ENVIRONMENTAL TECHNOLOGY21XX
Videos
Loading the player ...
- Offer Profile
- TheProcess Technology company divisiontakes a new approach to the complex requirements of the market. With its core brands of Allgaier, Mogensen, Gosag and Mozer as well as a global presence in more than 30 countries, this division delivers both standardized and individually produced systems and machines for industrial washing, drying, cooling, screening and sorting.
Integrated thinking and acting – that is what puts us out in front.
Product Portfolio
Appliances & Procedures
Washing

- The group of companies can look back on more than 20 years of experience in the field of Process Technology.
Clients from all over the world use Allgaier washing machines for various functions such as: cleaning minerals and sand, removing foreign particles, handling sludge and contaminated soils, producing high-performance sands as well as for adapting the grain size distribution of particle mixtures. The performance and accuracy of these tailor-made systems are significantly higher than in conventional washing wheels or augers. For example, greater friction between the particles ensures that high-performance sands can be produced without the loss of their fine material proportion. Depending on the task facing the client, a modular system makes it possible to choose between pumps, motors, tank systems and hydrocyclones. The great variety of available combination options means that Allgaier supplies its customers with optimally configured and tailor-made machines and systems.
Reliability, precision and performance – these are the most important properties of our systems.
-
-
-
-
Sandwashing plant
-
- Working principle
Sandwashing machines are designed to obtain sand that meet industry requirements such as grain size, fineness or cleaning harmful materials (clay, organic matter, chloride, sulphates, etc.). The operating method of this type of machine can be summed up as follows:
- Water pulp plus contaminated sand fed to a tank.
- Pumping stage from main tank to cyclone.
- Pulp cycloning stage (separation of sand and clay or filler).
- Water and clay from cyclone enter secondary tank for automatic adjustment of main tank level using buoy system.
- Clean sand from cyclone drained.
- Water and clay or filler leave secondary vat to go to thickening process.
- Washed sand leaves for storage via channel.
- Depending on the process and operating conditions (percentage of material to be removed and the end product quality required), a series of several cycloning stages may be necessary.
Range
The component of each unit, i.e. pumps, motors, drainers, hydrocyclones, etc. will be selected in accordance with the job specifications. The wide variety of combinations available allows a broad range of practically tailor-made machines to be manufactured for each client, thus optimising the investment necessary to produce the facility.
产品的范围从20 T / h的沙子hed in the smallest machine up to 300 T/h in larger versions. Due to the abrasive nature of the materials to be processed and demanding operating conditions, as a standard highly resistant materials, components and linings are selected. Based on an individual study of each product, special solutions are sought for even the strictest requirements. The choice of pump is extremely important. Here, factors such as the abrasiveness and grain size of the material and the concentration of the pulp to be pumped require a special study of the type, speed and linings of the pump.
Drying
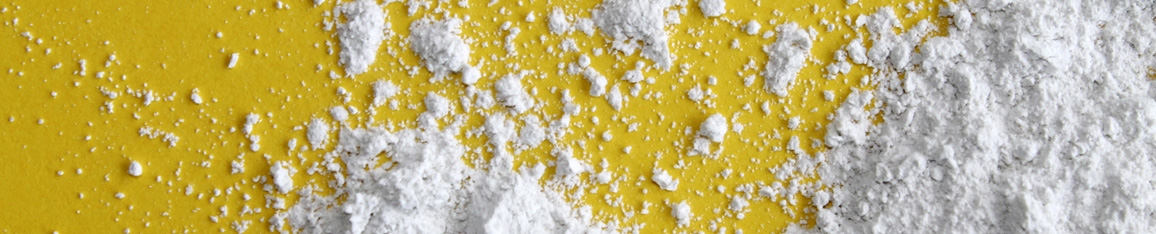
- Allgaier offers its customers dryer systems and machines based on the fundamental principles of rotating drum dryers as well as fluidized bed technology.
These are used in the processing industry for building materials and minerals, in mining, crude and manufactured minerals, plastics and ceramics, animal feeds and fertilizer, pigments, recycling as well as for bio fuels/pellets. Companies from the foodstuffs and pharmaceuticals industry also use the systems for the typical applications of their industries. The drying technology product portfolio includes complete solutions which take the various drying processes as well as processes for cooling and calcining, and rationally link them together with granulating and screening technologies. The "MOZER® System" rotating drum dryer is regarded as a classic industrial drying product; it was developed several decades ago and has been continuously optimized ever since.
Complete drying machines are supplied not only with individual apparatus components but also with ancillary equipment such as conveyor units, silos or electronic machine automation that are installed directly at the customer by Allgaier engineers, who take them into operation. The communication of knowledge in the best sense of the concept takes place in the Technical Center at the headquarters in Uhingen. This is where Allgaier carries out series of scientific experiments and practical tests in order to arrive at made-to-measure solutions for customers all over the world. The insights are made available for use by all subsidiaries and agencies of the Allgaier Group.
From aluminum oxide to citric acid: We find a way to dry your products.
-
-
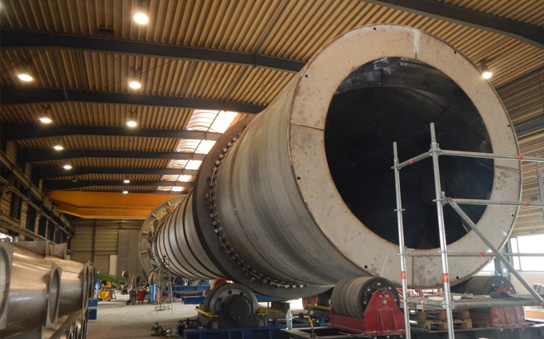
"Mozer" drum dryer cooler system
-
- Allgaier drum dryers or rotary kiln dryers are produced as multi-shell dryers (single, double and triple-shell dryers). They process materials with very differing granulometric properties, or highly fluctuating moisture levels and throughputs with a high throughput rate.
Features
Multi-shell烘干机包括几个管插入ed one inside another. Longer holding times for the solid materials combined with a compact design permit high performance without taking up too much space. The drums are heated directly by oil or gas burners. The combustion chamber on the infeed end ensures that the fuel is used optimally, and that homogenous drying air temperatures are achieved.
Speciality – heating and cooling
Indirectly heated rotary kiln dryers are used for temperature control and calcination at temperatures up to 600 °C. They are used for cooling very hot solids from calcination drums and rotary kilns, and permit heat energy to be recovered effectively.
Applications
In the mineral industry for drying sands, limestone, stones and soil, ores. For fertilisers, wood chips, coal, iron sulphate, filter cakes, sewage sludge, etc.
-
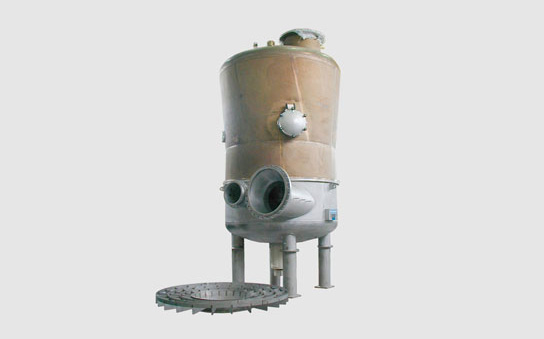
Dispersion dryer FL-T
-
- Allgaier dispersion dryers are used as short-time dryers, predominantly for products with high surface moisture.
Benefits
- Gentle drying in a matter of seconds
- Can also be used as economical preliminary dryers in multi-stage drying machines
- Favourable operating costs due to high water vapour output
- Optimum investment costs due to compact, space-saving design
Applications
Dispersion dryers can be used in almost all industrial areas.
Examples:
- Hydroxides
- Pigments
- Sodium sulphate
- Potato granulate
- Zeolites
- Gypsum
- Cellulose and other fibres
-
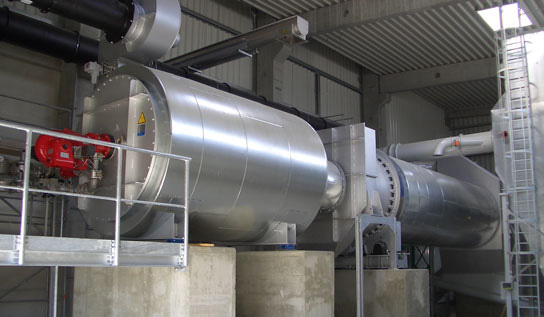
Double-shell dryer TT
-
- In double-shell dryers, drying takes place in both shells in the counter-flow principle using the hot drying gas. Their short length means that double-shell dryers are popular and frequently used.
Special form
A special design of these dryers is represented by Allgaier's MOZER TK and TKplus system drying/cooling drums for drying and cooling in one device.
-
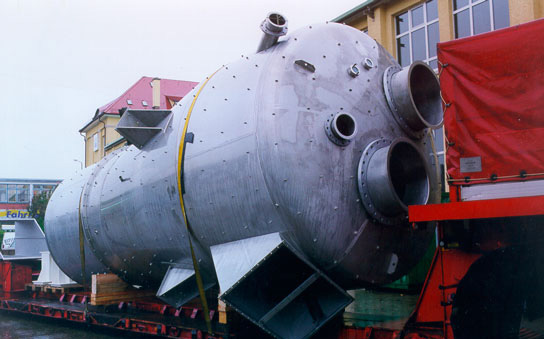
Fluid bed spray granulator WS-GT
-
- Continuous granulation dryers from Allgaier can be used for manufacturing solid and dust-free granulates from fluid precursors such as suspensions and solutions. Dust and powder can be processed further into easily dissolved instant products.
Special quality
- Compliance with defined particle or granulate sizes
- Dimensional stability
- High bulk density
- Good compressibility
- Low dust level
-
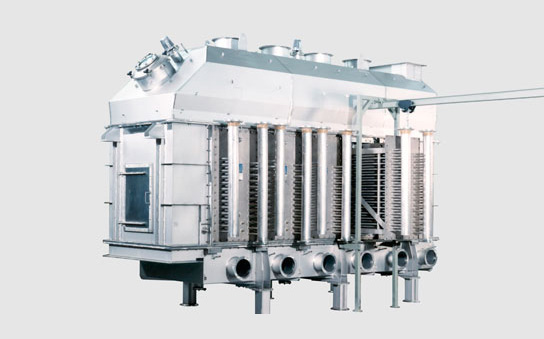
Fluidised-bed dryer with heater WS-HF-T
-
- Overview
Fluidised-bed dryers with integrated heating or cooling surfaces are used for particularly high solid and water vapour performance levels in the salt and soda industry, the fodder industry, foodstuffs technology as well as for plastics.
Features
A particularly high, fluidised solid fill has tube bundle heat exchangers in it. During the process, they permit a continuous heat supply or removal in solid cooling systems. The highest possible solid and water vapour performance can be achieved with comparatively low air quantities and relatively low temperatures.
Benefit
Particularly economical drying processes in compact systems with small footprints and low exhaust air quantities.
应用程序:
- Sodium chloride, table salt
- Ammonium sulphate
- Soda
- Sodium sulphate
- Potato granulate
- Fodder (soy meal)
- Plastics
-
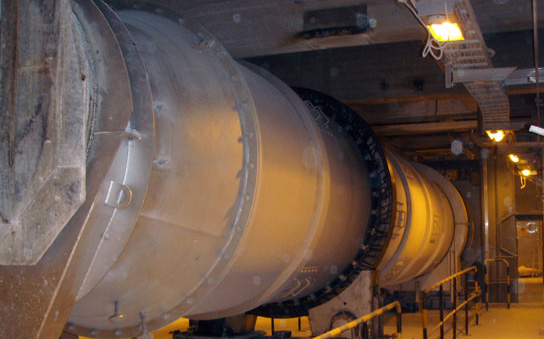
Indirect cooling drums
-
- Indirectly acting rotary kiln coolers are used for cooling very hot solids from calcination drums and rotary kilns, and permit very effective recovery of heat energy.
Applications
e.g. cooling of titanium dioxide
-
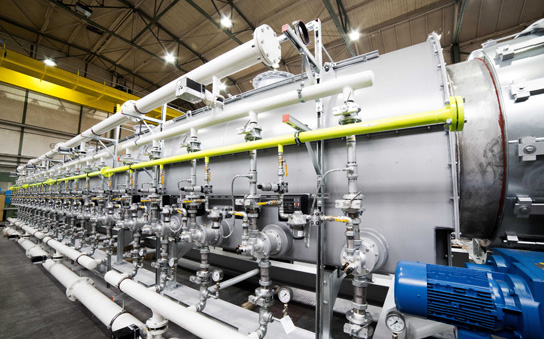
Indirect drying drums
-
- Indirectly acting drying drums are predominantly used for calcination of finely-grained solids at high temperatures. They are also suitable for heating finely-grained materials to high temperatures.
Benefits
The indirect supply of heat for drying means that it is possible to work with a reduced oxygen atmosphere (to avoid product oxidisation or to avoid or reduce harmful exhaust gases).
-
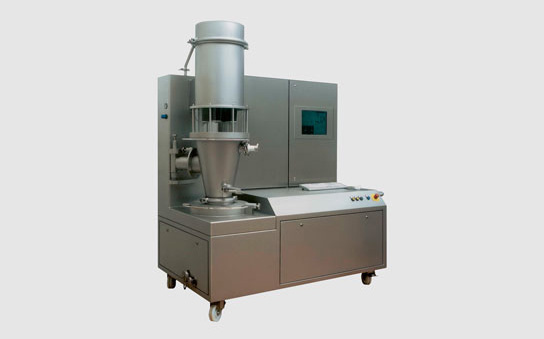
Laboratory dryer WS-CT-L
-
- Allgaier laboratory dryers are especially suitable for developing powders and granulates as well as for manufacturing small product batches. In addition, they can ideally be used for drying, spray granulating and coating small product batches ("WURSTER tube").
Benefits
With different and easily exchangeable distributor plates, it is possible to vary and optimise the process conditions accordingly. The transparent part of the housing makes it possible to observe the processes taking place in the fluidised bed. The ability to exchange different container sizes means the laboratory system offers the best opportunities for scale-up studies.
Optionally, air preparation units are available for drying in the solvent circuit or in the inert gas circuit.
Applications
The main users are customers from chemicals and pharmaceuticals as well as research and development, universities and educational institutions.
-
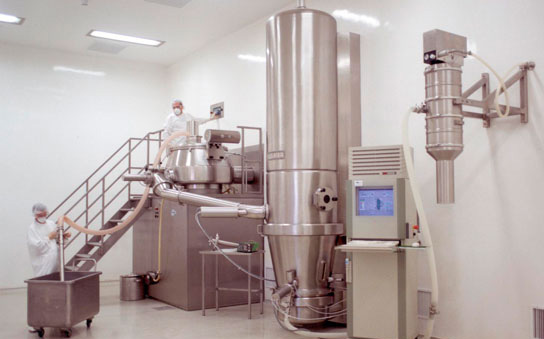
Pharmaceutical system WS-CA
-
- In addition to our continuous fluidised-bed systems, Allgaier offers the most modern, PLC-controlled batch systems which meet GMP and FDA requirements in full.
Benefits
The machine can be positioned inside a production area and a fully separate technical area ("white area"/"grey area"). The system can dry most products that can be fluidised, as well as being used for spray granulation, agglomeration, instant powder generation and coating.
Features
Our systems offer the latest equipment features and a level of quality that meets the exacting requirements of the pharmaceuticals industry.
- Systems of the type "WURSTER" are used for particel-coating.
- Automated systems for machine cleaning (washing in place - WIP or cleaning in place - CIP).
- Optional equipment:
- Explosion-proof
- With systems for drying in the inert circuit gas
- For solvent recovery
- The qualification documentation (DQ, IQ, OQ, PQ) for validation are provided either as parts of the system services or when the system is delivered.
We have particular expertise in designing continuous drying processes for pharmaceutical products.
-
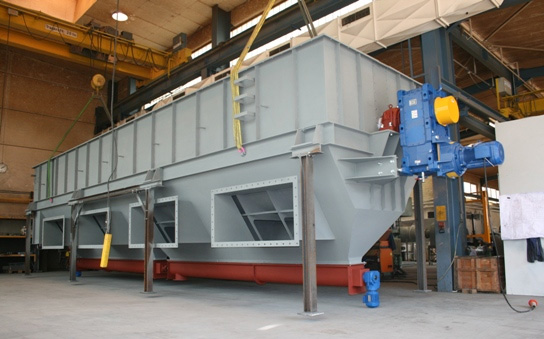
滚床干燥器WB-T
-
- The rolling bed dryer combines the advantages of the drum dryer and fluidised-bed dryer systems, and is used for drying wood chips and organic residues.
Features
The special design of the dryer permits homogenous and gentle drying at a low temperature level. It meets the requirements for processing organic residues in order to manufacture alternative fuels.
Benefits
High energy efficiency, homogenous drying-through of the organic residues due to the long time spent by the product in the dryer. The waste heat from combined heat and power stations used for generating electrical energy can be reused optimally in the roller bed dryer.
应用程序:
- Wood chips
- Cropped biomass
- Alternative fuels
- Sugar beets pulp
- Bush reaping
- Greenery cut
- Trimmings
- Green waste
-
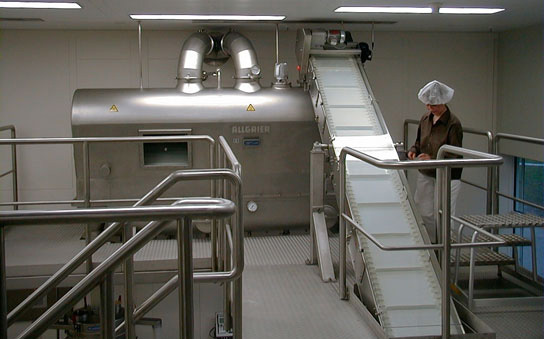
Static fluidised-bed dryer/cooler WS-T/K
-
- The group of static (non-vibrating) fluidised-bed dryers includes, for example, fluidised-bed dryers with immersed heat exchangers (heating surfaces or cooling surfaces), suspension and paste dryers, and spray granulation dryers.
Process
In bulk materials that are easily fluidised and have a close particle distribution, or which are non-adhesive, it is possible to dispense with the supporting effect of vibration transport for fluidisation of the solid.
Higher fluidised-bed heights and somewhat higher air speeds than in vibration drying are used in order to achieve homogenous fluidisation. The higher air flow speeds mean that the upper parts of the dryer configured as an expansion hood are frequently higher and wider than in vibration dryers.
Applications
Drying of plastic granulate, fodder, sugar, yeast, pharmaceutical granulate, potato granulate; expansion of foam granulate, heating of urea, cooling of cocoa, iron sulphate ("copperas") and other salts as well as almost all batch processes.
-
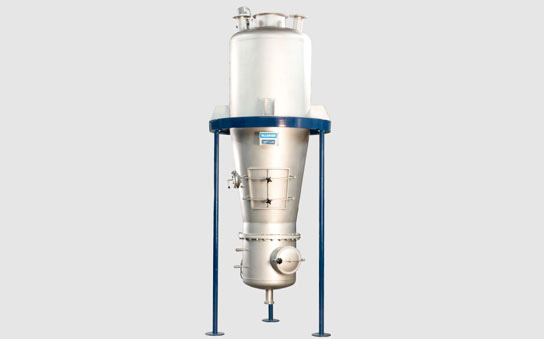
Suspension and paste dryer WS-IB-T
-
- Allgaier suspension and paste dryers make it possible to homogenise and dry suspensions, solutions, heavy pastes or solid filter cakes and to turn them into powders.
Process
The liquid distributed through nozzles is dried on the fluidised inert bodies. This reliably deagglomerates the solid and turns it into the finest powder.
Benefits
A simple machine concept and reliable process control permit:
- Powders without agglomerations
- Good flow properties
- Defined particle size
Our suspension and paste dryers are characterised by their small size and by the fact that they have a correspondingly small footprint. They are particularly robust in response to load fluctuations
-

Triple-shell烘干机TT-TR
-
- Triple-shell dryers can be installed in the most compact space. They are especially suitable for finely grained materials such as quartz sands.
Cold/hot variant
As a special design, the drying can take place in the two inner tubes, whilst cooling is performed in the outer shell by means of the cold ambient air that is channelled to the hot solid matter using the counter-flow principle.
-
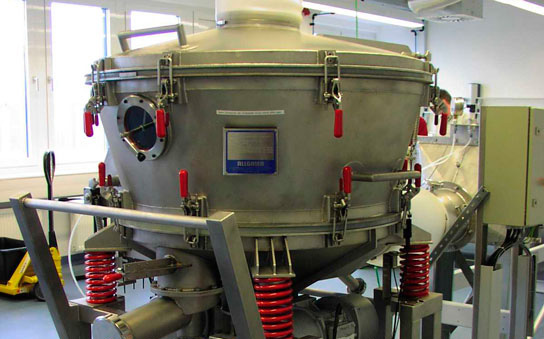
Vibration batch dryer WS-R-V-CT
-
- Allgaier vibration batch dryers are used for treating solids that are particularly difficult to process and which:
Products
- are initially highly adhesive or difficult to fluidise
- have an irregular particle shape and a wide range of particle sizes
- change their properties significantly during drying
Speciality
Adhesion and encrustation in the apparatus is prevented by a stirrer.
Applications
The preferred application area includes gelatine and alginate capsules which can only be dried with difficulty. Vibration batch dryers are also excellently suited for use as an economical alternative solution to drying of medium batches of products in standard batch dryers.
-
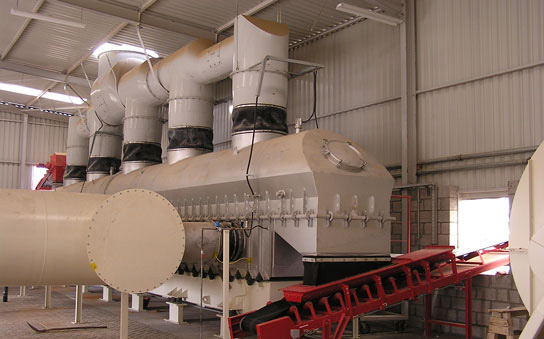
Vibration dryer WS-V-T/K
-
- Allgaier fluidised-bed dryers are supplied as continuous dryers or batch dryers. As vibration dryers, they adapt to the specific properties of the products to be processed and to the process management particularly effectively.
Features
- Low dry material temperatures
- Gentle treatment of sensitive products
- Dryers with optional cooling compartment
- Handling of products with a wide particle spectrum
- Simultaneous product dust removal
- Integrated stirring zone for products with a tendency to clumping
- Influence of the holding time and therefore the quality of products
- Addition of additives through nozzles for granulate drying
- Use of waste heat by exhaust air recovery
Completion possible
Our wide-ranging technology programme means that we can combine our dryers and screening machines to make economical complete plants, e.g. for manufacturing potato granulate. Allgaier also masters special processes for drying pigment filter cakes by means of upstream filter cake pelletisation.
应用程序:
Crystalline products, granulates, dust, powders, coarse-particle substances, minerals and sands, filter cakes from almost all branches of industry.
Cooling
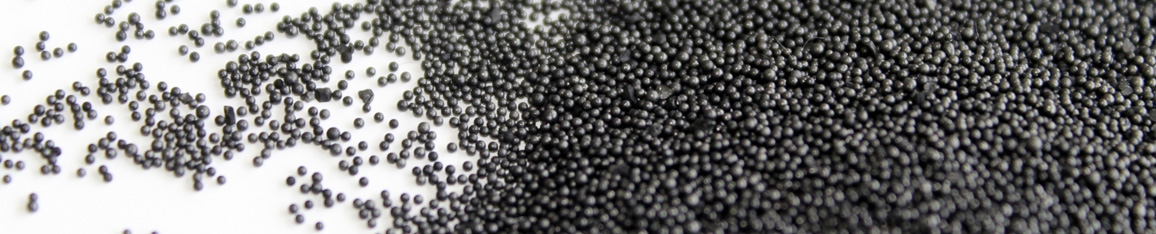
- In many applications, the dried or heated product has also to be cooled before further processing. For this process, Allgaier offers both cooling drums and fluidized bed coolers as well as combined drying and cooling units.
Allgaier rotary cooling systems are becoming increasingly important, and are used for heat recovery from hot bulk goods. Their value is reflected in the energy saving and reduction in resource consumption. In many cases, drying and cooling in fluidized bed systems is also backed up by the fluidization of solid material by vibrating the entire dryer apparatus. This leads to both particularly gentle and even product handling as well as very robust and reliable operation of the system. Many companies that have specialized in specific products use the expertise of Allgaier's Process Technology test laboratories. In the Technical Center at the headquarters in Uhingen, the company carries out series of scientific experiments and practical tests in order to find made-to-measure solutions for customers all over the world in the area of industrial cooling and contract drying.
-
-
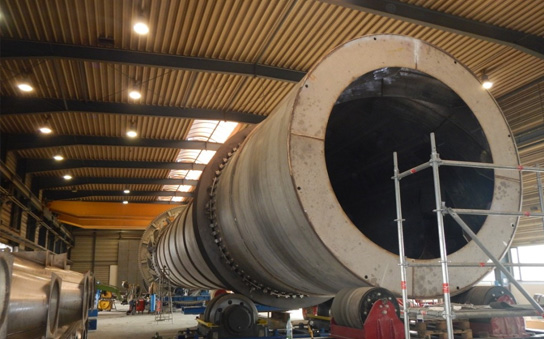
"Mozer" drum dryer cooler system
-
- Allgaier drum dryers or rotary kiln dryers are produced as multi-shell dryers (single, double and triple-shell dryers). They process materials with very differing granulometric properties, or highly fluctuating moisture levels and throughputs with a high throughput rate.
Features
Multi-shell烘干机包括几个管插入ed one inside another. Longer holding times for the solid materials combined with a compact design permit high performance without taking up too much space. The drums are heated directly by oil or gas burners. The combustion chamber on the infeed end ensures that the fuel is used optimally, and that homogenous drying air temperatures are achieved.
Speciality – heating and cooling
Indirectly heated rotary kiln dryers are used for temperature control and calcination at temperatures up to 600 °C. They are used for cooling very hot solids from calcination drums and rotary kilns, and permit heat energy to be recovered effectively.
Applications
In the mineral industry for drying sands, limestone, stones and soil, ores. For fertilisers, wood chips, coal, iron sulphate, filter cakes, sewage sludge, etc.
-
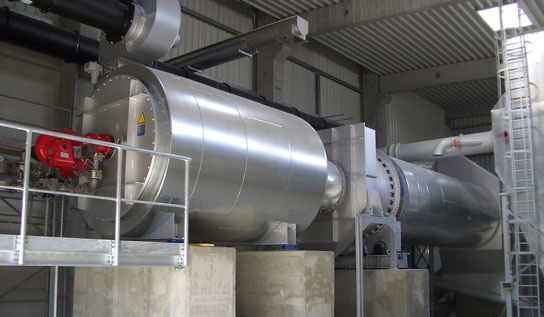
Double-shell dryer TT
-
- In double-shell dryers, drying takes place in both shells in the counter-flow principle using the hot drying gas. Their short length means that double-shell dryers are popular and frequently used.
Special form
A special design of these dryers is represented by Allgaier's MOZER TK and TKplus system drying/cooling drums for drying and cooling in one device.
-
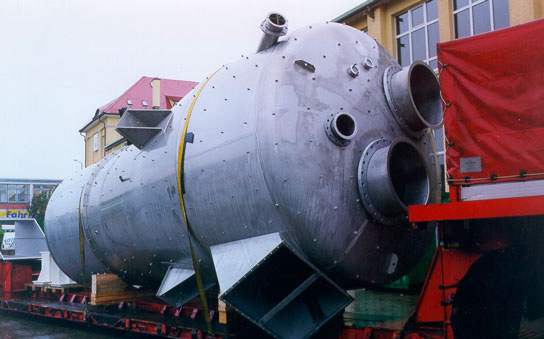
Fluid bed spray granulator WS-GT
-
- Continuous granulation dryers from Allgaier can be used for manufacturing solid and dust-free granulates from fluid precursors such as suspensions and solutions. Dust and powder can be processed further into easily dissolved instant products.
Special quality
- Compliance with defined particle or granulate sizes
- Dimensional stability
- High bulk density
- Good compressibility
- Low dust level
应用程序:
- Fertiliser suspensions
- Distillers dried grains
- Yeast suspensions
- Waste water concentrate
- Gelatines
- Potash solutions
- Sodium nitrate solution
- Pigment suspensions
- Organic acids
- Milk and whey
-

Fluidised-bed dryer with heater WS-HF-T
-
- Overview
Fluidised-bed dryers with integrated heating or cooling surfaces are used for particularly high solid and water vapour performance levels in the salt and soda industry, the fodder industry, foodstuffs technology as well as for plastics.
Features
A particularly high, fluidised solid fill has tube bundle heat exchangers in it. During the process, they permit a continuous heat supply or removal in solid cooling systems. The highest possible solid and water vapour performance can be achieved with comparatively low air quantities and relatively low temperatures.
Benefit
Particularly economical drying processes in compact systems with small footprints and low exhaust air quantities.
应用程序:
- Sodium chloride, table salt
- Ammonium sulphate
- Soda
- Sodium sulphate
- Potato granulate
- Fodder (soy meal)
- Plastics
-

Laboratory dryer WS-CT-L
-
- Allgaier laboratory dryers are especially suitable for developing powders and granulates as well as for manufacturing small product batches. In addition, they can ideally be used for drying, spray granulating and coating small product batches ("WURSTER tube").
Benefits
With different and easily exchangeable distributor plates, it is possible to vary and optimise the process conditions accordingly. The transparent part of the housing makes it possible to observe the processes taking place in the fluidised bed. The ability to exchange different container sizes means the laboratory system offers the best opportunities for scale-up studies.
Optionally, air preparation units are available for drying in the solvent circuit or in the inert gas circuit.
Applications
The main users are customers from chemicals and pharmaceuticals as well as research and development, universities and educational institutions.
-
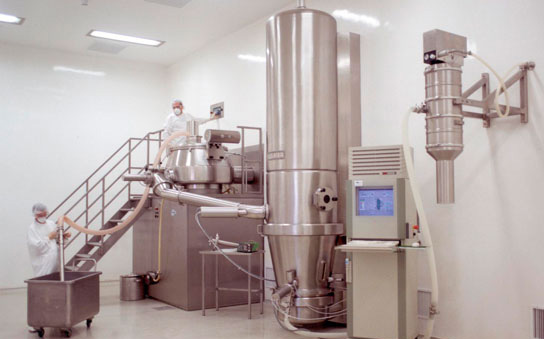
Pharmaceutical system WS-CA
-
- In addition to our continuous fluidised-bed systems, Allgaier offers the most modern, PLC-controlled batch systems which meet GMP and FDA requirements in full.
Benefits
The machine can be positioned inside a production area and a fully separate technical area ("white area"/"grey area"). The system can dry most products that can be fluidised, as well as being used for spray granulation, agglomeration, instant powder generation and coating.
Features
Our systems offer the latest equipment features and a level of quality that meets the exacting requirements of the pharmaceuticals industry.
- Systems of the type "WURSTER" are used for particel-coating.
- Automated systems for machine cleaning (washing in place - WIP or cleaning in place - CIP).
- Optional equipment:
- Explosion-proof
- With systems for drying in the inert circuit gas
- For solvent recovery
- The qualification documentation (DQ, IQ, OQ, PQ) for validation are provided either as parts of the system services or when the system is delivered.
We have particular expertise in designing continuous drying processes for pharmaceutical products.
-
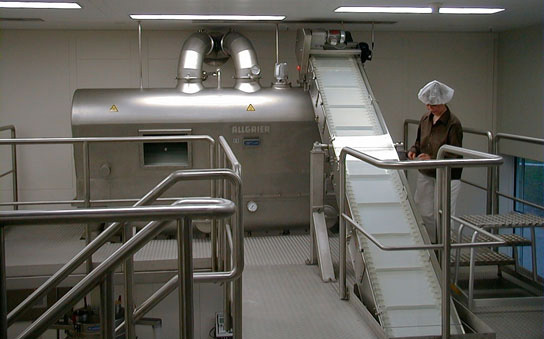
Static fluidised-bed dryer/cooler WS-T/K
-
- The group of static (non-vibrating) fluidised-bed dryers includes, for example, fluidised-bed dryers with immersed heat exchangers (heating surfaces or cooling surfaces), suspension and paste dryers, and spray granulation dryers.
Process
In bulk materials that are easily fluidised and have a close particle distribution, or which are non-adhesive, it is possible to dispense with the supporting effect of vibration transport for fluidisation of the solid.
Higher fluidised-bed heights and somewhat higher air speeds than in vibration drying are used in order to achieve homogenous fluidisation. The higher air flow speeds mean that the upper parts of the dryer configured as an expansion hood are frequently higher and wider than in vibration dryers.
Applications
Drying of plastic granulate, fodder, sugar, yeast, pharmaceutical granulate, potato granulate; expansion of foam granulate, heating of urea, cooling of cocoa, iron sulphate ("copperas") and other salts as well as almost all batch processes.
-
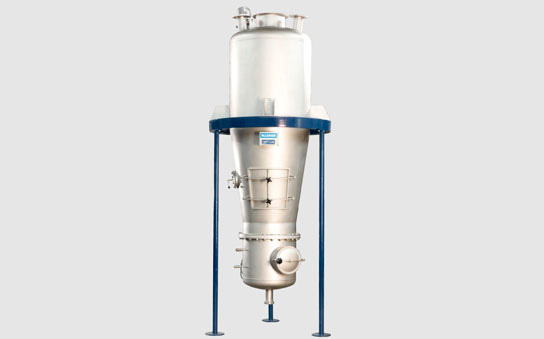
Suspension and paste dryer WS-IB-T
-
- Allgaier suspension and paste dryers make it possible to homogenise and dry suspensions, solutions, heavy pastes or solid filter cakes and to turn them into powders.
Process
The liquid distributed through nozzles is dried on the fluidised inert bodies. This reliably deagglomerates the solid and turns it into the finest powder.
Benefits
A simple machine concept and reliable process control permit:
- Powders without agglomerations
- Good flow properties
- Defined particle size
Our suspension and paste dryers are characterised by their small size and by the fact that they have a correspondingly small footprint. They are particularly robust in response to load fluctuations
-
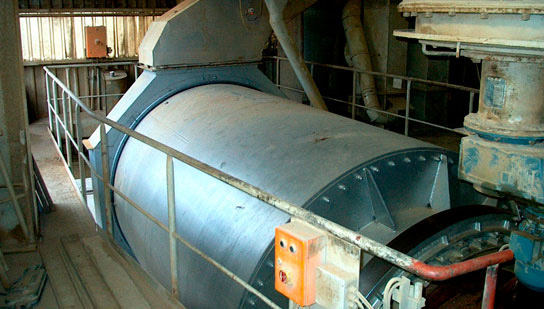
Triple-shell烘干机TT-TR
-
- Triple-shell dryers can be installed in the most compact space. They are especially suitable for finely grained materials such as quartz sands.
Cold/hot variant
As a special design, the drying can take place in the two inner tubes, whilst cooling is performed in the outer shell by means of the cold ambient air that is channelled to the hot solid matter using the counter-flow principle.
-
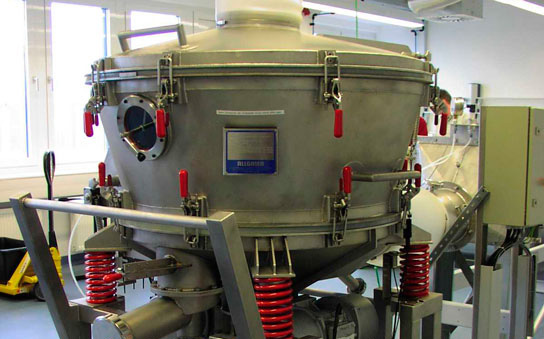
Vibration batch dryer WS-R-V-CT
-
- Allgaier vibration batch dryers are used for treating solids that are particularly difficult to process and which:
Products
- are initially highly adhesive or difficult to fluidise
- have an irregular particle shape and a wide range of particle sizes
- change their properties significantly during drying
Speciality
Adhesion and encrustation in the apparatus is prevented by a stirrer.
Applications
The preferred application area includes gelatine and alginate capsules which can only be dried with difficulty.
Vibration batch dryers are also excellently suited for use as an economical alternative solution to drying of medium batches of products in standard batch dryers.
-

Vibration dryer WS-V-T/K
-
- Allgaier fluidised-bed dryers are supplied as continuous dryers or batch dryers. As vibration dryers, they adapt to the specific properties of the products to be processed and to the process management particularly effectively.
Features
- Low dry material temperatures
- Gentle treatment of sensitive products
- Dryers with optional cooling compartment
- Handling of products with a wide particle spectrum
- Simultaneous product dust removal
- Integrated stirring zone for products with a tendency to clumping
- Influence of the holding time and therefore the quality of products
- Addition of additives through nozzles for granulate drying
- Use of waste heat by exhaust air recovery
Completion possible
Our wide-ranging technology programme means that we can combine our dryers and screening machines to make economical complete plants, e.g. for manufacturing potato granulate. Allgaier also masters special processes for drying pigment filter cakes by means of upstream filter cake pelletisation.
应用程序:
Crystalline products, granulates, dust, powders, coarse-particle substances, minerals and sands, filter cakes from almost all branches of industry.
Screening
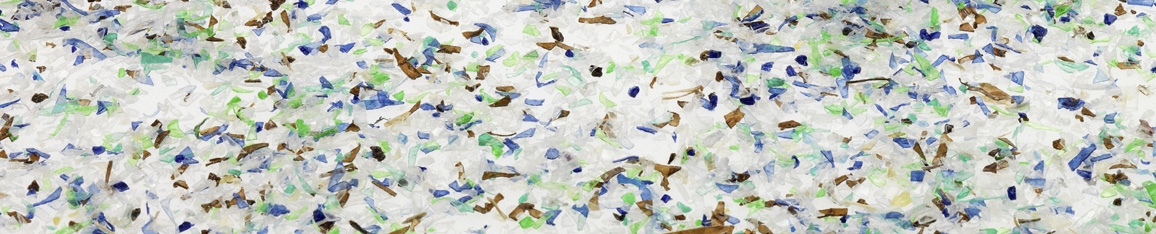
- The bandwidth offered by Allgaier Process Technology is enormous. The company division is a leading supplier of screening machines in Europe and implements both standard and individual solutions for companies from all over the world in the industrial sectors of chemicals and pharmaceuticals, foodstuffs and luxury goods, animal feeds, wood, minerals and metals as well as in the plastics industry.
In industrial preparation and processing of substances of extremely diverse types, the factors that really matter are the quality of the screening material, the choice of screening method and the technology of the screening machine. Allgaier offers a wide range of modern and high-quality classifier machines with a wide range of variants. These can operate in the ultrafine powder range with particle sizes of less than one millimeter. Clean and reliable separation of small, heavy, light, dry and dusty screening materials, as well as even wet or sticky materials to a certain extent, is guaranteed at all times.
Allgaier has the appropriate solution for each task. Tumbler screening machines meet the most exacting quality requirements in ultrafine screening, while flat gyratory screens in the wood processing industry offer convincing performance, and Mogensen sizers are characterized by robustness and a high throughput rate. Using the most suitable machine for the job also means adopting a clear position with regard to the competition, and visibly expanding your own production strength.
Our high-quality screening machines mean we can guarantee our customers the best quality and highest performance.
-
-

Gyratory screening machines ARSM
-
- ARSM – quality that has proven its worth
The ARSM gyratory screening machine is the classic amongst screening machines for the wood industry.
Service
- Loading quantity up to 300 m³/h
- Low-maintenance
- Dust-tight
- Low-noise
Applications
- Wood chips
- Particles
- Sawdust
- Waste wood
-

Gyratory screening machines JUMBO
-
- JUMBO gyratory screening machine for raw wood materials
The JUMBO gyratory screening machine achieves particle fractions with the best quality due to inverted screening.
Service
- Loading quantity up to 170 m³/h
- Suspension principle with very smooth running
- Design without suspension struts reduces the spare part requirements
-
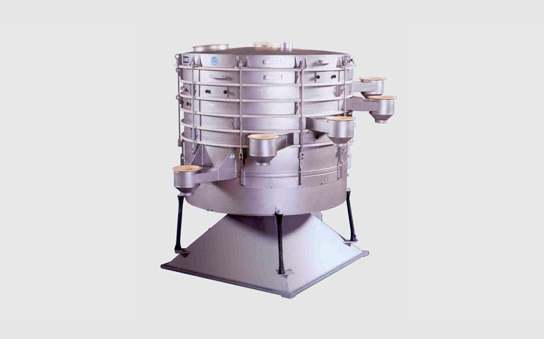
Pharmaceutical screening machines
-
- Tumbler and vibration screening machines
Allgaier produces tumbler and vibration screening machines according to GMP and FDA criteria for applications in pharmaceuticals, food and fine chemicals, for processing high-value powders, pellets and granulates.
The hygienic design includes WIP cleanable and ATEX-certified designs to meet the most exacting customer requirements.
Application
- Pharmaceutical
- Fine chemicals
- Foodstuffs industry
Service
- Fractioning
- Protective screening
- Dust removal
Options
- Electropolished surfaces possible
- WIP cleanable
- IQ/DQ documentation
- Dust of gas-tight
- Connection pipe as clamp connections
- Ultrasonic screen cleaning
- Movable versions
- Multi-deck machines
- ATEX-compliant
-
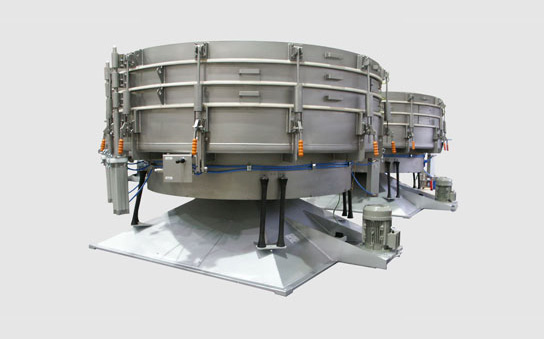
Tumbler screening machines TSM/tsi
-
- The Allgaier tumbler screening system offers optional adaptation to meet the most exacting requirements, and is used in fine and ultrafine screening throughout the world.
The screening system is subject to continuous further development. It offers a wide range of equipment options. The number of different screen cleaning devices available represents a unique feature: Balls, air, brushes, ultrasound or combinations of the above keep the screen meshes clear and make the screening process efficient.
The benefits
- Screening method that is not harmful to the product
- Fractioning down to 0.032 mm
- Dust removal, protective screening, fractioning
- High separation precision with up to 99 % screening quality
- Throughput up to 40 t/h
- 9 sizes with diameters between 600 mm and 2900 mm
- Screen surface/deck 0.28 – 6.40 m2
- One to 5 decks for 2 – 6 fractions
- Greatest hygienic design for pharmaceuticals and food
- Special versions such as mobile frames, quick clamps or folding hoods
-
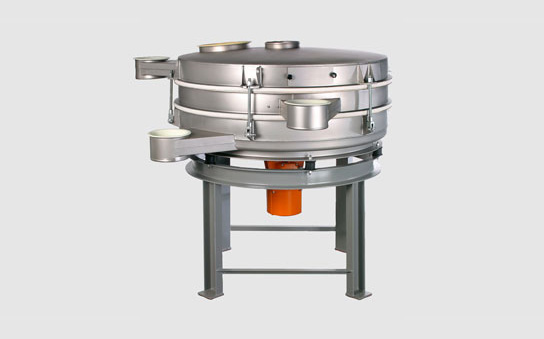
Vibration screening machine VRS
-
- The standard solution
In addition to individual solutions, Allgaier offers a high-performance, economical technology for universal application in the form of the new VRS circular vibratory screening machine.
Particularly high value for money
The consistent use of standardised components and low-complexity manufacture means that our customers have a particularly low-cost alternative available.
Application
- Dry and wet screening
- Protective and control screening
- Dust removal
- Water removal
Technology
- 1 to 3 screen decks
- Internal screen frames
- Sizes: 600 to 1500 mm screen diameter
Options
- Bouncing ball cleaning
- Flexible hoses
-
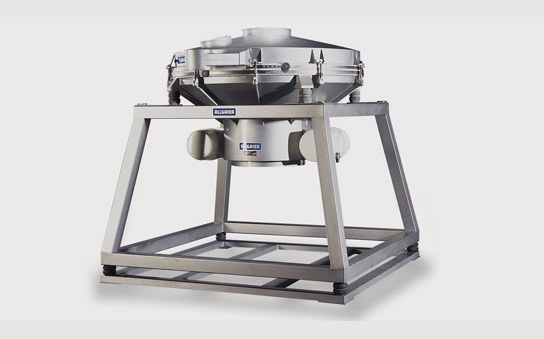
Vibration screening machines VIBRALL D
-
- Allgaier screening machines in the VIBRALL series are used for control and protective screening of free-flowing bulk goods. The central arrangement of the material loading and fine matter outfeed mean that VIBRALL screening machines are especially suited for use in vertical conveyor systems with high transport capacities.
Services
- Control screening
- Protective screening
- Coarse to fine particle area
- Dry bulk goods
- Up to 1800 mm screen diameter
- All branches of industry
Options
- Cover hood or open material loading
- Folding hood
- Quick clamping system
- One or two-decker
- High-quality surface finish for the pharmaceuticals and foodstuffs industries
- Inverted vibration frame
- Bouncing ball cleaning
- ATEX-certified
The optional equipment variants permit a wide range of applications for our vertical screening machines
-
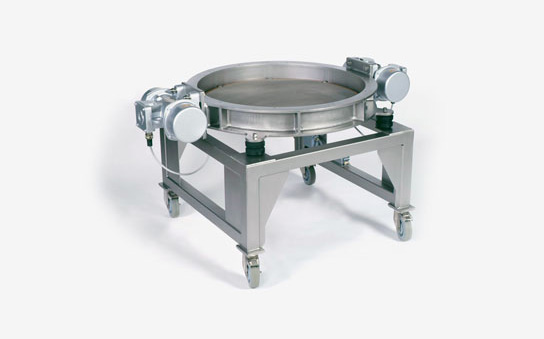
Vibration screening machines VIBRALL F
-
- As a variant of the tried-and-tested Vibrall types, "Vibrall F" offers extended possibilities for protective screening of bagged goods and/or for filling the final product.
Flexible and space-saving
The flat screen is suitable for fixed installation – but can also be configured as a mobile unit for interchangeable inserts. The low height allows it to be used when space is at a premium.
Benefits
- 600 and 800 mm diameter
- Ideal for filling and loading stations
- 极低的height
- Fixed installation or mobile
- ATEX-certified
-
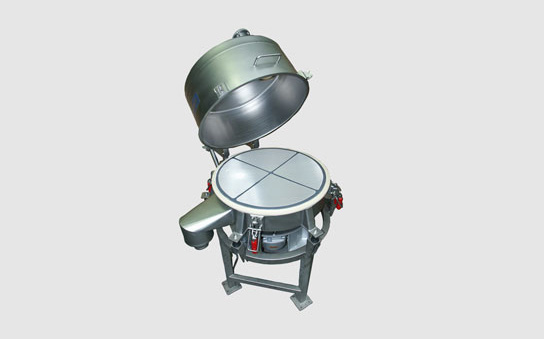
Vibration tumbler screening machines VTS
-
- Screening machines in the VTS series are suitable for efficient processing of almost all bulk goods in the fine, medium and coarse particle ranges.
Wet and dry
The VTS can also be used to optimum effect in wet screening: Straightforward adjustment of the vibration movement enables the screening grade and throughput rate to be adjusted to the particular requirements.
- Classification with maximum 3 screen decks
- Wet and dry screening
- Protective and control screening
- Dust removal
- Water removal
Benefits
- Flexible adaptation to the product
- Modular system permits versions tailored to requirements
- Bouncing ball or ultrasonic cleaning
- Long service lives of the screen fabrics
- Simple and quick screen changes
- Dust and water-tight
- Low energy requirement
- Low foundation load
Sorting

- With the help of machines and systems, raw materials and additives are sorted on the basis of color differences, brightness characteristics as well as item size, composition and purity.
In the sorting process, cameras image more than 2000 particles per second. Following this, computer systems reach a decision within fractions of a second as to whether the particle should be sorted out or not. Sorting out then takes place using pneumatically activated high-performance valves.
The intelligent combination of the latest technology and traditional engineering makes Mogensen sorting machines into essential tools for processing companies which recover reusable materials with regard to commercial aspects and with the highest level of separation accuracy. It goes without saying that the material to be processed must be prepared accordingly before the sorting process. Experience and the interplay between drying and screening play a significant role here. The group of companies possesses the expertise and skills for these interlocking process steps, which mean complete sorting machines with the best quality can be supplied from a single source.
Relatively simple sorting tasks can be solved with less complicated processes. This is where separating tables are used, in which an air flow separates materials with different weights or densities from one another. Separation is achieved using an angled separating tray with a vibration drive. Air is blown across the tray. The less dense material flows downstream in a fluidized bed, without touching the tray. The material with the higher density remains lying on the tray and is transported upstream by vibration. It is chiefly companies from the industrial areas of chemicals, wood, waste and recycling as well as glass manufacture and mineral processing which use these systems for recycled, flat glass and hollow glass just as much as for plastic flakes, minerals, limestone and quartz, as well as for talc, magnesite and rock salt.
The particular advantage of using sorting machines from the Allgaier Group involves the better exploitation of raw materials, increasing product quality and lower processing costs.
We work efficiently and precisely – from economic and ecological perspectives. We share this performance with our customers.
-
-
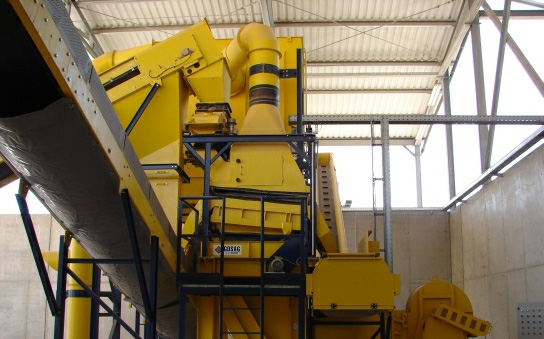
Densimetric tables
-
- Working principle
Dry densimetric separation is achieved on an inclined treatment bottom with vibratory motion. A current of rising air crosses this bottom, which has two effects on the material to be treated:
Less dense products float without touching the base and slide to the bottom part due to the tilt.
More dense products touch the bottom and are pushed towards the top due to the vibration.
The greater the difference in density of the products, the greater the grain size bands treated.
Range
ALMO S.A.U. manufactures two densimetric table models, depending on the level of severity of the application:
- FM model.Used to treat products with low density and medium grain size. They have a robust design with wear and tear parts for severe operating conditions. There are 4 versions depending on their width (0.7, 1, 1.5 and 2.4 m.).
- M model.Used to treat products with a high density and grain sizes up to 80 mm. They have a specially robust design so that materials such as crushed minerals or metals can be treated. Three models are manufactured depending on their width (0.7, 1 and 1.5 m.).
The two models can be supplied with or without a dust collection system and this can be via a cyclone or bag filter. In the case of the M model, an extractor hood and ducts can be installed to fully or partially re-circulate the air.
-
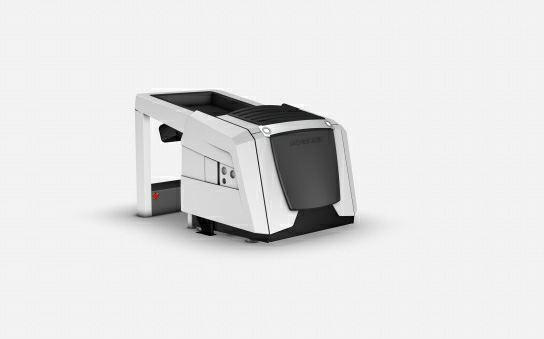
Optical sorting technology
-
- With Mogensen MSort opto-electronic sorting systems and Mogensen X-ray sorting systems, it is possible to remove foreign bodies from materials which were previously not able to be sorted.
Features
MSort separates products with extremely varied compositions and colour differentiations, which are difficult to sort, according to brightness criteria, colour characteristics or unit size and achieves a high level of purity. We have developed various machine types depending on the application.
Benefit
Improved exploitation of raw materials, increased product quality and reduced processing costs deliver not only a financial but also an ecological benefit.
Applications
- Recycling glass (flat and hollow glass)
- Plastic flakes (PET, PE, PP, PVC)
- Different industrial minerals (limestone, talc, magnesite, refractory materials)
- 岩盐
- Particle size analysis
Machinery systems & package units

- Machinery systems and "package units"
以及提供单独的机器,apparatus and lines with various peripheral devices, the Allgaier- Group is able to deliver complete systems and "package units". Very frequently, this involves using a large number of machines, apparatus and lines from the delivery range of member companies in the Allgaier-Group. The plant engineering solutions are supplemented by technologies from suppliers and partner companies, by additional engineering, including third party equipment, or the planning and delivery of steel fabrication.
这导致复杂的加工厂和一个defined benefit due to the ability to manufacture high-quality products. You benefit from partnership with a single contact and supplier with responsibility for the whole thing.
-
Service

- Our service. For you. Worldwide.
As an Allgaier customer, not only do you have the technical benefits of high-quality screening machines and drying systems, you also gain from our excellent service quality. The company's own experienced technicians are experts in our screening machines and drying systems. Maintenance, service and necessary repairs are carried out professionally and quickly, all over the world.
We will help you straight away, even on weekends and public holidays in case of emergency. This involves delivering exchange parts the fastest way possible in order to reduce any downtime to a minimum. To be able to offer our customers this extensive service, we operate a large warehouse and keep a particularly broad range of spare parts.
Spare parts supply
- Consulting
In the spare parts department our experienced team will happily provide their expert advice and support.
Our services offered comprise delivery of the entire range of wearing parts. This starts with remeshing of the screening inserts and extends to direct conversion of screening machines. With decades of experience in screening and processing technology under our belts, we will prove to be your best possible contact.
We offer individual advice
- Which screening system is the best for your application?
- What equipment is necessary?
- Is it possible to retrofit options?
- Is rapid machine conversion guaranteed if there are frequent product changes?
Our service
- 24-hour service for standard spare parts, in an emergency also at weekends and public holidays
- Replacement and wearing parts in genuine quality, for the safety of your machine
- A spare parts concept specially adapted to your requirements – spare and wearing parts without waiting a long time!
Screen meshing
By using modern meshing devices and attachment methods, we ensure the quality of the meshed screen frame. We keep more than 150 different fabric types in stock on a continuous basis.
Our service
- Rapid delivery times
- Use of different attachment methods such as gluing, brazing and clamping, in accordance with FDA/BGVV requirements
Productivity keeps your operation in profit. Think about modernization of your screening machines or lines in good time.
Retrofit
Modernization, conversion or retrofitting of your older screening machine can represent a worthwhile alternative to a new purchase.
Our service
- We carefully and precisely assess the condition of the machine.
- On request, we are also happy to handle the subsequent ATEX certification.
-
Installation/field service
- During the startup phase, we assist you after installation of new machines, and support you in the commissioning. As a result, we aid you achieve the intended production capacity and quality as rapidly as possible. Our on-the-spot service helps you to rectify application problems with precise fault diagnosis. When production conditions change, we will also be pleased to readjust the machine settings.
Allgaier offers you qualified service packages for the entire lifecycle of your machines and systems. From startup through to preventative maintenance and service concepts, as well as continuous process optimizations, we are at your side right from the start.
It goes without saying that we also place our specialist knowledge about screening machines at the disposal of your operating personnel. We train your employees directly on your premises or, in the Allgaier customer centre, explain relationships that are relevant to the process and maintenance.
Here are some of our service products
- Performance and quality increase by conversion to double-performance machine
- Adaptation of the machine to different cleaning devices
- Monitoring of the machine by rotation speed monitoring
- Lifting devices for optimizing the screen change
- Subsequent ATEX certification
- Adaptation of the machine to different closing variants
- Conversion to segmented screening inserts in order to simplify screen transport and remeshing, above all with screens of 2.6 m diameter and more
- Screen meshing service: on request, we collect the screen from you and deliver it re-meshed back to you.
- Repairs and preventative maintenance on-site (even on weekends and public holidays in an emergency)
Second-hand machines
Are you looking for a bargain on a screening machine? We restore used screening machines to optimum condition by technical service and genuine parts, which may well be just the economical solution you are looking for.
-
Contract screening
- Use the full range of services offered by the Allgaier Technical Centre. We offer capacity ranging from small batches up to production of several tonnes.
We are there for you
- If you are encountering capacity bottlenecks in your own screening and/or drying
- If you do not have your own production system available
- If there is a sudden system failure or in case of conversion
- For model quantity production
We process materials from the following areas
- Chemicals
- Plastic
- Stones/soil
- Minerals
- Powder coatings
- Metallurgy
-
Service drying technology
- You deserve only First Class Services – This is our standard. Allgaier Process will deliver a superior technology so you can satisfy your customers with maximum performance, efficiency and safety – thus giving you a competitive advantage. Up-time and Process Availability translates into more profits. With Allgaier’s professional advice and support, you can be assured of the most robust and technological superior equipment and processes.
Consulting
All processes start with an idea. It is our job to take your ideas and develop the right technology solution. When it comes to Drying, Allgaier has decades of Experience coupled with a Test Centre for trials. Allgaier Process Technology offers nearly every type of Industrial Drying Technology. Our highly skilled and professional staff will support you with expert help, and exact advice.
- Individual training
- Defining maintenance intervals and preparation of service contracts
- Assistance in choosing the right drying system from a wide range specifically for your personal needs
- Balanced spare parts concept for your individual needs
Service
The Allgaier Service Team partners with you so you can run your plant under optimum conditions. Unnecessary downtime and annoying waiting times for Factory Skilled and competent help are reduced by preventive maintenance intervals, fast track response, rapid spare part delivery and immediate repair services.
- Scheduled inspections, preventive maintenances, fast help in emergency situations
- Fast delivery of standard spare parts
- High quality original spare parts to ensure the safety of your plant
- On-site support to spot and prevent potential risks
Optimizing
准备好一个成功的未来。我们的经济l modernizations solutions provide performance, safety and added value to the whole life cycle of your plant – so you can concentrate on your main business.
Our range of services includes:
- 分析现有关于能源植物consumption and throughput rate.
- Modernization of old- and third-party drying plants
- Retrofitting of drying and processing plants to new areas of application
- Consulting and projecting of heat recovery systems
- Inspection of older heating methods together with our service partners worldwide.
We ensure you the best and competent support in every situation
-
Contract drying
- Use the complete range of services of the Allgaier Technical Centre – we have the best equipment. We offer capacity ranging from small batches up to production of several tonnes.
We are there for you
- If you are encountering capacity bottlenecks in your own screening and/or drying
- If you do not have your own production system available
- If there is a sudden system failure or in case of conversion
- For model quantity production
We process materials from the following areas
- Chemicals
- Plastic
- Stones/soil
- Minerals
- Powder coatings
- Metallurgy
-