De Dietrich Process Systems
Videos
Loading the player ...
- Offer Profile
- DE DIETRICH PROCESS SYSTEMS
is the leading global provider of Process Equipment, Engineered Systems and Process Solutions for the fine chemical, chemical and pharmaceutical industry.
Product Portfolio
Reaction

- For highly corrosive materials or end products that require ultra-pure environments, De Dietrich Process Systems reactors are the best choice to achieve process performance goals efficiently and economically.
We are able to provide complete engineered solutions for reaction. Our reactors are available as standalone equipment or can be incorporated into a system, including upstream and downstream equipment.
As a chemical process equipment specialist, our main purpose is to ensure both the mixture of reactants and heat transfer, resulting in a guaranteed process efficiency.
Reaction units are primarily manufactured from glass-lined steel, borosilicate 3.3 glass or stainless steel with a variety of accessories and instrumentation. Each method of construction has its own advantages for process and operation considerations.
GLASS-LINED REACTOR
- Our glass-lined reactors have been at the heart of chemical operations for over a century. These are robustly designed and manufactured to stand up to very harsh environments.
-

THE DIN RANGE
-
- This range of reactors meets every standards and is able to cover all your needs whatever your process. The perfect control of our manufacture and quality procedures leads to provide high quality products every time.
The polyvalence and reliability in every circumstances
All our glass lined-steel reactors are in accordance with the DIN 28136.
Three types of glass-lined steel reactor design AE, BE, CE which can be provided with jacket or half-coil and a wide selection of agitation solutions.
BE
closed-welded reactors without a large main opening for higher pressure ratings.
AE
clamped or flanged-top reactors designed with a removable top head for today’s cleanability demands.
CE
rugged, heavyweight reactors with large top head main cover that allows for installation and removal of one-piece agitators.
-
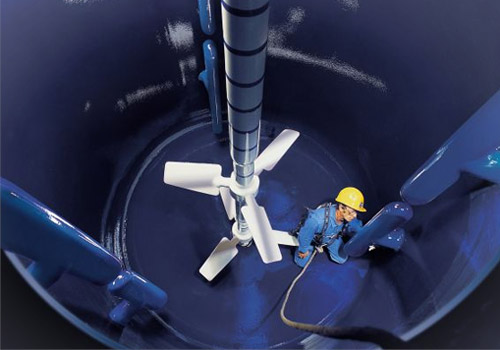
THE OPTIMIX® REACTOR
-
- Exclusively from De Dietrich Process Systems, the OptiMix® reactor offers tremendous optimization of the mixing performance of glass-lined steel reactors by integrating three baffles on the vessel wall.
OptiMix® reactor: The efficient technology
This patented design enhances heat transfer, solids suspension and distribution, gas dispersion, gas flow rates and mass transfer.
The OptiMix glass-lined reactor's performances are based on the integration of three baffles onto the vessel wall. This leads to a notable improvement in the capacity of the mixture and in heat transfer compared to the standard DIN series.
The result is that all the nozzles remain free for the process. This arrangement considerably improves the hydrodynamics by using an optimized baffling effect.
The profile of the paddles prevents the accumulation of crystals in the event of crystallization. This design satisfies two of industry's primary requirements: optimal process efficiency and improved cleanability of the reactor, as well as a reduction of the amount of dead zones which generally occurs with a standard, nozzle-mounted baffle.
CHARACTERISTICS
- OptiMix reactors are lined with DD3009 glass for superior corrosion resistance.
- A complete range standardized from 6.3l (glass) up to 25m3 (Glass-lined).
- Working conditions:
- Pressures from full vacuum to 6/10 bar
- Temperatures from -30°C to 260°C
- The OptiMix reactor range is fitted with an integrated sensor on the shell which enables control of very small reaction volumes.
- Equipment is interchangeable with standard reactors of the same size. OptiMix comes standard with two coil zones and a GlasLock® agitator, with optional jacket.
-

PHARMA REACTOR
-
- Innovative reactors provide optimal cleanability
Advanced solutions for efficient cleaning
CHARACTERISTICS
- A wide range from 63 l up to 630 l
- Optimization of the thermal transfer and the mixing performances (OptiMix®)
- Glass-lined flat cover with excellent surface finish and pad nozzles
- Polished 316L Stainless Steel sheathing on drive and motor
- CIP validation
- Successful test results
ADVANTAGES
- OptiMix design for high agitation performances, more connections and less dead zones
- A range of advanced solutions like:
- Fused Glass quick release opening (by request)
- Flat seal outlet valve
- Pad nozzles
- Reversed mechanical seal
- High performing spray balls: different materials available (in Alloy or PTFE)
-
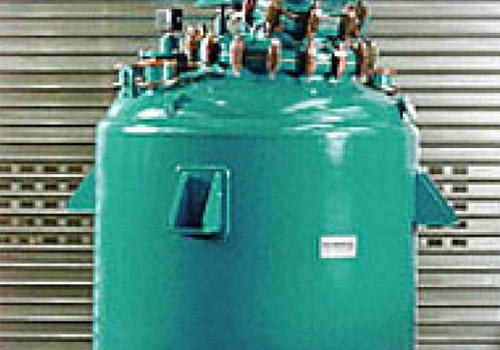
EURO EZ
-
- The Euro EZ reactor has been designed for easy processes but still feature the same level of quality found in the DIN range. This guarantees equipment reliability.
The economical solution for easy processes
For this design, new calculation data is taken into account which allows us to reduce steel thickness and weight, the number of clamps, and the sizing of agitation and drive assemblies.
Standardization has been deeply applied to this range of products, which gives you at the end a reactor that competently fulfills basic process requirements, in a total safety and reliability, for lower investment costs.
CHARACTERISTICS
- Pressure: internal -1 to 3 bar ; jacket 4 bar
- Temperature: -10 to 150° C
- Viscosity: max. 500 cP
- Specific weight: 1250 kg/m3
- Codes: ASME - AD2000 - CODAP
ADVANTAGES
- De Dietrich DD3009 high enamel quality
- Nozzles with different connections possibilities (DIN, ANSI, JIS…)
- Specific drive with direct coupling, dry single mechanical seal, (C/SiC) and gearbox motor
- Reduced maintenance costs
- Impeller agitator and baffle equipped with DR2 temperature probe
- Possibility of support by legs or lugs
- Jacket equipped with agitation nozzles
GLASS REACTOR
- Our range of reactors and components, manufactured from Borosilicate Glass 3.3, provide excellent resistance to chemical attack and corrosion as well as transparency for optimum visual observation.
- PERFECT OBSERVATION OF THE PROCESS -
- UNIVERSAL USE due to :
- high corrosion resistance-
- wide temperature range -
- vacuum resistance -
- EASY CLEANING due to:
- transparency -
- smooth surface -
-
-
-
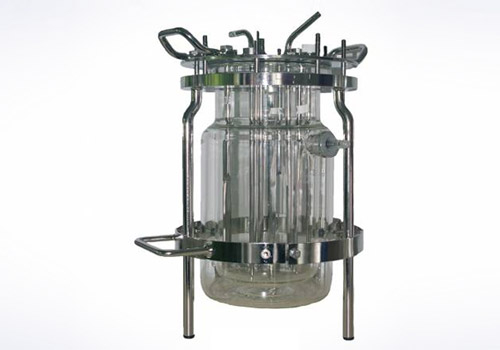
BIOREACTOR
-
- A new range of reactors from 5 to 20 liters developed with users to increase cell culture yields
GMP REACTOR
- Borosilicate 3.3 Glass according EN1595 with or without jacket
- Monobloc inner vessel, ≤ Ra 0.02 μm
- Customized design (Optimization of the KLa)
AGITATION
- Minimization of agitation restrictions (CFD)
- Mechanical or magnetic
COVER & ACCESSORIES
- Stainless steel 316 L or Alloy
- Ferrite content < 5%
- Electro polished finish Ra < 0.5 μm
- EPDM gaskets with FDA, USP certificates
SERVICES
- QA / QC plan
- FAT, SAT
- Qualification : DQ, IQ, OQ
- Aftersales and spare parts
DOCUMENTATION
- According to GMP requirement
CONTROL / SUPERVISION
- Entry level with variable speed control
- 21 CFR part11 Control interface (on request) pH, RedOx, T°, aeration (KLa), stirring speed,...
MIXING
- Efficient mixing is essential to the reaction process and is the major concerns of the chemical and pharmaceutical industries. Reliable agitation, mixing and heat transfer solutions are necessary to improve performances and reduce production costs.
-
-
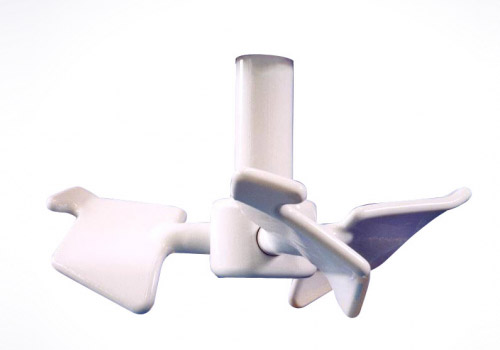
THE GLASLOCK® SYSTEM
-
- The GlasLock system allows installation of specific blade profiles as well as several flights of blades to better suit the process requirements. This system, therefore, makes it possible to obtain small, non-agitated volumes less than 1%.
The only system in the world with removable blades
This system has been especially designed for BE reactors where the main opening is the manhole, but is usable for all kinds of reactors.
Fitting and dismantling are carried out laterally, making it possible to work on the scraping agitators without completely dismantling them. With multi-tiered agitators, it is possible to modify just one stage independently of the others by leaving the agitator in place.
The assembly of a blade in its conical emplacement, both fully enamelled, is done using a manual tool according to a simple procedure. GlasLock uses a single hub offering greater flexibility by allowing all types of blade profiles to be fitted. This technology reduces the time needed to dismantle the drive, when this is required.
Our teams can define and install a blade profile according to your process and your agitation parameters. This technology makes it possible to fit several flights of blades to better suit the reaction.
ADVANTAGES
- Multi process-system
- Individual dismantling of the blades
- Small agitated volume
- Easy maintenance
- Limited stock of blades
-
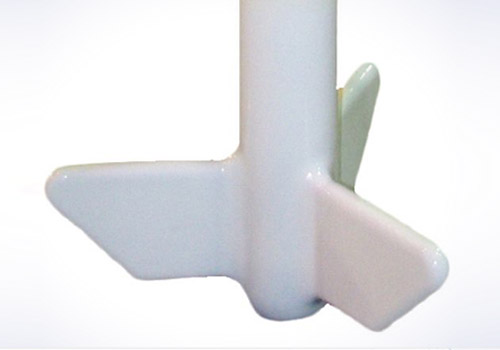
MONOBLOC AGITATORS
-
- This range of agitators, covered with our DD3009 enamel, is dedicated to reactors featuring a large opening (AE and CE reactors)
IMPELLER AGITATOR
The Impeller is an universal agitator giving a radial flow.
Having three curved blades, it works between 50 and 200 RPM.
ANCHOR AGITATOR
The Anchor is an agitator specially used in viscous products and to increase the heat transfer. Its shape is adapted to the reactor. Low rotation speeds, from 20 to 80 RPM.
TURBINE AGITATOR
The Turbine is specifically adapted for dispersion reactions. Having three to six welded blades, it can work up to 500 RPM.
FRAME AGITATOR
The Frame can be used for homogenization on a large range of viscosity.
-
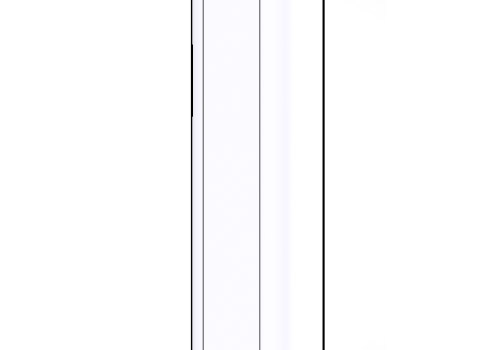
BEAVERTAIL BAFFLE
-
- The flange-mounted Beavertail baffle with temperature sensing system offers high performance mixing even at low liquid levels
The high performance Beavertail Baffle
CHARACTERISTICS
海狸尾巴挡板是法兰连接允许easy, no-entry installation and removal. It can be installed through one of the standard nozzles on a De Dietrich reactor as well as any other glass-lined reactor. No special holder is required for the baffle. Our DR type temperature sensor comes standard.
The flange-mounted design reduces the possibility of leaks through gaskets, since only one gasket is required for a seal.
Sized to fit vessels from 370 liters to 110,000 liters (popular sizes from 370 liters to 20,000 liters are normally available from stock for quick shipment).
Headroom approximately equal to the length of the baffle is required.
ADVANTAGES
- 不需要输入本月船或删除内容all or change-out the baffle
- Chance of leaks substantially reduced with only one gasket required for a seal
- Sensor change out/maintenance while vessel is in service
- 高性能混合液体即使在低水平
-
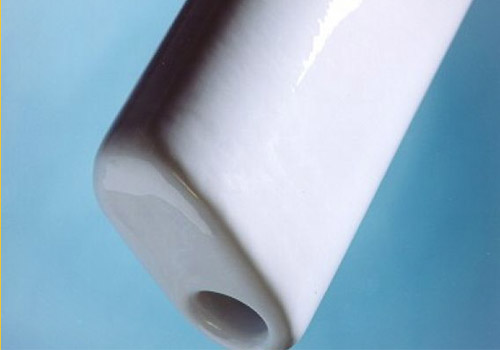
DIP PIPE BAFFLE
-
- The innovative combination dip pipe/baffle provides four functions in one piece of equipment.
Baffling, product introduction, sampling and temperature measurement can all be performed from a single nozzle, freeing up additional nozzles for other functions.
Installation requires a DN200 (8”) nozzle or larger. A bellow or expansion joint must be used in conjunction with the baffle/dip pipe to compensate the thermal expansion of the inner pipe.
ADVANTAGES
- Flange-mounted for easy and inexpensive installation without having to enter the vessel and cause unwanted delays in production.
- Completely lined with DD 3009 glass, the unit has optimum corrosion resistance and meets cGMP requirements for cleaning.
- The temperature sensor can be removed or replaced while the vessel is still in service.
-

MULTIPROBE® SAMPLING SYSTEM
-
- The exclusive design of the MultiProbe system allows a perfectly representative sample to be "captured" in the very heart of the reaction process
The easiest way to take a representative sample without opening the manway!
CHARACTERISTICS
Once installed, the MultiProbe is immediately operational without need of further adjustment. Its design facilitates its installation on small reaction units. Its compact over-all dimensions make it possible to be integrated in a congested peripheral environment.
多功能探针能够完全clean the entire sampling circuit with the use of an appropriate solvent.
The ability to take a truly representative sample with no need to depressurize the vessel or lose the insert atmosphere makes this product ideal for chemical and pharmaceutical processes where contamination is usually an issue during sampling.
ADVANTAGES
- Representative Samples
- 最小化停机时间
- Health and Safety Benefits
- Process Control
- Multipurpose Functionality
- No Additional Support
Distillation
- Separation of chemical components is often achieved by using distillation or evaporation. De Dietrich Process Systems has designed such equipment for many years within the QVF brand of our integrated business while the De Dietrich glass lining brand has designed and built many distillation columns over the years.
-
-

EVAPORATORS
-
- Evaporation is a common activity and we have a range of thin film evaporators for heat sensitive materials as well as the more basic heated vessels with condensers and receivers.
-
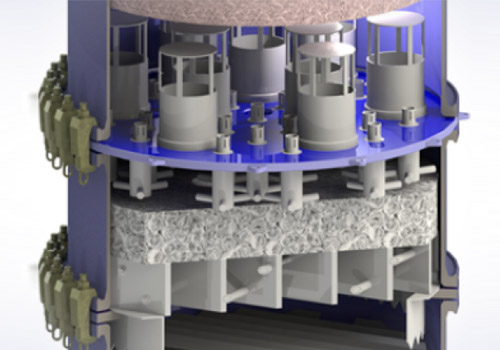
PROCESS SOLUTIONS FOR THERMAL SEPARATION
-
- Columns and internals for aggressive media
HIGHLIGHTS
- Corrosion-resistant materials for corrosive substances
- Vacuum and pressure-resistant for a wide variety of process conditions
- Temperature ranges up to +230°C
- Diffusion-proof for sustained corrosion resistance
- Smooth surfaces that stay clean, non-stick effect
- Abrasion-resistant for a long service life
- Compact design to keep investment costs down
- Reliable process design for further investment cost reduction
- Solutions optimised for efficient processes
- From initial design to component manufacturing to commissioning – from a one-stop shop
-
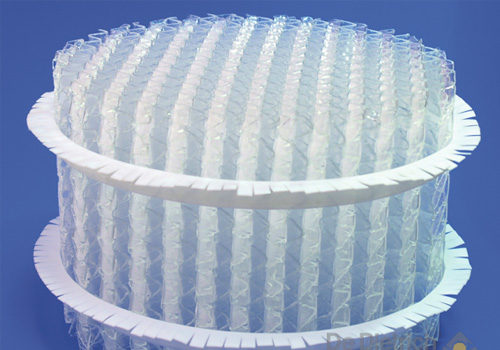
STRUCTURED PACKING DURAPACK®
-
- made of borosilicate glass 3.3
- highly corrosion resistant
- high separation efficiency-
- low pressure drop
The efficient solution for highly corrosive thermal separation processes
CONCEPTThermal separation processes are often used in treating and cleaning chemicals. Very common are processes that involve two liquids or a liquid and a gas. The processes used mainly involve extraction, absorption, desorption or stripping, distillation or rectification. These separation processes require mass transfer between two phases; in the above rectification example, the mass transfer between the liquid and gas phase. Keeping the equipment used in this process as compact as possible requires creating as much mass transfer surface in as small a volume as possible. DURAPACK® ensures high flow rates with low pressure drop and at the same time huge mass transfer areas for an efficient separation.
In order to intensify the mass transfer in absorption, desorption, distillation and extraction columns structured packing DURAPACK® from borosilicate glass 3.3 is the best choice for corrosive media. Applications are among other are therefore corrosive chemicals such as sulfuric acid, nitric acid, other mineral acids such as HCl but also halides such as chlorine, bromine and iodine: short wherever metal material but also plastic fail.
DURAPACK® patented structured packing consists of alternately allocated corrugated plates made of borosilicate glass 3.3 with channels at an angle of 45°. In order to increase the turbulence the corrugations are notched. The packing is only made from borosilicate glass 3.3, i.e. the plates are sintered together without any gluing material so that only borosilicate glass 3.3 is in contact with the media to be processed.
The easy-to-clean smooth and inert surface is extremely convenient.