- Offer Profile
- Welcome to AMC Europe Ltd., European headquarters of ADVANCED Motion Controls, a world leader in servo drive solutions and precision motion controls, headquartered in California, USA.
ADVANCED Motion Controls was founded in 1987 to provide high quality servo amplifiers and drives for the rapidly expanding automated machinery demands in many industries. AMC’s focus is working with customers to develop and produce motion control amplifiers and drives capable of delivering from 20 W up to 48 kW peak.
ADVANCED Motion Controls has numerous standard products available but also provides custom products for OEMs with specific requirements or special option adaptations that meet their needs. Designs include both analog and digital technology covering a broad range of solutions. The newly introduced Digiflex® family offers multiple configuration capabilities, networking solutions, and provisions for optional software libraries to reduce programming time.
Product Portfolio
Servo Drives

Performance
High performance servo drives start with optimally tuned current loops with fast update rates, then progresses to velocity and position loops that match the machine's dynamics. FlexPro and DigiFlex Performance servo drives are easily tuned through software including the current, velocity and position loops. AxCent servo drives come configured with current loop tuning parameters that are suitable for most applications, but can be further optimized using traditional tuning methods.Power
Our servo drives range from 50W to over 20,000W of continuous power; with peak ratings typically double the continuous rating. We have a wide selection of sub-80V servo drives that are ideal for battery powered systems like mobile robotics and portable devices including IMR, AMR, AGV, medical and laboratory applications. Higher voltage servo drives are available from 120VAC to 480VAC as well as the equivalent DC voltage levels to cover most industrial applications.Network Connectivity
Supported networks include EtherCAT, CANopen, EtherNet/IP, RS485 and more. Machines can be readily adapted for Industry 4.0 and Smart Factories since most servo drive parameters are accessible by the controller over the network bus.Shape and Size
We make it easy for machine designers to find servo drives that physically fit into their applications by offering a variety of form factors. Panel Mount drives are typically found in factories and industrial settings, PCB Mount drives are perfect for tightly integrated systems, while machine embedded designs are a convenient blend of the two. Regardless of the form factor, performance is never sacrificed.
Analog Drives
-
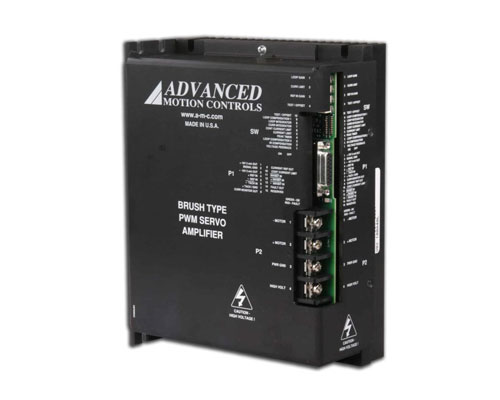
100A40
-
- Panel Mount:Classic
SPECIFICATIONS
- Current Continuous (A)50
- Current Peak (A)100
- DC Supply Voltage (VDC)80 - 400
- Network CommunicationNone
- Size (mm)235 x 183.2 x 92.4
- Weight (g)3410
The 100A40 panel mount servo drive is targeted for centralized control and offers high bandwidth and quick response times.
- CONTROL/COMMAND
±10 V Analog
- PRIMARY FEEDBACK
Tachometer (±60 VDC)
- OPERATING MODE
- Current
- IR Compensation
- Velocity
- Voltage
- MOTOR TYPE
Single Phase (Brushed)
-
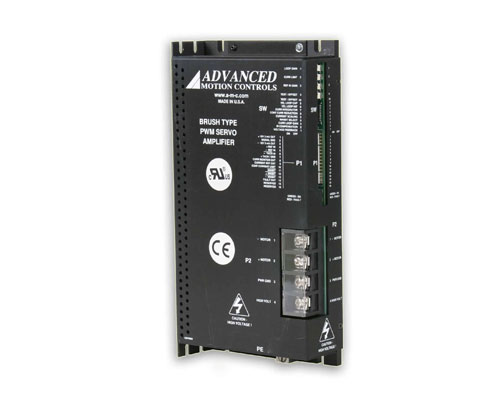
120A10
-
- Panel Mount:Classic
SPECIFICATIONS
- Current Continuous (A)60
- Current Peak (A)120 DC
- Supply Voltage (VDC)20 - 80
- Network CommunicationNone
- Size (mm)254 x 130.2 x 48.7
- Weight (g)1140
The 120A10 panel mount servo drive is targeted for centralized control and offers high bandwidth and quick response times.
- CONTROL/COMMAND
±10 V Analog
- PRIMARY FEEDBACK
Tachometer (±60 VDC)
- OPERATING MODE
- Current
- IR Compensation
- Velocity
- Voltage
- MOTOR TYPE
Single Phase (Brushed)
-
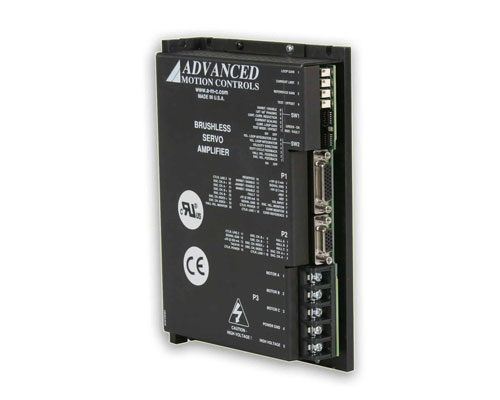
B30A40
-
- Panel Mount:AxCent
SPECIFICATIONS
- Current Continuous (A)15
- Current Peak (A)30
- DC Supply Voltage (VDC)60 - 400
- Network CommunicationNone
- Size (mm)203.2 x 142.9 x 40.7
- Weight (g)990
The B30A40 AxCent™ panel mount servo drive is targeted for centralized control and offers high bandwidth and quick response times.
- CONTROL/COMMAND
±10 V Analog
- PRIMARY FEEDBACK
- Halls
- Incremental Encoder
- Tachometer (±60 VDC)
- OPERATING MODE
- Current
- Duty Cycle (Open Loop)
- Hall Velocity
- Velocity
- MOTOR TYPE
- Three Phase (Brushless)
- Single Phase (Brushed)
-
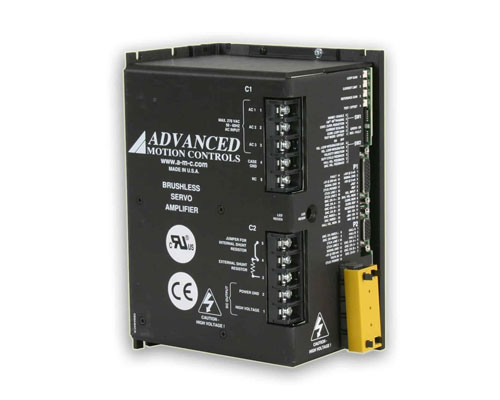
B30A40AC
-
- Panel Mount:AxCent
SPECIFICATIONS
- Current Continuous (A)15
- Current Peak (A)30
- DC Supply Voltage (VDC)60 - 400
- AC Supply Voltage (VAC)45 - 265
- Network CommunicationNone
- Size (mm)203.2 x 165.7 x 103.1
- Weight (g)2230
The B30A40AC AxCent™ panel mount servo drive is targeted for centralized control and offers high bandwidth and quick response times.
- CONTROL/COMMAND
±10 V Analog
- PRIMARY FEEDBACK
- Halls
- Incremental Encoder
- Tachometer (±60 VDC)
- OPERATING MODE
- Current
- Duty Cycle (Open Loop)
- Hall Velocity
- Velocity
- MOTOR TYPE
- Three Phase (Brushless)
- Single Phase (Brushed)
CONTROL/COMMAND
- ±10 V Analog
- Step & Direction (24V)
- Encoder Following
- Indexing Jogging
- Over the Network
- PWM and Direction
- Sequencing
PRIMARY FEEDBACK
- ±10 VDC Position
- Halls
- Incremental Encoder
- Tachometer (±10 VDC)
OPERATING MODE
- Current
- Hall Velocity
- Position
- Velocity
MOTOR TYPE
- Three Phase (Brushless)
- Single Phase (Brushed)
- AC Induction
- Stepper
Digital Drives
-

DPRAHIE-030A800
-
- Panel Mount:DigiFlex Performance
SPECIFICATIONS
- Current Continuous (A)15
- Current Peak (A)30
- DC Supply Voltage (VDC)255 - 747
- AC Supply Voltage (VAC)200 - 480
- Network CommunicationModbus RTU, RS-485/232
- Functional SafetySafe Torque Off (STO)
- Size (mm)300.5 x 231.3 x 91.4
- Weight (g)5437
The DPRAHIE-030A800 DigiFlex® Performance™ panel mount servo drive offers full tuning control of all servo loops and is designed for distributed or centralized servo systems. This servo drive utilizes RS485 or Modbus RTU communication and is commissioned with DriveWare® via an RS-232 interface.
CONTROL/COMMAND
- ±10 V Analog
- Step & Direction (24V)
- Encoder Following
- Indexing Jogging
- Over the Network PWM and Direction
- Sequencing
PRIMARY FEEDBACK
- ±10 VDC Position
- Halls
- Incremental Encoder
- Tachometer (±10 VDC)
OPERATING MODE
- Current
- Hall
- Velocity
- Position
- Velocity
MOTOR TYPE
- Three Phase (Brushless)
- Single Phase (Brushed)
- AC Induction
- Stepper
-
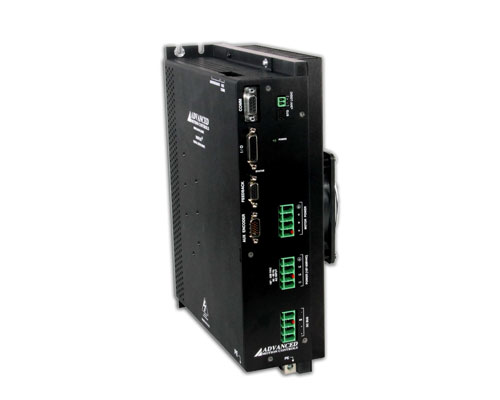
DPRAHIE-060A800
-
- Panel Mount:DigiFlex Performance
SPECIFICATIONS
- Current Continuous (A)30
- Current Peak (A)60
- DC Supply Voltage (VDC)255 - 747
- AC Supply Voltage (VAC)200 - 480
- Network CommunicationModbus RTU, RS-485/232
- Functional SafetySafe Torque Off (STO)
- Size (mm)300.5 x 231.3 x 140.91
- Weight (g)6165
The DPRAHIE-060A800 DigiFlex® Performance™ panel mount servo drive offers full tuning control of all servo loops and is designed for distributed or centralized servo systems. This servo drive utilizes RS485 or Modbus RTU communication and is commissioned with DriveWare® via an RS-232 interface.
CONTROL/COMMAND
- ±10 V Analog
- Step & Direction (24V)
- Encoder Following
- Indexing
- Jogging
- Over the Network PWM and Direction
- Sequencing
PRIMARY FEEDBACK
- ±10 VDC Position
- Halls
- Incremental Encoder
- Tachometer (±10 VDC)
OPERATING MODE
- Current
- Hall Velocity
- Position
- Velocity
MOTOR TYPE
- Three Phase (Brushless)
- Single Phase (Brushed)
- AC Induction
- Stepper
-
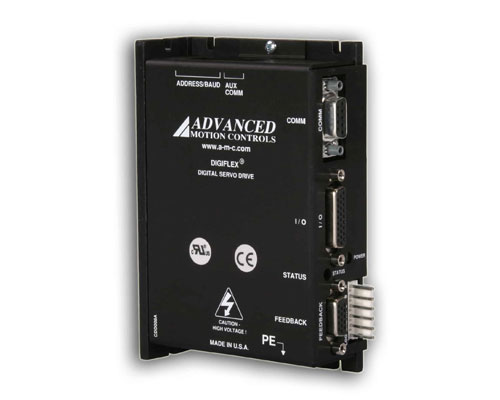
DPRALTE-015B200
-
- Panel Mount:DigiFlex Performance
SPECIFICATIONS
- Current Continuous (A) 7.5
- Current Peak (A)15
- DC Supply Voltage (VDC)40 - 190 Network Communication Modbus RTU, RS-485/232
- Size (mm)132.5 x 89.5 x 35.9
- Weight (g)486
The DPRALTE-015B200 DigiFlex® Performance™ panel mount servo drive offers full tuning control of all servo loops and is designed for distributed or centralized servo systems. This servo drive utilizes RS485 or Modbus RTU communication and is commissioned with DriveWare® via an RS-232 interface.
CONTROL/COMMAND
- ±10 V Analog
- Step & Direction (5V)
- Encoder Following
- Indexing
- Jogging
- Over the Network
- Sequencing
PRIMARY FEEDBACK
- ±10 VDC Position
- Halls
- Incremental Encoder
- Tachometer (±10 VDC)
OPERATING MODE
- Current
- Hall Velocity
- Position
- Velocity
MOTOR TYPE
- Three Phase (Brushless)
- Single Phase (Brushed)
- AC Induction
- Stepper
-
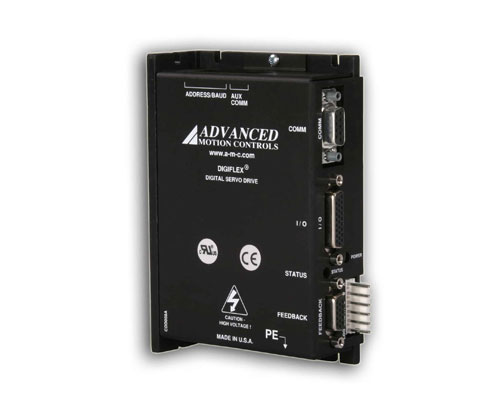
DPRALTE-020B080
-
- Panel Mount:DigiFlex Performance
SPECIFICATIONS
- Current Continuous (A)10
- Current Peak (A)20
- DC Supply Voltage (VDC)20 - 80
- Network CommunicationModbus RTU, RS-485/232
- Size (mm)132.5 x 89.5 x 35.9
- Weight (g)486
dpralte - 020 b080 DigiFlex®性能™面板ount servo drive offers full tuning control of all servo loops and is designed for distributed or centralized servo systems. This servo drive utilizes RS485 or Modbus RTU communication and is commissioned with DriveWare® via an RS-232 interface.
CONTROL/COMMAND
- ±10 V Analog
- Step & Direction (5V)
- Encoder Following
- Indexing
- Jogging
- Over the Network
- Sequencing
PRIMARY FEEDBACK
- ±10 VDC Position
- Halls
- Incremental Encoder
- Tachometer (±10 VDC)
OPERATING MODE
- Current
- Hall Velocity
- Position
- Velocity
MOTOR TYPE
- Three Phase (Brushless)
- Single Phase (Brushed)
- AC Induction
- Stepper
-
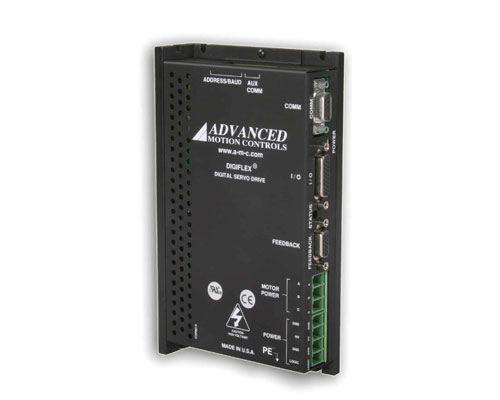
DPRALTE-025B200
-
- Panel Mount:DigiFlex Performance
SPECIFICATIONS
- Current Continuous (A)12.5
- Current Peak (A)25
- DC Supply Voltage (VDC)20 - 190
- Network CommunicationModbus RTU, RS-485/232
- Size (mm)190.5 x 111.8 x 35.9
- Weight (g)872
The DPRALTE-025B200 DigiFlex® Performance™ panel mount servo drive offers full tuning control of all servo loops and is designed for distributed or centralized servo systems. This servo drive utilizes RS485 or Modbus RTU communication and is commissioned with DriveWare® via an RS-232 interface.
CONTROL/COMMAND
- ±10 V Analog
- Step & Direction (5V)
- Encoder Following
- Indexing
- Jogging
- Over the Network
- Sequencing
PRIMARY FEEDBACK
- ±10 VDC Position
- Halls
- Incremental Encoder
- Tachometer (±10 VDC)
OPERATING MODE
- Current
- Hall Velocity
- Position
- Velocity
MOTOR TYPE
- Three Phase (Brushless)
- Single Phase (Brushed)
- AC Induction
- Stepper
-
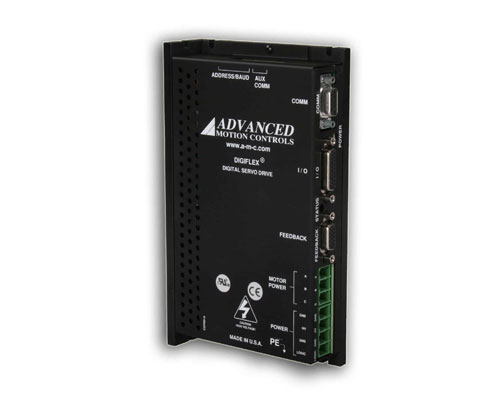
DPRALTE-040B080
-
- Panel Mount:DigiFlex Performance
SPECIFICATIONS
- Current Continuous (A)20
- Current Peak (A)40
- DC Supply Voltage (VDC)20 - 80
- Network CommunicationModbus RTU, RS-485/232
- Size (mm)190.5 x 111.8 x 35.9
- Weight (g)872
The DPRALTE-040B080 DigiFlex® Performance™ panel mount servo drive offers full tuning control of all servo loops and is designed for distributed or centralized servo systems. This servo drive utilizes RS485 or Modbus RTU communication and is commissioned with DriveWare® via an RS-232 interface.
CONTROL/COMMAND
- ±10 V Analog
- Step & Direction (5V)
- Encoder Following
- Indexing
- Jogging
- Over the Network
- Sequencing
PRIMARY FEEDBACK
- ±10 VDC Position
- Halls
- Incremental Encoder
- Tachometer (±10 VDC)
OPERATING MODE
- Current
- Hall Velocity
- Position
- Velocity
MOTOR TYPE
- Three Phase (Brushless)
- Single Phase (Brushed)
- AC Induction
- Stepper
-
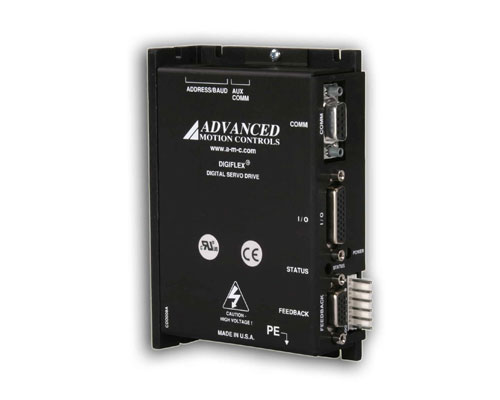
DPRALTR-015B200
-
- Panel Mount:DigiFlex Performance
SPECIFICATIONS
- Current Continuous (A)7.5
- Current Peak (A)15
- DC Supply Voltage (VDC)40 - 190
- Network CommunicationModbus RTU, RS-485/232
- Size (mm)132.5 x 89.5 x 35.9
- Weight (g)486
The DPRALTR-015B200 DigiFlex® Performance™ panel mount servo drive offers full tuning control of all servo loops and is designed for distributed or centralized servo systems. This servo drive utilizes RS485 or Modbus RTU communication and is commissioned with DriveWare® via an RS-232 interface.
CONTROL/COMMAND
- ±10 V Analog
- Step & Direction (5V)
- Encoder Following
- Indexing
- Jogging
- Over the Network
- Sequencing
PRIMARY FEEDBACK
- ±10 VDC Position
- Resolver
- Tachometer (±10 VDC)
OPERATING MODE
- Current
- Position
- Velocity
MOTOR TYPE
- Three Phase (Brushless)
- Single Phase (Brushed)
- AC Induction
- Stepper
-

DPRALTR-015B200
-
- Panel Mount:DigiFlex Performance
SPECIFICATIONS
- Current Continuous (A)7.5
- Current Peak (A)15
- DC Supply Voltage (VDC)40 - 190
- Network CommunicationModbus RTU, RS-485/232
- Size (mm)132.5 x 89.5 x 35.9
- Weight (g)486
The DPRALTR-015B200 DigiFlex® Performance™ panel mount servo drive offers full tuning control of all servo loops and is designed for distributed or centralized servo systems. This servo drive utilizes RS485 or Modbus RTU communication and is commissioned with DriveWare® via an RS-232 interface.
CONTROL/COMMAND
- ±10 V Analog
- Step & Direction (5V)
- Encoder Following
- Indexing
- Jogging
- Over the Network
- Sequencing
PRIMARY FEEDBACK
- ±10 VDC Position
- Resolver
- Tachometer (±10 VDC)
OPERATING MODE
- Current
- Position
- Velocity
MOTOR TYPE
- Three Phase (Brushless)
- Single Phase (Brushed)
- AC Induction Stepper
-

DPRALTR-025B200
-
- Panel Mount:DigiFlex Performance
SPECIFICATIONS
- Current Continuous (A)12.5
- Current Peak (A)25
- DC Supply Voltage (VDC)20 - 190
- Network CommunicationModbus RTU, RS-485/232
- Size (mm)190.5 x 111.8 x 35.9
- Weight (g)872
The DPRALTR-025B200 DigiFlex® Performance™ panel mount servo drive offers full tuning control of all servo loops and is designed for distributed or centralized servo systems. This servo drive utilizes RS485 or Modbus RTU communication and is commissioned with DriveWare® via an RS-232 interface.
CONTROL/COMMAND
- ±10 V Analog
- Step & Direction (5V)
- Encoder Following
- Indexing Jogging
- Over the Network
- Sequencing
PRIMARY FEEDBACK
- ±10 VDC Position
- Resolver
- Tachometer (±10 VDC)
OPERATING MODE
- Current
- Position
- Velocity
MOTOR TYPE
- Three Phase (Brushless)
- Single Phase (Brushed)
- AC Induction
- Stepper
-
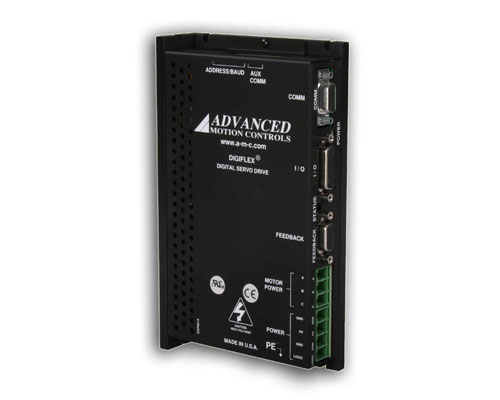
DPRALTR-040B080
-
- Panel Mount:DigiFlex Performance
SPECIFICATIONS
- Current Continuous (A)20
- Current Peak (A)40
- DC Supply Voltage (VDC)20 - 80
- Network CommunicationModbus RTU, RS-485/232
- Size (mm)190.5 x 111.8 x 35.9
- Weight (g)872
The DPRALTR-040B080 DigiFlex® Performance™ panel mount servo drive offers full tuning control of all servo loops and is designed for distributed or centralized servo systems. This servo drive utilizes RS485 or Modbus RTU communication and is commissioned with DriveWare® via an RS-232 interface.
CONTROL/COMMAND
- ±10 V Analog
- Step & Direction (5V)
- Encoder Following
- Indexing
- Jogging
- Over the Network
- Sequencing
PRIMARY FEEDBACK
- ±10 VDC Position
- Resolver
- Tachometer (±10 VDC)
OPERATING MODE
- Current
- Position
- Velocity
MOTOR TYPE
- Three Phase (Brushless)
- Single Phase (Brushed)
- AC Induction
- Stepper
-
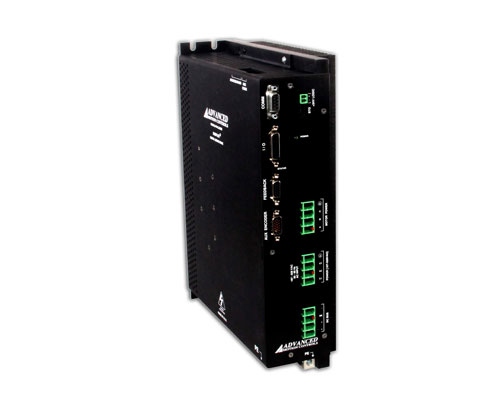
DPRANIE-030A800
-
- Panel Mount:DigiFlex Performance
SPECIFICATIONS
- Current Continuous (A)15
- Current Peak (A)30
- DC Supply Voltage (VDC)255 - 747
- AC Supply Voltage (VAC)200 - 480
- Network CommunicationModbus RTU, RS-485/232
- Functional SafetySafe Torque Off (STO)
- Size (mm)300.5 x 231.3 x 91.4
- Weight (g)5437
The DPRANIE-030A800 DigiFlex® Performance™ panel mount servo drive offers full tuning control of all servo loops and is designed for distributed or centralized servo systems. This servo drive utilizes RS485 or Modbus RTU communication and is commissioned with DriveWare® via an RS-232 interface.
CONTROL/COMMAND
- ±10 V Analog
- Encoder Following
- Indexing
- Jogging
- Over the Network
- PWM and Direction
- Sequencing
PRIMARY FEEDBACK
- ±10 VDC Position
- Halls
- Incremental Encoder
- Tachometer (±10 VDC)
OPERATING MODE
- Current
- Hall Velocity
- Position Velocity
MOTOR TYPE
- Three Phase (Brushless)
- Single Phase (Brushed)
- AC Induction Stepper
-

DPRANIE-060A800
-
- Panel Mount:DigiFlex Performance
SPECIFICATIONS
- Current Continuous (A)30
- Current Peak (A)60
- DC Supply Voltage (VDC)255 - 747
- AC Supply Voltage (VAC)200 - 480
- Network CommunicationModbus RTU, RS-485/232
- Functional SafetySafe Torque Off (STO)
- Size (mm)300.5 x 231.3 x 140.91
- Weight (g)6165
The DPRANIE-060A800 DigiFlex® Performance™ panel mount servo drive offers full tuning control of all servo loops and is designed for distributed or centralized servo systems. This servo drive utilizes RS485 or Modbus RTU communication and is commissioned with DriveWare® via an RS-232 interface.
CONTROL/COMMAND
- ±10 V Analog
- Encoder Following
- Indexing
- Jogging
- Over the Network
- PWM and Direction
- Sequencing
PRIMARY FEEDBACK
- ±10 VDC Position
- Halls
- Incremental Encoder
- Tachometer (±10 VDC)
OPERATING MODE
- Current
- Hall Velocity
- Position Velocity
MOTOR TYPE
- Three Phase (Brushless)
- Single Phase (Brushed)
- AC Induction
- Stepper
-
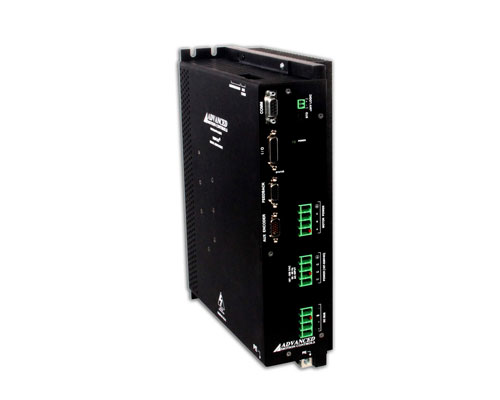
DPRANIR-030A800
-
- Panel Mount:DigiFlex Performance
SPECIFICATIONS
- Current Continuous (A)15
- Current Peak (A)30
- DC Supply Voltage (VDC)255 - 747
- AC Supply Voltage (VAC)200 - 480
- Network CommunicationModbus RTU, RS-485/232
- Functional SafetySafe Torque Off (STO)
- Size (mm)300.5 x 231.3 x 91.4
- Weight (g)5437
The DPRANIR-030A800 DigiFlex® Performance™ panel mount servo drive offers full tuning control of all servo loops and is designed for distributed or centralized servo systems. This servo drive utilizes RS485 or Modbus RTU communication and is commissioned with DriveWare® via an RS-232 interface.
CONTROL/COMMAND
- ±10 V Analog
- Encoder
- Following
- Indexing
- Jogging
- Over the Network
- PWM and Direction
- Sequencing
PRIMARY FEEDBACK
- ±10 VDC Position
- Resolver
- Tachometer (±10 VDC)
OPERATING MODE
- Current
- Position
- Velocity
MOTOR TYPE
- Three Phase (Brushless)
- Single Phase (Brushed)
- AC Induction
- Stepper
-
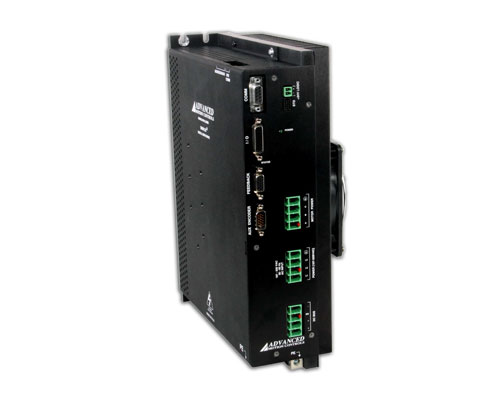
DPRANIR-060A800
-
- Panel Mount:DigiFlex Performance
SPECIFICATIONS
- Current Continuous (A)30
- Current Peak (A)60
- DC Supply Voltage (VDC)255 - 747
- AC Supply Voltage (VAC)200 - 480
- Network CommunicationModbus RTU, RS-485/232
- Functional SafetySafe Torque Off (STO)
- Size (mm)300.5 x 231.3 x 140.91
- Weight (g)6165
The DPRANIR-060A800 DigiFlex® Performance™ panel mount servo drive offers full tuning control of all servo loops and is designed for distributed or centralized servo systems. This servo drive utilizes RS485 or Modbus RTU communication and is commissioned with DriveWare® via an RS-232 interface.
CONTROL/COMMAND
- ±10 V Analog
- Encoder Following
- Indexing
- Jogging
- Over the Network
- PWM and Direction
- Sequencing
PRIMARY FEEDBACK
- ±10 VDC Position
- Resolver
- Tachometer (±10 VDC)
OPERATING MODE
- Current
- Position
- Velocity
MOTOR TYPE
- Three Phase (Brushless)
- Single Phase (Brushed)
- AC Induction Stepper
-

DZCANTE-012L080
-
- PCB Mount:DigiFlex Performance
SPECIFICATIONS
- Current Continuous (A)6
- Current Peak (A)12
- DC Supply Voltage (VDC)20 - 80
- Network CommunicationCANopen
- Size (mm)63.5 x 50.8 x 18.4
- Weight (g)99.8
The DZCANTE-012L080 DigiFlex® Performance™ pcb mount servo drive offers full tuning control of all servo loops and is designed for distributed or centralized servo systems. This servo drive utilizes CANopen® communication and is commissioned with DriveWare® via an RS-232 interface.
CONTROL/COMMAND
- ±10 V Analog
- Encoder Following
- Indexing
- Jogging
- Over the Network
- PWM and Direction
- Sequencing
PRIMARY FEEDBACK
- ±10 VDC Position
- Halls Incremental
- Encoder
- Tachometer (±10 VDC)
OPERATING MODE
- Interpolated Position Mode (PVT)
- Profile Modes
- Cyclic Synchronous Modes
- Current Position
- Velocity
MOTOR TYPE
- Three Phase (Brushless)
- Single Phase (Brushed)
- AC Induction Stepper
-
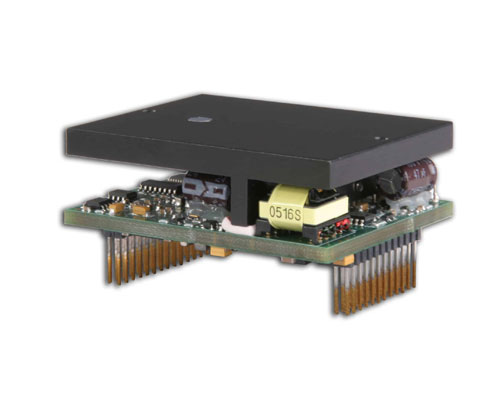
DZCANTE-020L080
-
- PCB Mount:DigiFlex Performance
SPECIFICATIONS
- Current Continuous (A)12
- Current Peak (A)20
- DC Supply Voltage (VDC)10 - 80
- Network CommunicationCANopen
- Size (mm)63.5 x 50.8 x 22.9
- Weight (g)105
The DZCANTE-020L080 DigiFlex® Performance™ pcb mount servo drive offers full tuning control of all servo loops and is designed for distributed or centralized servo systems. This servo drive utilizes CANopen® communication and is commissioned with DriveWare® via an RS-232 interface.
CONTROL/COMMAND
- ±10 V Analog
- Encoder Following
- Indexing
- Jogging
- Over the Network PWM and Direction
- Sequencing
PRIMARY FEEDBACK
- ±10 VDC Position
- Halls
- Incremental Encoder
- Tachometer (±10 VDC)
OPERATING MODE
- Interpolated Position Mode (PVT)
- Profile Modes
- Cyclic Synchronous Modes
- Current
- Position
- Velocity
MOTOR TYPE
- Three Phase (Brushless)
- Single Phase (Brushed)
- AC Induction Stepper
-
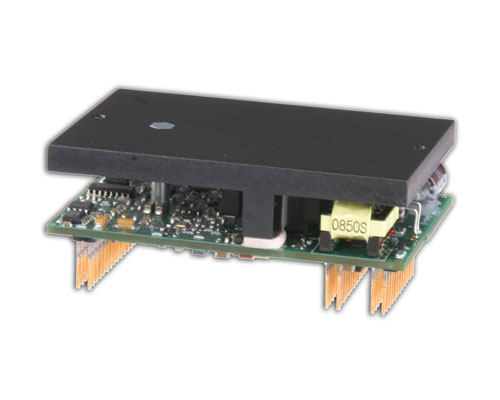
DZCANTE-025L200
-
- PCB Mount:DigiFlex Performance
SPECIFICATIONS
- Current Continuous (A)12.5
- Current Peak (A)25
- DC Supply Voltage (VDC)40 - 175
- Network CommunicationCANopen
- Size (mm)76.2 x 50.8 x 22.9
- Weight (g)123
The DZCANTE-025L200 DigiFlex® Performance™ pcb mount servo drive offers full tuning control of all servo loops and is designed for distributed or centralized servo systems. This servo drive utilizes CANopen® communication and is commissioned with DriveWare® via an RS-232 interface.
CONTROL/COMMAND
- ±10 V Analog
- Encoder Following
- Indexing
- Jogging
- Over the Network PWM and Direction
- Sequencing
PRIMARY FEEDBACK
- ±10 VDC Position
- Halls
- Incremental Encoder
- Tachometer (±10 VDC)
OPERATING MODE
- Interpolated Position Mode (PVT)
- Profile Modes
- Cyclic Synchronous Modes Current Position Velocity
MOTOR TYPE
- Three Phase (Brushless)
- Single Phase (Brushed)
- AC Induction
- Stepper
-
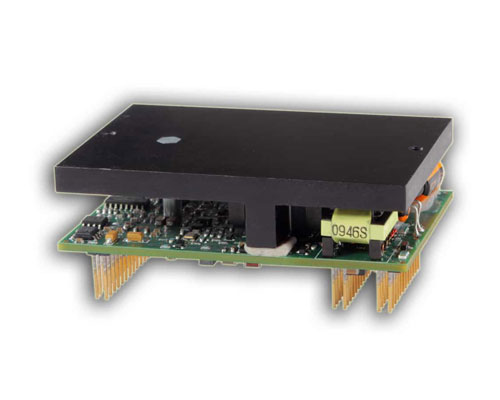
DZCANTE-060L080
-
- PCB Mount:DigiFlex Performance
SPECIFICATIONS
- Current Continuous (A)30
- Current Peak (A)60
- DC Supply Voltage (VDC)10 - 80
- Network CommunicationCANopen
- Size (mm)76.2 x 50.8 x 22.9
- Weight (g)123
The DZCANTE-060L080 DigiFlex® Performance™ pcb mount servo drive offers full tuning control of all servo loops and is designed for distributed or centralized servo systems. This servo drive utilizes CANopen® communication and is commissioned with DriveWare® via an RS-232 interface.
CONTROL/COMMAND
- ±10 V Analog
- Encoder Following
- Indexing
- Jogging
- Over the Network
- PWM and Direction
- Sequencing
PRIMARY FEEDBACK
- ±10 VDC Position
- Halls
- Incremental Encoder
- Tachometer (±10 VDC)
OPERATING MODE
- Interpolated Position Mode (PVT)
- Profile Modes
- Cyclic Synchronous Modes
- Current
- Position
- Velocity
MOTOR TYPE
- Three Phase (Brushless)
- Single Phase (Brushed)
- AC Induction
- Stepper
-
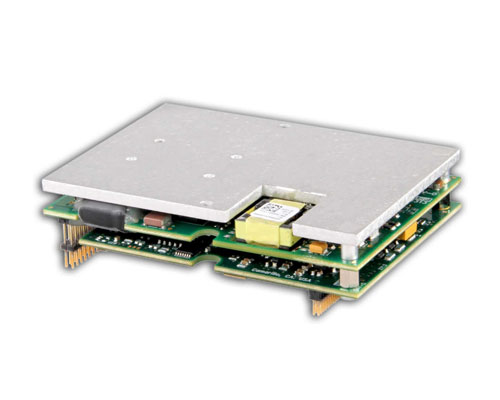
DZEANTU-020B080
-
- PCB Mount:DigiFlex Performance
SPECIFICATIONS
- Current Continuous (A)10
- Current Peak (A)20
- DC Supply Voltage (VDC)18 - 80
- Network CommunicationEtherCAT, DxM Technology
- Functional SafetySafe Torque Off (STO)
- Size (mm)88.9 x 63.5 x 20.1
- Weight (g)126
The DZEANTU-020B080 DigiFlex® Performance™ pcb mount servo drive offers full tuning control of all servo loops and is designed for distributed or centralized servo systems. This servo drive utilizes EtherCAT® communication and is commissioned with DriveWare® via a USB interface.
CONTROL/COMMAND
- ±10 V Analog
- Encoder Following
- Indexing
- Jogging
- Over the Network
- Sequencing
PRIMARY FEEDBACK
- ±10 VDC Position
- 1Vp-p Sine/Cosine Encoder
- BiSS C-Mode
- EnDat® 2.1
- EnDat® 2.2 Halls
- Hiperface®
- Incremental Encoder
- Tachometer (±10 VDC)
OPERATING MODE
- Profile Modes
- Cyclic Synchronous Modes
- Current
- Position
- Velocity
MOTOR TYPE
- Three Phase (Brushless)
- Single Phase (Brushed)
- AC Induction Stepper
-
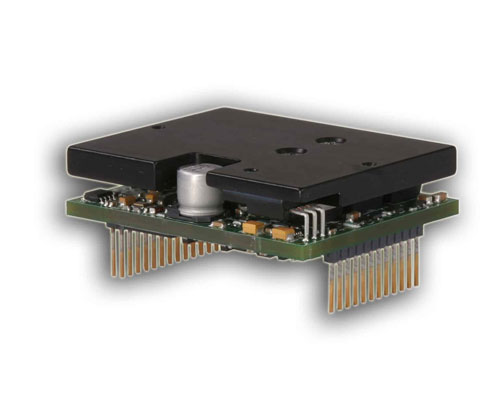
DZRALTE-012L080
-
- PCB Mount:DigiFlex Performance
SPECIFICATIONS
- Current Continuous (A)6
- Current Peak (A)12
- DC Supply Voltage (VDC)20 - 80
- Network CommunicationModbus RTU, RS-485/232
- Size (mm)63.5 x 50.8 x 18.4
- Weight (g)99.8
The DZRALTE-012L080 DigiFlex® Performance™ pcb mount servo drive offers full tuning control of all servo loops and is designed for distributed or centralized servo systems. This servo driver utilizes RS485 or Modbus RTU communication and is commissioned with DriveWare® via an RS-232 interface.
CONTROL/COMMAND
- ±10 V Analog
- Step & Direction (5V)
- Encoder Following
- Indexing
- Jogging
- Over the Network
- PWM and Direction
- Sequencing
PRIMARY FEEDBACK
- ±10 VDC Position
- Halls
- Incremental Encoder
- Tachometer (±10 VDC)
OPERATING MODE
- Current
- Hall Velocity
- Position
- Velocity
MOTOR TYPE
- Three Phase (Brushless)
- Single Phase (Brushed)
- AC Induction
- Stepper
-

DZRALTE-020L080
-
- PCB Mount.DigiFlex Performance
SPECIFICATIONS
- Current Continuous (A)12
- Current Peak (A)20
- DC Supply Voltage (VDC)10 - 80
- Network CommunicationModbus RTU, RS-485/232
- Size (mm)63.5 x 50.8 x 22.9
- Weight (g)105
The DZRALTE-020L080 DigiFlex® Performance™ pcb mount servo drive offers full tuning control of all servo loops and is designed for distributed or centralized servo systems. This servo driver utilizes RS485 or Modbus RTU communication and is commissioned with DriveWare® via an RS-232 interface.
CONTROL/COMMAND
- ±10 V Analog
- Step & Direction (5V)
- Encoder Following
- Indexing
- Jogging
- Over the Network
- PWM and Direction
- Sequencing
PRIMARY FEEDBACK
- ±10 VDC Position
- Halls
- Incremental
- Encoder
- Tachometer (±10 VDC)
OPERATING MODE
- Current
- Hall Velocity
- Position
- Velocity
MOTOR TYPE
- Three Phase (Brushless)
- Single Phase (Brushed)
- AC Induction
- Stepper
-
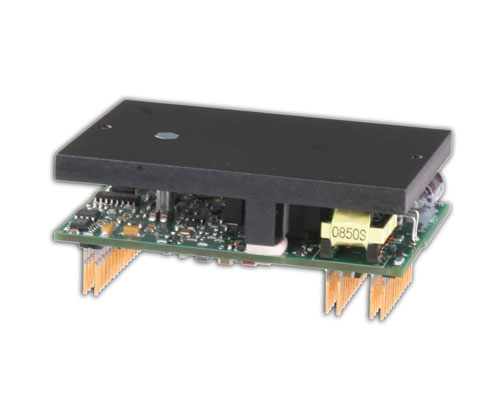
DZRALTE-025L200
-
- PCB Mount:DigiFlex Performance
SPECIFICATIONS
- Current Continuous (A)12.5
- Current Peak (A)25
- DC Supply Voltage (VDC)40 - 175
- Network CommunicationModbus RTU, RS-485/232
- Size (mm)76.2 x 50.8 x 22.9
- Weight (g)123
The DZRALTE-025L200 DigiFlex® Performance™ pcb mount servo drive offers full tuning control of all servo loops and is designed for distributed or centralized servo systems. This servo driver utilizes RS485 or Modbus RTU communication and is commissioned with DriveWare® via an RS-232 interface.
CONTROL/COMMAND
- ±10 V Analog
- Step & Direction (5V)
- Encoder Following
- Indexing
- Jogging
- Over the Network PWM and Direction
- Sequencing
PRIMARY FEEDBACK
- ±10 VDC Position
- Halls
- Incremental Encoder
- Tachometer (±10 VDC)
OPERATING MODE
- Current
- Hall Velocity
- Position
- Velocity
MOTOR TYPE
- Three Phase (Brushless)
- Single Phase (Brushed)
- AC Induction Stepper
-
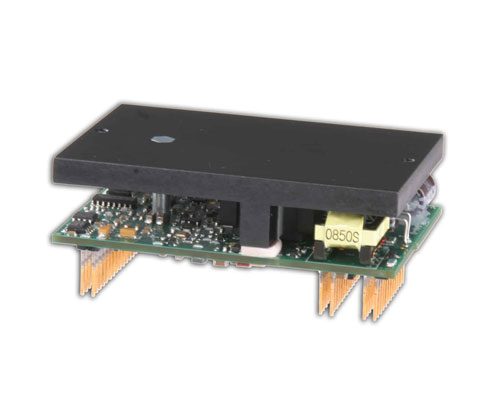
DZRALTE-040L080
-
- PCB Mount:DigiFlex Performance
SPECIFICATIONS
- Current Continuous (A)20
- Current Peak (A)40
- DC Supply Voltage (VDC)10 - 80
- Network CommunicationModbus RTU, RS-485/232
- Size (mm)76.2 x 50.8 x 22.9
- Weight (g)123
The DZRALTE-040L080 DigiFlex® Performance™ pcb mount servo drive offers full tuning control of all servo loops and is designed for distributed or centralized servo systems. This servo driver utilizes RS485 or Modbus RTU communication and is commissioned with DriveWare® via an RS-232 interface.
CONTROL/COMMAND
- ±10 V Analog
- Step & Direction (5V)
- Encoder Following
- Indexing
- Jogging
- Over the Network
- PWM and Direction
- Sequencing
PRIMARY FEEDBACK
- ±10 VDC Position
- Halls
- Incremental Encoder
- Tachometer (±10 VDC)
OPERATING MODE
- Current
- Hall
- Velocity
- Position
- Velocity
MOTOR TYPE
- Three Phase (Brushless)
- Single Phase (Brushed)
- AC Induction
- Stepper
-
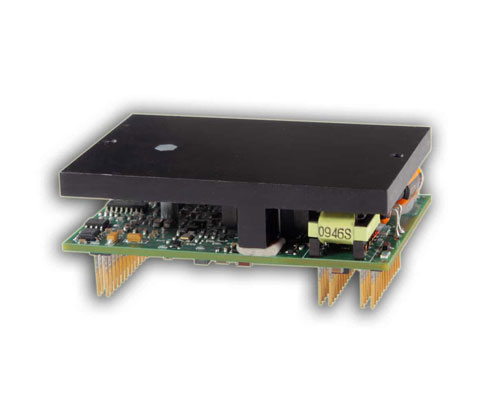
DZRALTE-060L080
-
- PCB Mount:DigiFlex Performance
SPECIFICATIONS
- Current Continuous (A)30
- Current Peak (A)60
- DC Supply Voltage (VDC)10 - 80
- Network CommunicationModbus RTU, RS-485/232
- Size (mm)76.2 x 50.8 x 22.9
- Weight (g)123
The DZRALTE-060L080 DigiFlex® Performance™ pcb mount servo drive offers full tuning control of all servo loops and is designed for distributed or centralized servo systems. This servo driver utilizes RS485 or Modbus RTU communication and is commissioned with DriveWare® via an RS-232 interface.
CONTROL/COMMAND
- ±10 V Analog
- Step & Direction (5V)
- Encoder Following
- Indexing
- Jogging
- Over the Network
- PWM and Direction
- Sequencing
PRIMARY FEEDBACK
- ±10 VDC Position
- Halls Incremental Encoder
- Tachometer (±10 VDC)
OPERATING MODE
- Current
- Hall Velocity
- Position
- Velocity
MOTOR TYPE
- Three Phase (Brushless)
- Single Phase (Brushed)
- AC Induction
- Stepper
-
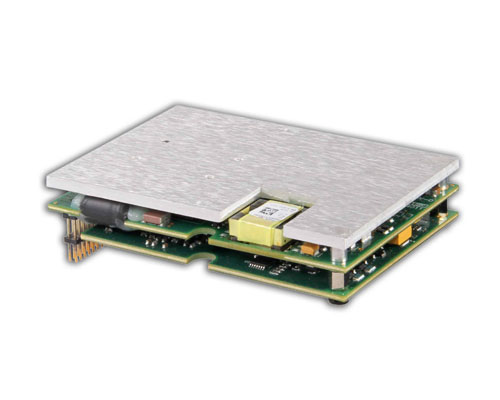
DZSANTU-020B080
-
- PCB Mount:DigiFlex Performance
SPECIFICATIONS
- Current Continuous (A)10
- Current Peak (A)20
- DC Supply Voltage (VDC)18 - 80
- Network CommunicationDxM Technology
- Functional SafetySafe Torque Off (STO)
- Size (mm)88.9 x 63.5 x 20.1
- Weight (g)124
The DZSANTU-020B080 DigiFlex® Performance™ pcb mount servo drive offers full tuning control of all servo loops and is designed for distributed or centralized servo systems. DZSANTU servo drives are designed for use as sub-nodes on an EtherCAT® network and must be used in conjunction with a DZEANTU node. This drive utilizes DxM™ Technology and is commissioned with DriveWare® via a USB interface.
CONTROL/COMMAND
PRIMARY FEEDBACK
- ±10 VDC Position
- 1Vp-p Sine/Cosine Encoder
- BiSS C-Mode
- EnDat® 2.1
- EnDat® 2.2
- Halls
- Hiperface®
- Incremental Encoder
- Tachometer (±10 VDC)
OPERATING MODE
- Profile Modes
- Cyclic Synchronous Modes
MOTOR TYPE
- Three Phase (Brushless)
- Single Phase (Brushed)
- AC Induction
- Stepper
-

DZXCANTE-008L080
-
- PCB Mount:DigiFlex Performance
SPECIFICATIONS
- Current Continuous (A)4
- Current Peak (A)8
- DC Supply Voltage (VDC)10 - 80
- Network CommunicationCANopen
- Size (mm)63.5 x 50.8 x 22.9
- Weight (g)105
The DZXCANTE-008L080 DigiFlex® Performance™ extended environment pcb mount servo drive offers full tuning control of all servo loops and is designed for distributed or centralized servo systems in harsh temperatures or rugged environments. This servo motor drive utilizes CANopen® communication and is commissioned with DriveWare® via an RS-232 interface.
CONTROL/COMMAND
- ±10 V Analog
- Encoder Following
- Indexing
- Jogging
- Over the Network
- PWM and Direction
- Sequencing
PRIMARY FEEDBACK
- ±10 VDC Position
- Halls
- Incremental Encoder
- Tachometer (±10 VDC)
OPERATING MODE
- Interpolated Position Mode (PVT)
- Profile Modes
- Cyclic Synchronous Modes
- Current
- Position
- Velocity
MOTOR TYPE
- Three Phase (Brushless)
- Single Phase (Brushed)
- AC Induction
- Stepper
-
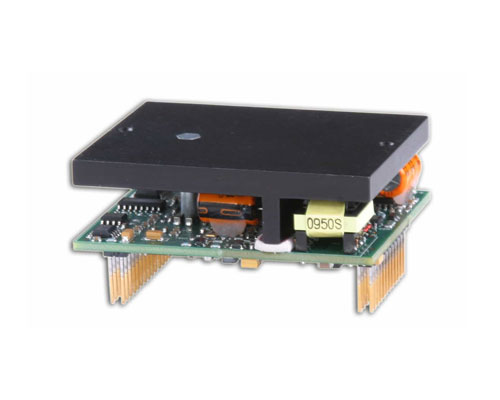
DZXCANTE-015L080
-
- PCB Mount:DigiFlex Performance
SPECIFICATIONS
- Current Continuous (A)7.5
- Current Peak (A)15
- DC Supply Voltage (VDC)10 - 80
- Network CommunicationCANopen
- Size (mm)63.5 x 50.8 x 22.9
- Weight (g)105
The DZXCANTE-015L080 DigiFlex® Performance™ extended environment pcb mount servo drive offers full tuning control of all servo loops and is designed for distributed or centralized servo systems in harsh temperatures or rugged environments. This servo motor drive utilizes CANopen® communication and is commissioned with DriveWare® via an RS-232 interface.
CONTROL/COMMAND
- ±10 V Analog
- Encoder Following
- Indexing
- Jogging
- Over the Network
- PWM and Direction
- Sequencing
PRIMARY FEEDBACK
- ±10 VDC Position
- Halls
- Incremental Encoder
- Tachometer (±10 VDC)
OPERATING MODE
- Interpolated Position Mode (PVT)
- Profile Modes
- Cyclic Synchronous Modes
- Current Position
- Velocity
MOTOR TYPE
- Three Phase (Brushless)
- Single Phase (Brushed)
- AC Induction
- Stepper
-
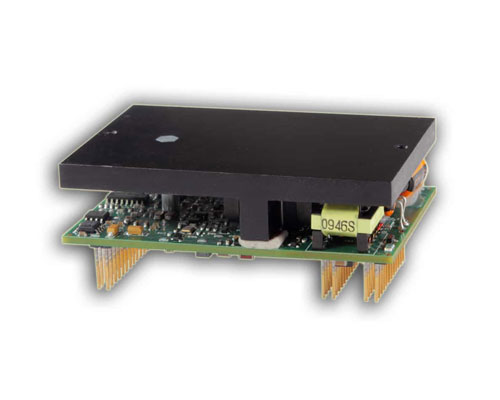
DZXCANTE-040L080
-
- PCB Mount:DigiFlex Performance
SPECIFICATIONS
- Current Continuous (A)20
- Current Peak (A)40
- DC Supply Voltage (VDC)10 - 80
- Network CommunicationCANopen
- Size (mm)76.2 x 50.8 x 22.9
- Weight (g)123
The DZXCANTE-040L080 DigiFlex® Performance™ extended environment pcb mount servo drive offers full tuning control of all servo loops and is designed for distributed or centralized servo systems in harsh temperatures or rugged environments. This servo motor drive utilizes CANopen® communication and is commissioned with DriveWare® via an RS-232 interface.
CONTROL/COMMAND
- ±10 V Analog
- Encoder Following
- Indexing
- Jogging
- Over the Network
- PWM and Direction
- Sequencing
PRIMARY FEEDBACK
- ±10 VDC Position
- Halls Incremental
- Encoder
- Tachometer (±10 VDC)
OPERATING MODE
- Interpolated Position Mode (PVT)
- Profile Modes
- Cyclic Synchronous Modes
- Current
- Position
- Velocity
MOTOR TYPE
- Three Phase (Brushless)
- Single Phase (Brushed)
- AC Induction
- Stepper
-
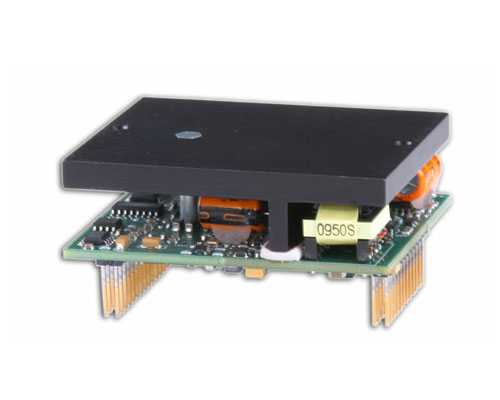
DZXRALTE-008L080
-
- PCB Mount:DigiFlex Performance
SPECIFICATIONS
- Current Continuous (A)4
- Current Peak (A)8
- DC Supply Voltage (VDC)10 - 80
- Network CommunicationModbus RTU, RS-485/232
- Size (mm)63.5 x 50.8 x 22.9
- Weight (g)105
The DZXRALTE-008L080 DigiFlex® Performance™ extended environment pcb mount servo drive offers full tuning control of all servo loops and is designed for distributed or centralized servo systems in harsh temperatures or rugged environments. This servo motor drive utilizes RS485 or Modbus RTU communication and is commissioned with DriveWare® via an RS-232 interface.
CONTROL/COMMAND
- ±10 V Analog
- Step & Direction (5V)
- Encoder Following
- Indexing
- Jogging
- Over the Network
- PWM and Direction
- Sequencing
PRIMARY FEEDBACK
- ±10 VDC Position
- Halls
- Incremental Encoder
- Tachometer (±10 VDC)
OPERATING MODE
- Current
- Hall Velocity
- Position
- Velocity
MOTOR TYPE
- Three Phase (Brushless)
- Single Phase (Brushed)
- AC Induction
- Stepper
-

DZXRALTE-015L080
-
- PCB Mount:DigiFlex Performance
SPECIFICATIONS
- Current Continuous (A)7.5
- Current Peak (A)15
- DC Supply Voltage (VDC)10 - 80
- Network CommunicationModbus RTU, RS-485/232
- Size (mm)63.5 x 50.8 x 22.9 Weight (g)105
The DZXRALTE-015L080 DigiFlex® Performance™ extended environment pcb mount servo drive offers full tuning control of all servo loops and is designed for distributed or centralized servo systems in harsh temperatures or rugged environments. This servo motor drive utilizes RS485 or Modbus RTU communication and is commissioned with DriveWare® via an RS-232 interface.
CONTROL/COMMAND
- ±10 V Analog
- Step & Direction (5V)
- Encoder Following
- Indexing
- Jogging
- Over the Network
- PWM and Direction
- Sequencing
PRIMARY FEEDBACK
- ±10 VDC Position
- Halls
- Incremental Encoder
- Tachometer (±10 VDC)
OPERATING MODE
- Current
- Hall Velocity
- Position
- Velocity
MOTOR TYPE
- Three Phase (Brushless)
- Single Phase (Brushed)
- AC Induction
- Stepper
-
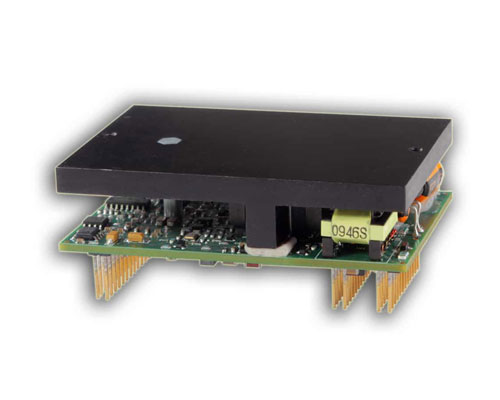
DZXRALTE-040L080
-
- PCB Mount:DigiFlex Performance
SPECIFICATIONS
- Current Continuous (A)20
- Current Peak (A)40
- DC Supply Voltage (VDC)10 - 80
- Network CommunicationModbus RTU, RS-485/232
- Size (mm)76.2 x 50.8 x 22.9
- Weight (g)123
The DZXRALTE-040L080 DigiFlex® Performance™ extended environment pcb mount servo drive offers full tuning control of all servo loops and is designed for distributed or centralized servo systems in harsh temperatures or rugged environments. This servo motor drive utilizes RS485 or Modbus RTU communication and is commissioned with DriveWare® via an RS-232 interface.
CONTROL/COMMAND
- ±10 V Analog
- Step & Direction (5V)
- Encoder Following
- Indexing
- Jogging
- Over the Network
- PWM and Direction
- Sequencing
PRIMARY FEEDBACK
- ±10 VDC Position
- Halls
- Incremental Encoder
- Tachometer (±10 VDC)
OPERATING MODE
- Current
- Hall Velocity
- Position Velocity
MOTOR TYPE
- Three Phase (Brushless)
- Single Phase (Brushed)
- AC Induction
- Stepper
Motion Control
Performance
At ADVANCED Motion Controls our goal is to make servo drives that are compatible with as many controllers as possible. These include EtherCAT, CANopen, Powerlink, and more! This gives you and other system designers the freedom to choose among a wider variety of controllers and not get locked into any particular manufacturer.
Click&Move Automated Software Solution

- Click&Move® (C&M) is an automation solution designed for OEMs and systems integrators. It can include motion control, PLC logic, local I/O, and networked I/O. Applications can be simple, single-axis with minimal I/O to complex, multi-axes running in real time.
A Click&Move system will consist of both a software component used to create the logic, HMI, and motion profiles and hardware components such as a controller, servo drives, and I/O devices.
-
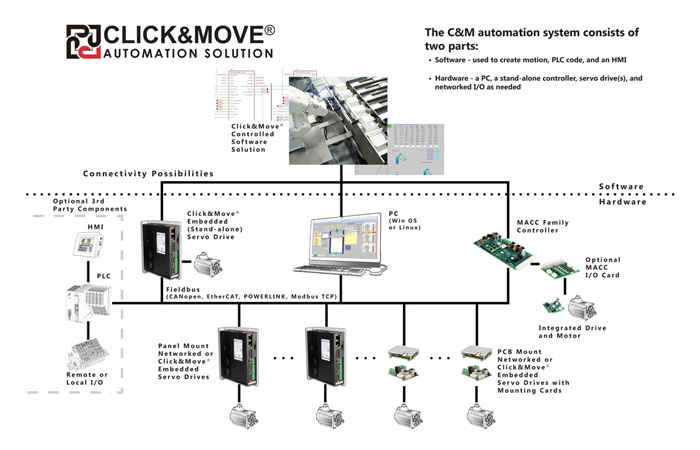
Click&Move Quick Facts
-
-
- Combines Motion, PLC, and HMI control
- Based on PLCopen, the global standard for industrial control programming
- Supports CANopen, EtherCAT, and POWERLINK network protocols
- Fully IEC 61131-3 compliant using graphical Function Block Diagrams (FBDs) (pre-configured or user-defined)
- Multiple platforms supported: PC (Win OS and Linux), stand-alone controller (MACC), and ADVANCED Motion Controls’ drives
-

Integrated Design Environment
-
- The C&M Integrated Development Environment (IDE) provides the user with a programming environment for a range of applications:
- Motion control
- PLC machine control
- G-code file handling for CNC apps
- Process control
- Robotics
The IDE consists of applications to graphically create/edit Function Block Diagram (FBD) based logic schematics and HMI screens, debug application code, organize and archive application code, merge and compare code as well as automating the build/compile status.
Where do we start?
HMI Requirements: The HMI represents the User Interface Controls. This is what the user will use to interact with the system once it's live.
FBD Requirements: The FBD (Function Block Diagram) represents the motion and logic behavior.
Depending on their project or their work style, users may want to start with either end. It's ultimately up to them!
-

HMI
-
- Click&Move® collects several aspects of motion control, real-time computation, and human interface into a single application. HMIs built in Click&Move are completely customizable. An HMI screen can be as simple as a start/stop button with a drive status read-out.
Alternatively, it can be a full operational control screen where users can input commands, enable and disable individual servo drives, display system information, adjust parameters, and even display a dynamic graphical representation of the motion system that updates in real time. As long as the values can be pulled from the function block diagram, the HMI can display any data the user chooses.
The editor comes with built in templates for buttons, fields and other elements, so its easy for users to get started. Users can even embed images and change colors and sizes of elements to make their HMI look exactly how they want.
- The Function Block Diagram (Eagle) handles the motion, PLC functions, and I/O behavior
- A real-time shell handles communication from the compiled motion program to the fieldbus and HMI (EtherCAT Master stack is embedded in the shell)
- Virtual axis or real axes are selected based on an XML file configuration in the project
- The HMI displays live information and alters variables during real-time operation
-
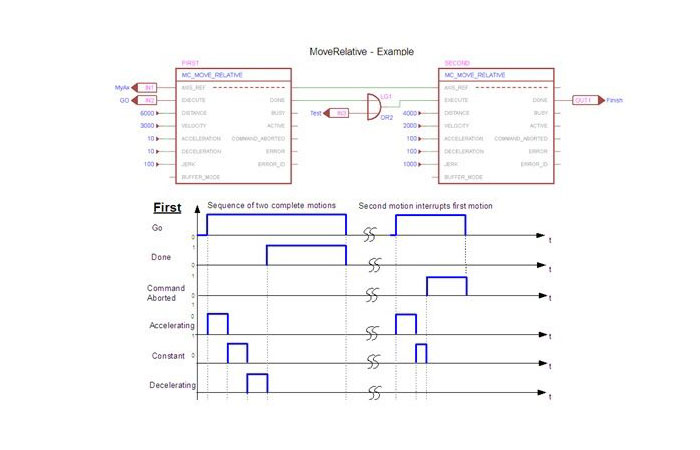
MC Blocks and G-Code
-
-
- Efforts toward keeping within the evolving motion control standards allows for a built-in knowledge base
- This layer of abstraction relieves some of the programming design issues
- PLCopen manuals are distributed within C&M
- Coordinated motion feature follows PLCopen standards
- G-Code handling
-
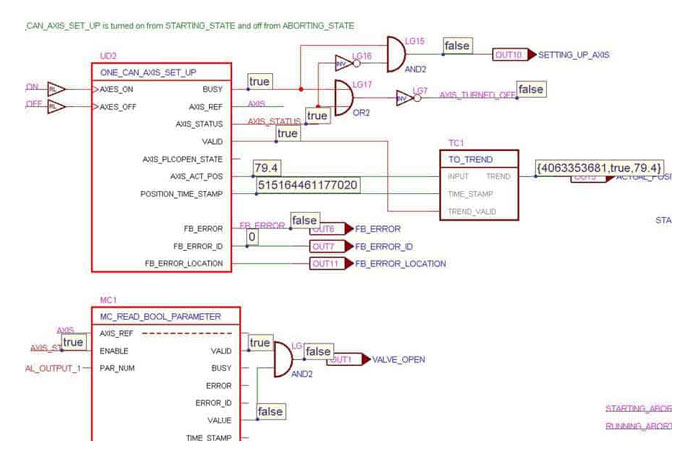
Debugging
-
-
- Application programming using PLCopen FBD language (IEC 61131-3)
- The development process can take place entirely within the user´s PC
- Virtual axes for motion simulation
- Virtual axis projects can be packaged and exchanged with tech support
- Entirely digital development system helps the support process virtual axes are more portable than real ones
- 调试工具:图形和文本
- Integrated HMI
- Extensive built-in Help - Tutorials, Demos, White Papers, etc.
- Extensive example applications
-
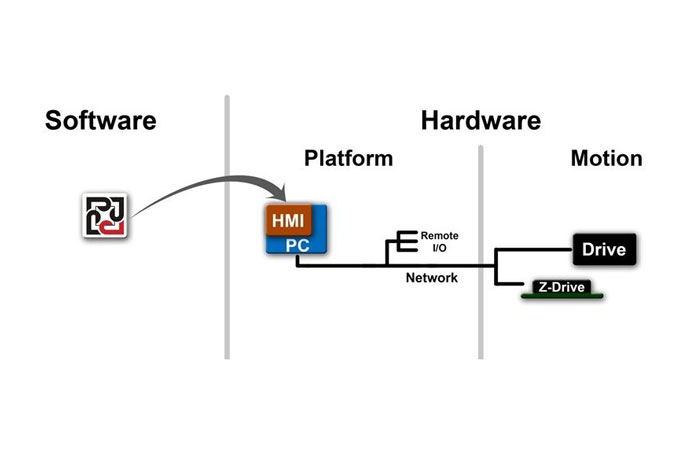
Solution Architectures
-
- 一个Click&Move thousa®系统可以放在一起nds of ways, but most architectures follow one of three main structures. The preferred method depends on the application.
PC-Based
In the PC-based solution below, the C&M development software is used to create motion code, PLC logic, and user interface screens (HMI). The code is compiled for the targeted PC platform and then downloaded. Servo drives and I/O are connected to the PC platform via the network.
The PC-based architecture is obviously best-suited for applications where having a PC connected to the system during operation is feasible, such as industrial machines, gantries, and other devices that remain largely stationary. It's also the preferred architecture for any system that has more than 8 motion axes.
-
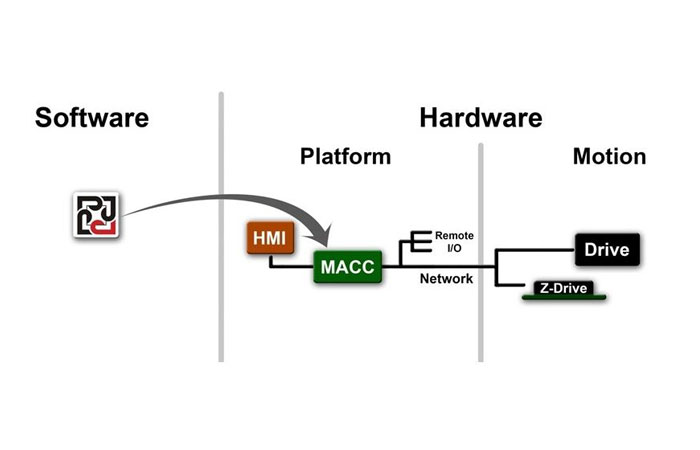
Motion Automation Control Card
-
- The Motion Automation Control Card (MACC) is a general purpose motion/automation controller with embedded Click&Move® capability. In this scenario, the code is compiled for the MACC platform and then downloaded. The servo drives and I/O are connected to the MACC platform via the network. Optionally, a separate HMI screen can be incorporated via the HDMI connector onboard.
The MACC solution is great for mobile applications such as AGV's, but also can be a more cost-effective alternative to the PC-based architecture for applications with 8 axes or fewer. The MACCs also are best suited for applications with a combination of both digital and analog servo drives.
-
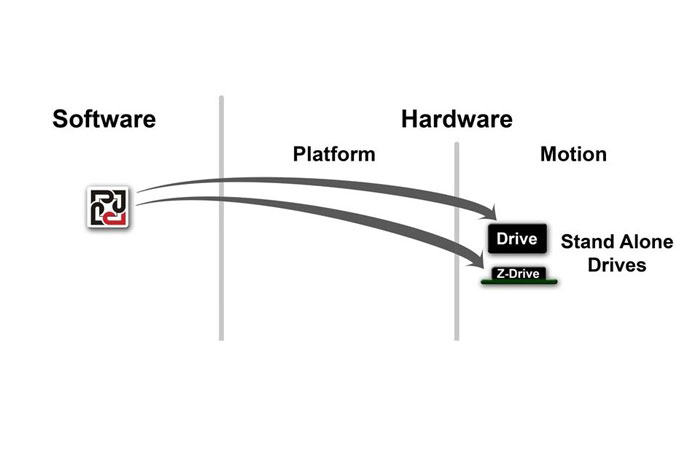
Servo Drive-Embedded
-
- ADVANCED Motion Controls offers digital drives that are designed to store and run an embedded C&M program. The C&M development software is used to create motion code and PLC logic. The code is compiled for the targeted drive platform and then downloaded. I/O is local to the drive(s).
The servo drive takes over the computational work that would otherwise be left to a PC or stand alone controller, saving both space and money.
This is a simple, powerful solution for small applications. It is, however, best used primarily for single-axis applications.
Power Supplies
-
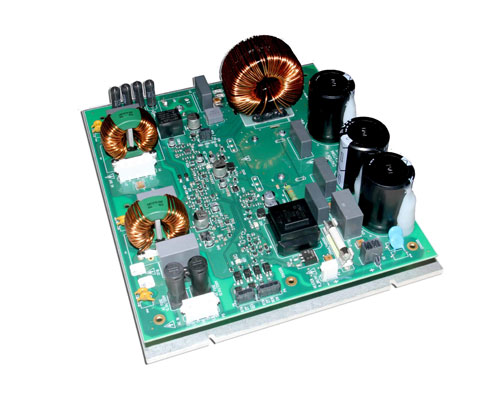
PFC2400W375
-
- SPECIFICATIONS
- Output Voltage (DC)375
- Current Continuous (A)6.4
- Rated Power Continuous (kw)2.4
- AC Supply Voltage (VAC)120, 240
- AC Input Phases1
- Additional FeaturesPower Factor Correction,Regulated,Built-in Shunt Regulator
The PFC2400W375 is a regulated DC power supply with power factor correction designed to feed 400V series servo drives with a low noise 375 VDC bus.
-
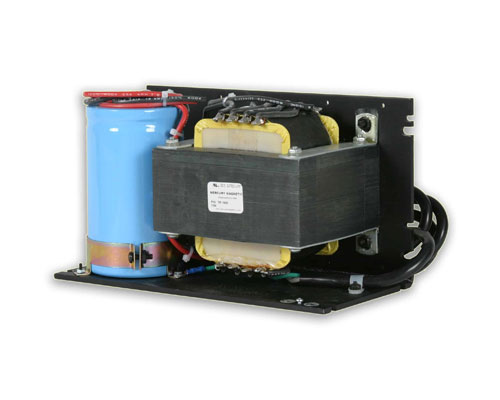
PS16H120-L
-
- SPECIFICATIONS
- Output Voltage (DC)120
- Current Continuous (A)7
- Rated Power Continuous (kw)0.8
- AC Input Phases1
- Additional FeaturesIsolation
的PS16H120-L is an unregulated power supply with an isolation transformer.
-
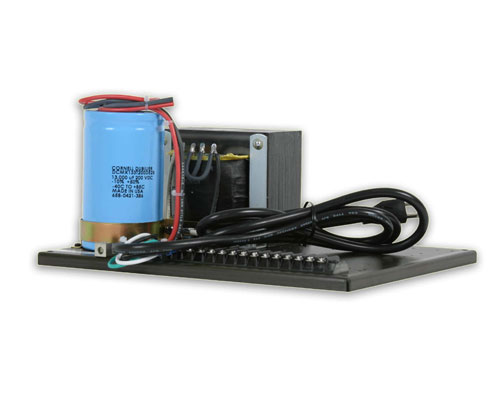
PS16H160
-
- SPECIFICATIONS
- Output Voltage (DC)160 Current Continuous (A) 5
- Rated Power Continuous (kw)0.8
- AC Input Phases1
- Additional FeaturesIsolation
的PS16H160 is an unregulated power supply with an isolation transformer.
-

PS16H30-L
-
- SPECIFICATIONS
- Output Voltage (DC)30
- Current Continuous (A)27
- Rated Power Continuous (kw)0.8
- AC Input Phases1
- Additional FeaturesIsolation
的PS16H30-L is an unregulated power supply with an isolation transformer.
-

PS16L120-L
-
- SPECIFICATIONS
- Output Voltage (DC)120
- Current Continuous (A)7
- Rated Power Continuous (kw)0.8
- AC Input Phases1
- Additional FeaturesIsolation
的PS16L120-L is an unregulated power supply with an isolation transformer.
-
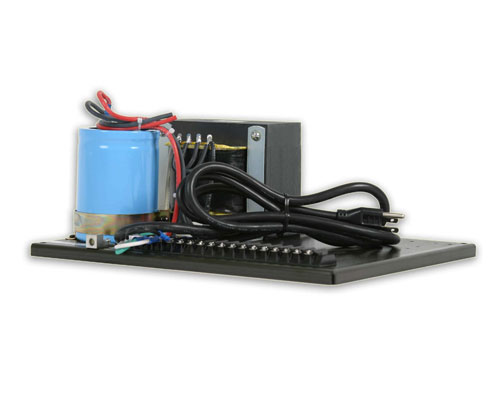
PS16L60
-
- SPECIFICATIONS
- Output Voltage (DC)60
- Current Continuous (A)13
- Rated Power Continuous (kw)0.8
- AC Input Phases1
- Additional FeaturesIsolation
的PS16L60 is an unregulated power supply with an isolation transformer.
-

PS300H24
-
- SPECIFICATIONS
- Output Voltage (DC)24
- Current Continuous (A)12
- Rated Power Continuous (kw)0.3
- AC Input Phases1
- Additional FeaturesIsolation
The PS300H24 is an unregulated power supply with an isolation transformer.
-
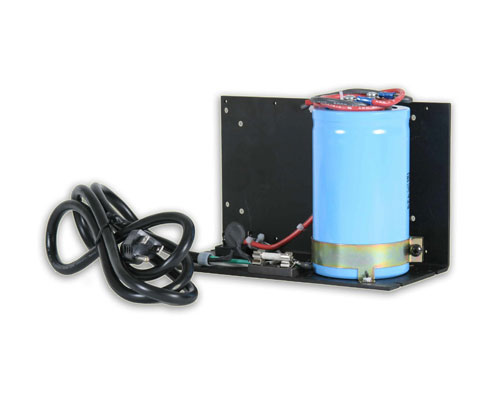
PS300W170
-
- SPECIFICATIONS
- Output Voltage (DC)170
- Current Continuous (A)15
- Rated Power Continuous (kw)2.55 AC
- Input Phases1
The PS300W170 is a non-isolated unregulated power supply.
-

PS30A
-
- SPECIFICATIONS
- Output Voltage (DC)340
- Current Continuous (A)15
- Rated Power Continuous (kw)10.1
- AC Input Phases3
- Additional FeaturesBuilt-in Shunt Regulator,Built-in Shunt Resistor
The PS30A is a non-isolated unregulated power supply.
Other Accessories
-
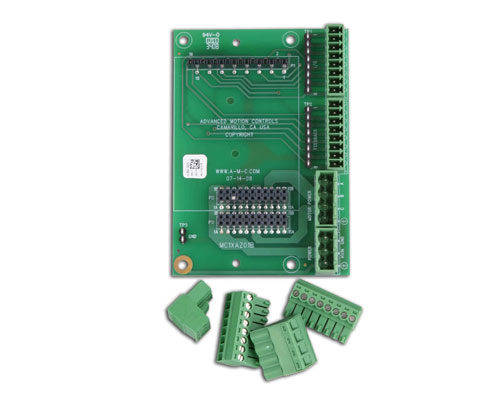
Mounting Card MC1XAZ01
-
- Family:AxCent
- Size (mm)101.6 x 71.9 x 15.7
- Weight (g)58.3
- Current Peak (A)25
The MC1XAZ01 mounting card is designed to hold an AxCent™ family pcb mount servo drive to simplify connection to the controller, motor, and feedback.
-
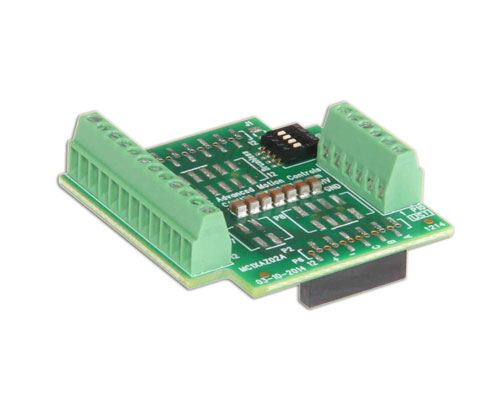
Mounting Card MC1XAZ02
-
- Family:AxCent
- Size (mm)38.1 x 38.1 x 16.2
- Weight (g)11.3
- Current Peak (A)10
The MC1XAZ02 mounting card is designed to hold a micro-size AxCent™ family pcb mount servo drive to simplify connection to the controller, motor, and feedback.
-

Mounting Card MC1XDZC03-QD
-
- Family:DigiFlex Performance
- Size (mm)63.5 x 76.2 x 25.4
- Weight (g)50.7
- Network CommunicationCANopen
- Current Peak (A)25
The MC1XDZC03-QD mounting card is designed to hold a DZCANTE or DZXCANTE DigiFlex® Performance™ family pcb mount servo drive to simplify connection to the controller, motor, and feedback. The motor and power connectors utilize quick-disconnect style connections.
-
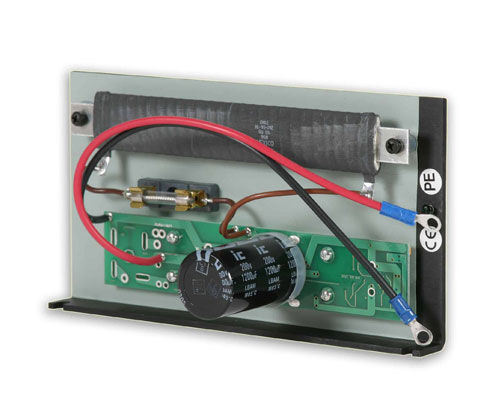
Shunt Regulator SRST175
-
- SPECIFICATIONS
- Clamping Voltage175
- Rated Dissipation Capability (W)95
- Size (mm)203.2 x 108.0 x 66.70
- Weight (g)385
The SRST175 shunt regulator clamps the supply voltage to 175 VDC during regeneration or voltage fluctuations.
-
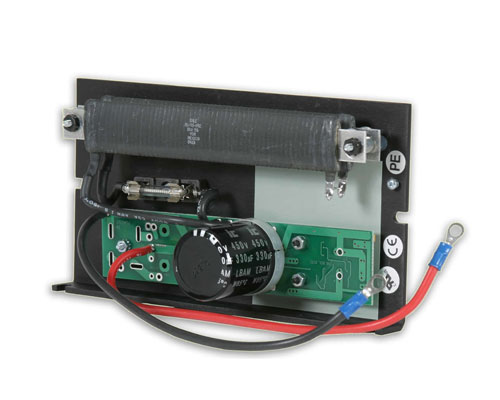
Shunt Regulator SRST380
-
- SPECIFICATIONS
- Clamping Voltage380
- Rated Dissipation Capability (W)190Size (mm)203.2 x 108.0 x 66.70
- Weight (g)385
The SRST380 shunt regulator clamps the supply voltage to 380 VDC during regeneration or voltage fluctuations.
-
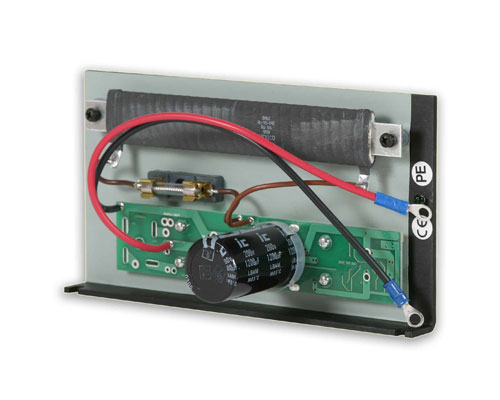
Shunt Regulator SRST50
-
- SPECIFICATIONS
- Clamping Voltage50
- Rated Dissipation Capability (W)95
- Size (mm)203.2 x 108.0 x 66.70
- Weight (g)385
The SRST50 shunt regulator clamps the supply voltage to 50 VDC during regeneration or voltage fluctuations.
-
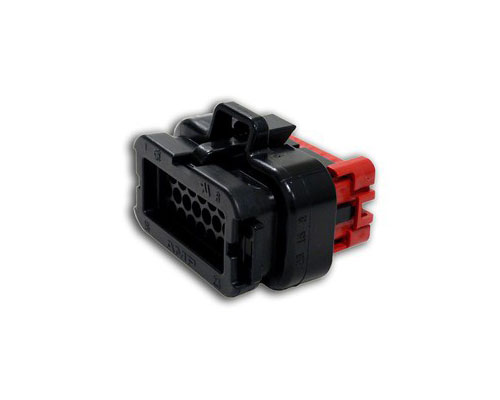
Connector Kit KC-23AMPSEAL01
-
- Family:AxCent
KC-23AMPSEAL01交配连接器套件提供了connector housing, socket contacts and seal plugs. Refer to the mating connector kit datasheet for compatible servo drives.
-

Connector Kit KC-MC1XDZ02
-
- Family:DigiFlex Performance
The KC-MC1XDZ02 mating connector kit provides mating connector housing and crimp pins. Refer to the mating connector kit datasheet for compatible mounting cards.
-
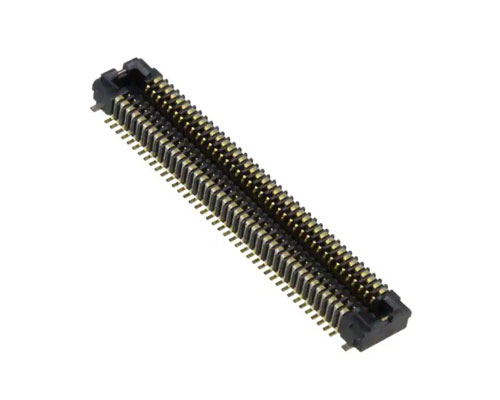
Connector Kit KC-MC1XFE01
-
- Family:FlexPro
The KC-MC1XFE01 mating connector kit provides a surface mount board connector and board spacers. Refer to the mating connector kit datasheet for compatible servo drive models.
-
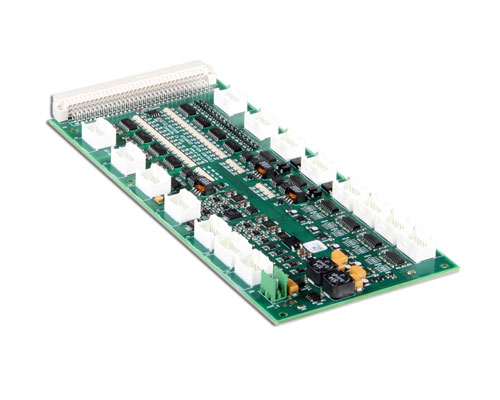
MACC I/O Board MACCIO1
-
- SPECIFICATIONS
- Size (mm)219.96 x 99.95 x 13.60
- Weight (g)153
The MACCIO1 module features the necessary digital and analog I/O’s to support up to four current mode servo drives with ±10V analog command input. A cost-effective and high performance motion control system can be built using the hardware resources of the MACC on-board FPGA and the software resources of the Click&Move® software development environment.
- 8 16-bit analog inputs
- 8 16-bit digital inputs
- 16 optocoupled digital inputs
- 16 optocoupled digital outputs
- 2×4 isolated high speed RS422 differential outputs
- 4 isolated high speed RS422 differential inputs
- 4 incremental or EnDat 2.0 encoder inputs (population option)
-
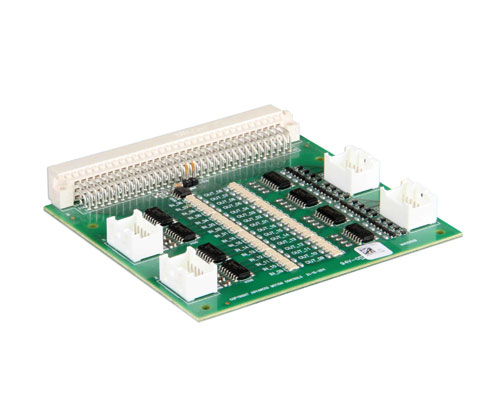
MACC I/O Board MACCIO2
-
- SPECIFICATIONS
- Size (mm)99.9 x 80.0 x 11.5
- Weight (g)53.9
The MACCIO2 module is a minimal solution for simple applications, using switches as input devices and LEDS or small signal relays on the output.
- 16 optocoupled digital inputs
- 16 optocoupled digital outputs
-

MACC I/O Board MACCIO3
-
- SPECIFICATIONS
- Size (mm)219.96 x 99.95 x 11.04
- Weight (g)127
The MACCIO3 module features the necessary digital I/O’s to support up to six position mode servo or stepper drives with Step/Dir command input. A cost-effective and high performance motion control system can be built using the hardware resources of the MACC on-board FPGA and the software resources of the Click&Move® software development environment.
- 12 optocoupled digital inputs 2 high speed differential optocoupled digital inputs
- 12 optocoupled digital outputs
- 12 high-speed RS422 differential digital inputs (2 per axis – galvanic isolation population option)
- 24 high-speed RS422 differential digital outputs (4 per axis – galvanic isolation population option)
- 4 independent encoder inputs supporting encoders or handwheels
-

Filter Card BFC10010
-
- SPECIFICATIONS
- Current Continuous ( A)10
- Inductance (Line to Line)200
- Size (mm)71.0 x 50.6 x 25.0
- Weight (g)210
The BFC10010 filter card provides additional inductance to meet minimum inductance requirements and reduce PWM switching noise. For use with three phase (brushless) motors.
-
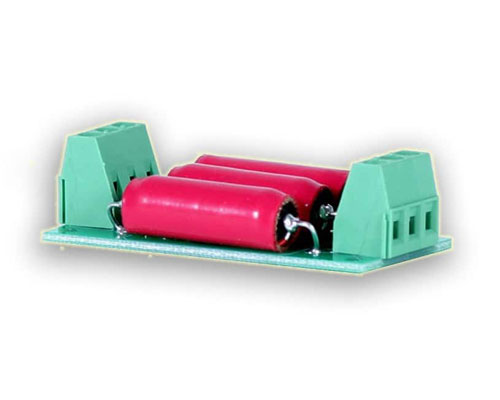
Filter Card BFC1010
-
- SPECIFICATIONS
- Current Continuous ( A)10
- Inductance (Line to Line)20
- Size (mm)56.5 x 28.6 x 15.8
- Weight (g)37
The BFC1010 filter card provides additional inductance to meet minimum inductance requirements and reduce PWM switching noise. For use with three phase (brushless) motors.
-

Filter Card BFC15030
-
- SPECIFICATIONS
- Current Continuous ( A)30
- Inductance (Line to Line)300
- Size (mm)134.6 x 113.7 x 43.5
- Weight (g)1430
The BFC15030 filter card provides additional inductance to meet minimum inductance requirements and reduce PWM switching noise. For use with three phase (brushless) motors.
Custom Servo Drives & Accessories

- One of the things that sets us apart from our competitors is our willingness to make modified and custom servo drives and other products. We’ve been making custom servo amplifiers nearly since the beginning. Today, make up about one third of our business. Modified products make up another third.
在开发一个定制的自定义伺服驱动er, we work closely with them to give them a servo solution that does everything they need. This can include creating drives that have different connectors, shape, number of axes, and other features than our usual product offering.Modified Servo Solution Options
先进的运动控制的off-the-shel提供f products encompasses a wide range of power, performance, and design considerations. However, sometimes a few minor adjustments to a standard product can be beneficial to make things just right for a specific application without the need to invest in a fully-custom solution. A modified solution can quickly be realized and greatly increase machine performance. Best of all, we’ll do it for you!
For years, ADVANCED Motion Controls has happily produced and sold modified versions of our off-the-shelf servo drive products. In fact, modified servo drives make up approximately a third of our business. Whether it’s a tweak to the drive’s loop tuning or a the customer’s logo silkscreen printed on the cover, small modifications guarantee everyone gets a solution that is specifically tailored to them.
With simple modifications, the cost per unit can be near parity with standard products. As quantities go up, the difference will be less. Also, some options are available that may actually make the modified design cost less than the standard. For example, some customers like their units without the servo drive cover, which reduces the material cost.
-
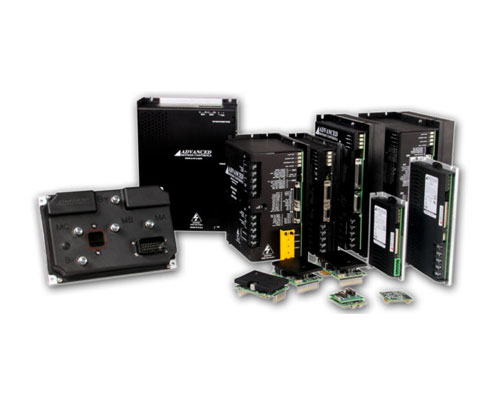
Examples of Modified Products and Options
-
-
- Tuning to a Specific Machine
- Gain Adjustments
- Current Limits and Voltage Limits
- Temperature, Shock, and IP Considerations
- Conformal Coating
- Silkscreen Branding
- Inverted Inhibit Logic
- Quick disconnect, and many more!
-
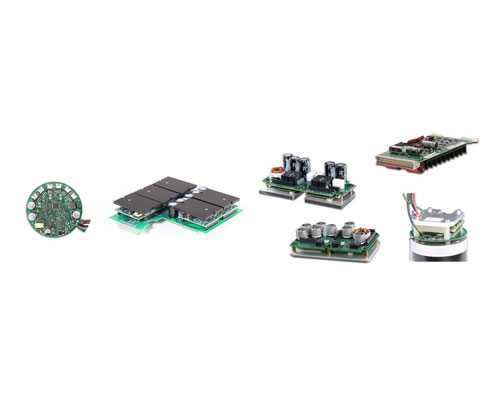
Custom Servo Solution Options
-
- ADVANCED Motion Controls has a broad servo drive offering and the ability to sell products in a modified form, but some motion control applications need something much different from the off-the-shelf models we offer. Thankfully, ADVANCED Motion Controls has the capability to promptly develop and deliver specified products for OEMs with volume requests.
It can start with a crazy idea, feature creep or near impossible specifications, but sometimes you just have to start over from scratch. Starting with a fresh design affords endless possibilities allowing the designer to expand capabilities beyond servo drive functions including full integration of peripheral components.
-

Non-Conventional Shape
-
- Rather than try to fit a square peg into a round hole, why not find the peg that fits? Some motion control applications can be very limited on space for electronics, which means there might not be room for a standard servo drive. This is where a custom servo drive can be essential. We have delivered all shapes of custom drives including round ones that were integrated onto the backs of motors.
It's not always a matter of changing a rectangle into a circle; Maybe you just need to reduce the width and can sacrifice a little length, or reduce the footprint and sacrifice height.
-

Multiple Axes
-
- Individual servo drives are typically used to drive one motor and one motor only. However, many applications have multiple motors working together. Rather than using multiple servo drives, you can get a custom multi-axis servo drive that can control more than one motor at once.
Multi-axis designs are smaller than the sum of their parts because they reduce redundant functions and components and take advantage of board layout.
-

Integrated Drives and Controls
-
- We pride ourselves on manufacturing servo drives and controls, but how about both at once? Instead of using wires and cables to connect servo drives to a controller, drives and controls can be put together and packaged as a single unit.
Integrated solutions greatly simplify supply management, reduce assembly time, save space, and increase reliability. In addition, like a multi-axis servo drive, this can consolidate control of multiple servo axes to a single unit.
-
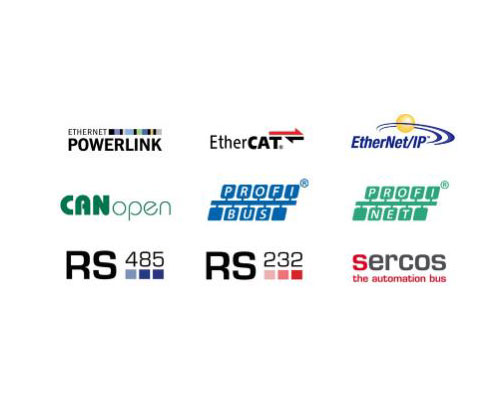
Specialized Network Options
-
- At present, ADVANCED Motion Controls already has standard products available that support EtherCAT, CANopen, Ethernet/IP, Ethernet TCP, Ethernet POWERLINK, Modbus RTU/TCP, and RS-485/232. Any of these networks can be applied to a custom product. However, we have the technology and experience to create custom drives for more networks such as Profinet RT, Profinet IRT, Profibus, and SERCOS III. These customs can even pave the way for expanding our standard network offering.
-
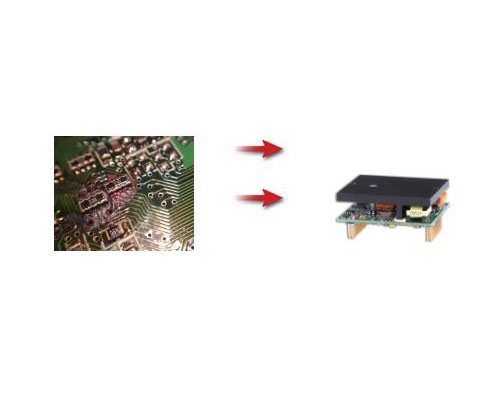
Environmental Considerations
-
- While we have an Extended Environment drive line, sometimes you need something special. All of our extended environment features and modifications can be applied to custom products, sometimes to an even greater extent. For example, we've made custom servo drives that can operate safely in ambient temperatures higher than 100°C and at crushing depths 6000 m below the surface of the ocean. These exceed the capabilities of our standard extended environment products.
-
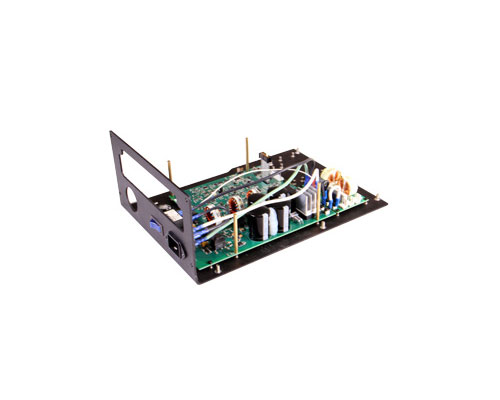
Unique Capabilities
-
- 你需要一个驱动更多的权力比我们的标准offering? Custom. You need a drive with more I/O ports than usual? Custom. You need a drive with special safety features? Custom. You need a drive that shares it's frame with the device? Custom. Want a magnetic encoder or other contactless feedback? Custom.
Examples
- We don't just talk the talk, we walk the walk. We've manufactured hundreds of custom and modified servo drive models over the years. Here we have just a small handful of them for you to check out.
-

High Pressure Servo Drive
-
- This servo drive was used to control an underwater camera traveling 6000m deep in the ocean. It was based on one of our standard solutions, but with a few key modifications that allowed it to work in this application.
- Designed to mount on end of a motor
- Used alternate capacitors and other components that would not be crushed under intense pressure
- Custom baseplate
- Incorporated a rotary magnetic module to replace the traditional Hall sensors and encoder feedback
- Configured the controls for the drive to operate in velocity mode with the host controller closing the position loop
-
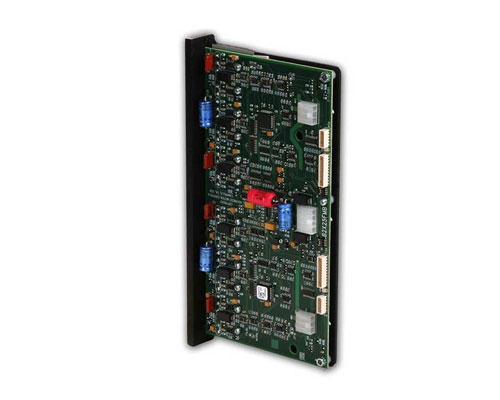
Two-Axis Servo Drive
-
- Two of these drives were used to simultaneously control treads and elbow joints in a military remotely operated vehicle. Each drive was built to control one elbow joint and one tread, rather than having one two-axis drive for the treads and one two-axis drive for the two elbow joints. This way, the number of unique parts was reduced, making replacements easy.
- No switches or potentiometers
- Duty cycle mode operation
- Axis #1: 30A peak, 24A continuous
- Axis #2: 30A peak, 20A continuous
- Custom operating voltage
- Specified peak current duration
- Specified I/O connectors
- Specified motor and main power connectors
- Conformal coating
- Baseplate integrated as control box cover
-
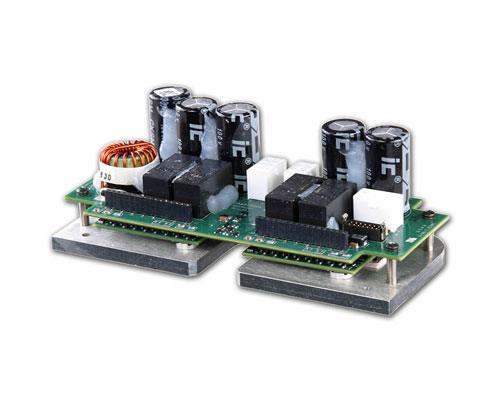
Two-Axis Servo Drive
-
-
- Baseplate shaped to match custom mount
- Dynamic braking relays hold motors while machine is shut down
- Specified connectors
- Built in inductance for motor compatibility
- Additional bus capacitance per customer spec +/-3V command range
- Special access to tuning values
- Built within size restrictions RTV applied to components for shock/vibration
- Conformal coating
- Custom label
- Delivered less than 2 months after receipt of specification
-
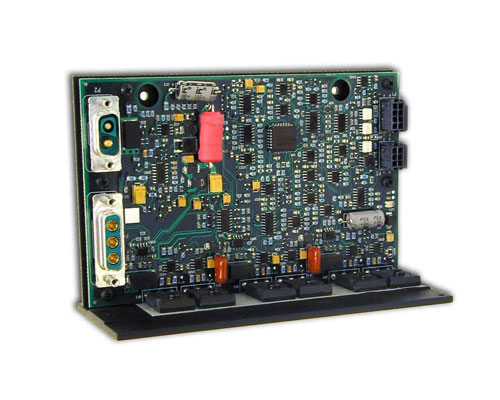
High Current Output Drive
-
-
- 70A peak current (duration 150ms)
- 7A continuous current
- 80kHz switching frequency
- Custom voltage range
- PWM & Direction command
- Duty cycle mode Specified connectors
- Baseplate an integral component in airflow system
-
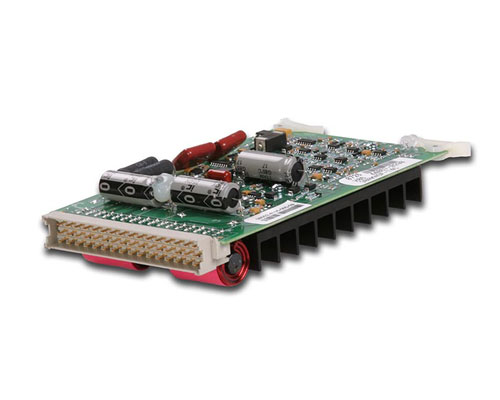
Ultra High Performance Drive
-
-
- 5kHz Bandwidth
- Maximized phase margin for system stability
- No switches or potentiometers
- 3U rack-mount
-
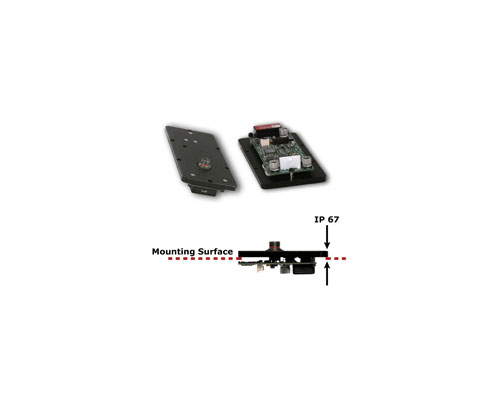
Extreme Environment Drive
-
- This drive controlled the grasping claw in a military remotely operated vehicle.
- MIL spec connector maintains an IP67 seal between the inside and outside while allowing communication and power to the drive
- Expanded temperature range
- Conformal coating
- USB interface for communication and command over the customer's existing communication hardware
- High powered DC/DC converter specified by the customer
-
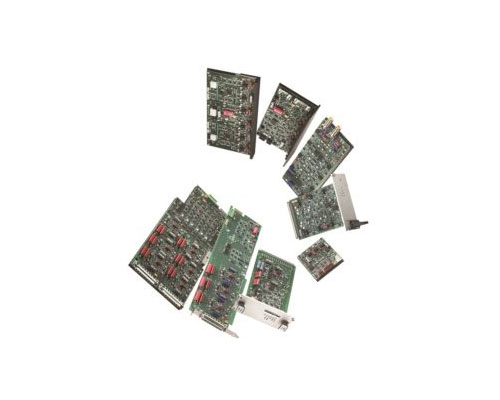
Is a Custom Worth it?
-
- Is it always worth it to seek out a custom solution, especially if there's a way to make a standard product work? All customs are different, so we have to treat each case individually. However, we can still provide some general guidance.
For customs where there is increased complexity it’s best to add up the cost of the individual components for comparison. A multi-axis solution for example can be a combination of two drives and a mounting card. If you added up the price of the individual components it is very likely that the custom 2-axis drive would cost less (Even including engineering costs and NRE).
custom servo drive collectionEven in cases where there is very low volume, you can still come out ahead if you consider the cost of alternative solutions. For example, how much does it really cost to design your own servo drive? We’ve seen customers struggle for years trying to design their own solution and end up with unsatisfactory results and poor reliability. But when given the chance to step in, we have proven ourselves time and again by delivering excellent solutions in just a few weeks or months making our customers very happy.
How do We Make it Happen?
So how is it that we can deliver the best solutions so quickly? The simple answer is – it’s just who we are. Our skill-set for designing servo drives is practiced and honed in daily, and it shows in our time-to-delivery, quality, performance and pricing. We truly do believe everything is possible at ADVANCED Motion Controls, and our custom products make that true.
-
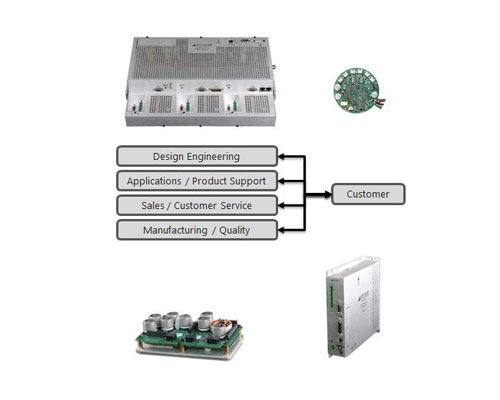
Our Strengths
-
-
- On-site engineering and manufacturing
- Close cooperation between our engineering and applications departments and the customer
- Built on the same equipment and by the same people as standard products
-

Customs Process
-
- A custom design has many advantages when it comes to cost and lead times
- 满足具体的形式,健康,和功能requirements
- Cost savings due to reduction of components or features not needed for the specific system
- ADVANCED Motion Controls' experience and in-house facilities will produce reliable custom solutions faster than any other suppliers on the market