ENVIRONMENTAL TECHNOLOGY21XX
- Offer Profile
- URT is an expert in the following fields of plant engineering:
- Refrigerator recycling
- SDA- and IT- recycling
- Big domestic appliances recycling
- Printed circuit board recycling
- Toner cartridge recycling
- Battery recycling
- LCD recycling
- CRT recycling
- Sorting of WEEE plastics
Product Portfolio
Areas of application

- We offer our customers the necessary technology for the recycling of electrical and electronic scrap in accordance with the latest state of the art and current regulations. URT plants are designed to remove pollutants and generate valuable materials. Through our collaboration on current standards and guidelines, as well as our research in the field of plant technology, we are constantly developing our recycling plants further.
URT has reference plants on the following continents:
- Europe
- 南美
- North America
- Asia
- Africa
with permanent representatives in Turkey, Poland, Italy, Spain, Portugal, Africa, Brazil, North America and Asia
-
-

Fridge Recycling
-
- URT is the world's leading manufacturer of refrigerator disposal plants. For over 25 years URT engineers are working in this field and creating plant concepts for the different customer demands. More than 50 plants worldwide are equipped with the URT technology.
URT refrigerator recycling plants have achieved excellent results especially in the field of CFC's (VFC) recovery. The changeover to CFC-free refrigerants and blowing agents (VHC) was a new and further challenge for URT engineers, because substitutes are flammable and explosive. URT is offering different concepts for the recovery of blowing agents.
轨道交通的员工工作状态ng in different national and international working groups in order to submit their specialized knowledge to be integrated also in regulations and laws.
URT fridge disposal reference plants are located in Europe, North America, South America and Asia.
Fridge disposal plants for VHCs and VFCs
The ozone layer is an important part of our ecosystem and protects us daily against strong, ultraviolet radiation of the sun. A chemical balance ensures that a relatively constant layer thickness remains. Due to their volatileness, chlorofluorocarbons (VFC), released on earth, simply get into the earth´s atmosphere and reach the ozone layer at a height of about 20 km.
氯氟化碳块臭氧生产。的地方al reduction of the ozone layer is the result. During the 70s and 80s it was found out that mainly the VFC used in the in-dustrial sector were responsible for this process and the reduction was started. 195 countries signed the Montreal-protocol in 1989 and resign to use these greenhouse gases mainly nowadays. Substitute materials which have similar physical characteristics but are much more environmentally friendly are used rather now. However, it must be considered that VFC was used in many ways and, despite of prohibition of processing in Europe, VFC is still contained in many products from the past. There is still a huge amount of end-of-life cooling devices on the market which contain not only polyurethane foam in the insulation body but also cooling agents strongly contaminated with VFC. This fact requires to dispose such end-of-life cooling devices properly and to separate CFC with suitable processes. The company URT Umwelt- und Recyclingtechnik GmbH has constructed plants for more than 20 years, which dismantle a cooling device in several work steps, separate them into single components and partially feed to the recycling process. It is very important that this process takes place in a closed room in order to avoid VFC gases escaping to the ambient air.
VHC-selective fridge disposal plants
No more CFCs have been used for the production of cooling devices in Europe since 1995. Those cooling devices which have been produced with substitute materials for the last 2 decades meanwhile represent a considerable part. A common characteristic of all substitute materials for cooling agents and propellants is the flammability of these materials. For this reason, all treatment plants must be constructed as fire and explosion-proof. URT has already realized various concepts successfully. In case of new plants, it is quite reasonable to treat VHC (volatile hydro carbons) and VFC end-of-life cooling devices differently, as the operating costs can be reduced considerably if using different device treatment systems.
-
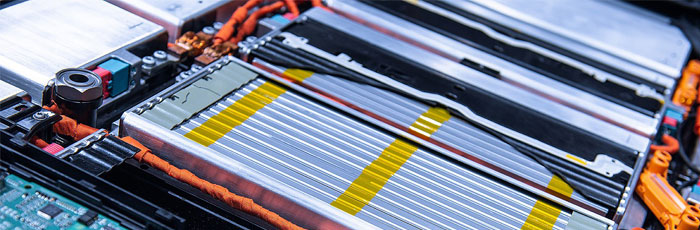
Battery Recycling
-
- URT Umwelt- und Recycling GmbH has developed a process to treat end of life Lithium Ion batteries. Before the mechanical, thermal treatment, the batteries are emptied electrically. After that the batteries will be fed to a shredding unit. This shredding unit enables a precise output fraction in a one step procedure. The shredded total fraction is now automatically fed to a drying phase. The drying process is necessary to enable optimal separation of the black mass later. All process steps from shredding to the drying step are gas-tight encapsulated and are treated with an inert gas, so that exothermic reactions are suppressed. The gas mixture, consisting of inert gas and process gas is sucked out of the encapsulated area and fed to a gas cleaning plant, so that legally prescribed emission requirements are exceeded.
The solid fractions will be cooled and screened afterwards to remove the black mass powder. The remaining fraction is now free of powder and consists mainly of plastics and metals. Metals will be separated by magnet technologies. The non-ferrous metals will be separated from ferrous metals. A mixed plastics fraction will be discharged as well. The innovation of this process is concentrated in the drying phase. In this process step in particular the selection of the drying process, the residence time in the dryer and the necessary temperature profile are crucial.
A customer installation supplied by URT to the Volkswagen AG has been in operation since 2020.
-

E-Scrap Recycling (WEEE-Recycling)
-
- Definition IT
Under the heading "IT", URT is summarizing all the components of WEEE collection group 3 coming from the electrical and electronic waste. In addition to information and telecommunications equipment such as telephones, cell phones, fax machines, printers, copiers and computers, also all devices in the field of consumer electronics such as video recorders, CD / DVD players, game consoles and digital cameras are concerned. In practice, devices coming from this collection group are often treated on plants together with "small domestic appliances". This can take place either in mixture or separately in batch mode. A differentiated treatment of the materials for example, will be then also possible depending on the design of URT plants. Screen devices belonging to this collection group as for example televisions or computer monitors require a separate treatment.
Definition small domestic appliances
在标题“小家用电器”,我们summarize all the components of WEEE collection group 5 from the electrical and electronic waste. In addition to domestic appliances such as vacuum cleaners, coffee makers, toasters, irons or microwaves, also sports and leisure equipment, electric toys as well as electric and electronic (hand) tools have to be added. URT has specialized in the design and construction of complete, mechanical primary treatment plants for this collection group and is offering individually tailored plant configurations with different sorting depth, which can also be linked modularly.
URT plants
Since many years WEEE recycling plants, domestic appliances recycling plants and IT recycling plants are within URT's portfolio. These WEEE treatment plants are often combined with refrigerator recycling plants. But also numerous URT references are on the market, on which non-containing CFC waste electric and electronic appliances are solely treated.
-
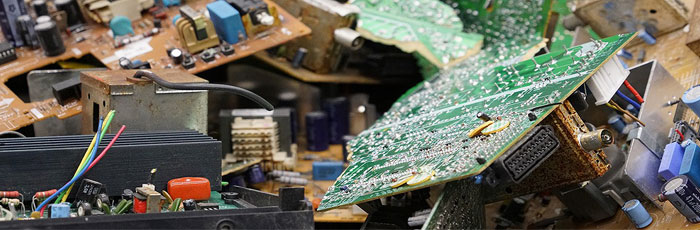
Recycling of Printed Circuit Boards (PCB)
-
- Since many years URT is successfully focusing on treatment concepts for printed circuit boards recycling.
There exists a basic PCB recovery concept which starts with a one-step shredding of the complete end-of-life printed circuit boards. This is done with a low rotating four-shaft rotary shear producing a granule having a size of 20 mm.
Ferrous metals and aluminium can be now separated with this granule size. In this case already 30 % of metals will be obtained which can be sold immediately.
Now precious metals (copper, gold, silver and palladium) are concentrated in the remaining PCB residue in comparison with the original material mass started. Usually this material fraction is sold to copper smelters.
By a further separation shredding and subsequent density separation steps metal concentrates can be furthermore produced, which can be directly melted. By subsequent electrolysis and hydrometallurgical processes copper and precious metals are recovered.
A further technical challenge regarding printed circuit board processing has been already realized by URT. So pyrolysis plants have been designed with which metal concentrates are produced in a pyrolysis furnace, under exclusion of air. All organic substances are directed in a gaseous form into a post combustion chamber for being burned.
At all mentioned methods, sampling of circuit boards is of prime importance. For this purpose, URT has developed a process by which the PCB fractions are separated by sample divider.
Statistically correct samples are resulting, even from large lot batches, which are then used for material analysis.
-

Recycling of toner cartridges
-
- Recycling task
According to the EU Directive 2002/96 / EC, toner cartridges are to be taken out of the printers
之前和复制机器回收,因为toner dust contained is harmful to health.
Above all, however, when cartridges are used commercially, a considerable quantity of cartridges are produced which cannot be refilled due to their design or damage.Toner cartridges are normally destroyed in waste incineration plants. However, they are often used in treatment plants with insufficient explosion protection. For this reason, URT Umwelt- und Recyclingtechnik GmbH Karlstadt decided to develop plant concepts for recycling toner cartridges.
Mechanical treatment
The plant concept described is enabling an automatic removal of the toner powder from the toner cartridge. Every single toner cartridge is put into a feeding device by a co-worker. These cartridges are then fed into a lock system. Thereafter, the cartridges are cracked by a shredding unit, whereupon a sieving machine separates the toner powder from the cartridge components.
Explosion protection
Powder dusts are not only harmful to health, but also explosive. Even during the feeding and shredding process of toner cartridges, a mineral inert powder is injected in the system. This inert powder immediately binds with the toner powder and molecules are formed, which are no longer explosive. The sieving machine already mentioned separates the mixture of toner powder and inert powder inside the closed system. The material is then filled up into a collecting container. This effect has been verified and confirmed by an European institute. The method for the suppression of explosions in the treatment of toner cartridges was applied for a patent.The inert material used is extremely cheap and thus reducing the operating costs compared to an explosive suppression with nitrogen. Additionally to the secondary explosion protection, which is the dosing of the inert powder, further explosion protection devices are integrated in the system. Explosion pressure relief devices, a pressure-resistant version and the extinguishing system form the tertiary explosion protection.
-

Recycling of CRT screens
-
- With the URT cathode ray tube separation device, type CRT, the so-called heat wire technology, front- and cone glasses of the cathode ray tube can be separated from each other. Front- and cone glass will be separated at the connecting line of both glasses.
The funnel glass is the lead containing, funnel-shaped rear part of glass from the cathode ray tube. A wire made of nickel-chromium alloy will be placed at the connectingline around the screen. The different glasses will be separated by a heating up and through the consequently resulting tension of the glass connecting line.
The fluorescent layer, which could be contaminant-laden, will be manually removed by the integrated vacuum cleaner, after opening the cathode ray tube. Subsequently the different types of glasses and the separated metal parts are transported to a further reutilisation. The fluorescent layer will be pulverulent collected in a collecting container.
-

Recycling of LCDs with mercury containing backlights
-
- The changeover from cathode-ray tube screens to flat screens is presenting new challenges to the WEEE recycling industry.
Special care in recycling of these appliances has to be taken since the backlight of flat screens is consisting of thin-capillary tubes containing mercury.
URT Umwelt- und Recyclingtechnik and IUTA (Institut für Energie- und Umwelttechnik have been jointly realized a research- and development project, which examined the conditions of an as much as possible comprehensive and ecologically sustainable recovery. The project was financially supported by the German Federal Environmental Foundation (DBU).
In the course of this LCD dismantling project several thousand end-of-life screens have been collected from the usual mixed return flow and have been dismantled according exactly defined conditions.
One result of this study showed, that shredding of the complete devices is ecologically and for operational safety reasons not acceptable. During shredding process of mercury containing tubes the contained mercury is released (between 3 and 5 mg per tube, up to over 50 tubes per screen) and is contaminating the air, the working environment as well as materials. The control of mercury emissions is extremely difficult and the guarantee for a contamination free treatment of the end-of-life appliances is therefore almost impossible.
Due to this reason URT is offering a LCD dismantling line, with which the capillaries can be riskless removed.
In case a tube will break during dismantling or end-of-life appliances are already containing broken tubes, the inserted filter with mercury sink, specially developed for this application warrants a sufficient health and safety protection in accordance with TRGS 900. The occupational exposure limit (OEL) is always below.
A further extension of the dismantling line is the capillary shredder developed by URT.
Thus URT allows a safe shredding of the tubes dismantled and the recovery of mercury in a mercury distillery.