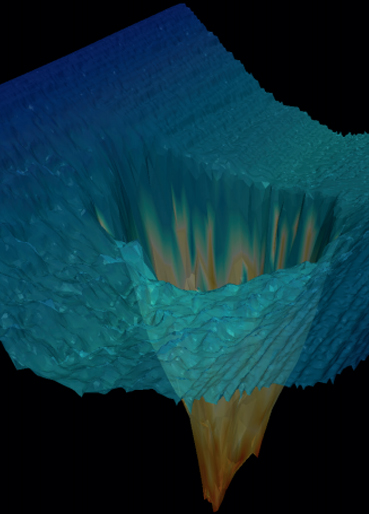
deepobserver
-
- absolute measurement of weld depth
焊透的闭环控制
3 measurement devices in one: welding penetration depth,
seam surface, seam &gap tracking
independent of welding optics
-
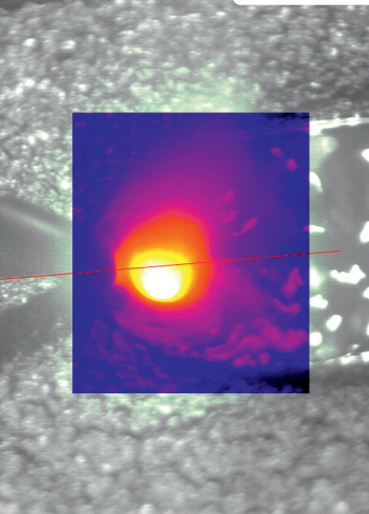
plasmoeye process
-
- process visualization & root cause analysis with
high dynamic camera, thermal analysis possible
客户特定的评估,准备关闭厕所p control
standardized fieldbus communication
statistical process control: up to 30% optimization
-
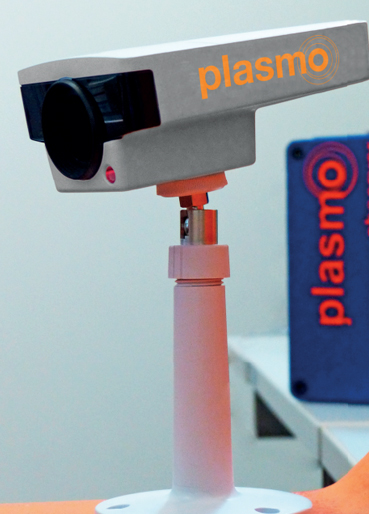
plasmoeye actioncam
-
- Always keeping an eye on your production process
Industrial actioncam provides a visual overview for your production process.
Capture component-specifi c images or videos for the entire laser process.
Draw conclusions about the error by seeing the root cause. 100% tracability by video.
Can be integrated with other plasmo solutions or used independently.