Videos
Loading the player ...
- Offer Profile
- 米imatic Tool System products are utilised between the machine spindle and the workpiece. Cutting tools, driven toolholders, angle heads as well as precision drill chucks are important elements of our range of products.
Cutting tools cover circular milling of slots and grooves, circular thread milling with multiple inserts or a single insert, solid carbide thread millers as well as reaming with system tools (shank plus carbide metal head).
Product Portfolio
Complete Solutions
-
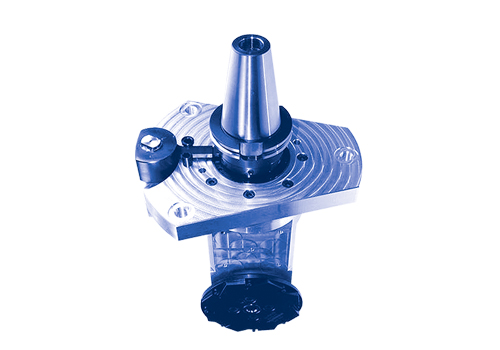
Component Part Specific Complete Solutions
-
- of driven tool holder and cutting edge
Ask us – we gladly accept the challenge and develop together with you a solution in the areas of:
- Multi spindle solutions
- Saw blade holders
- Fixed angle
- Plunge milling in cavities of larger components
- Complete solutions with cutting tools
-
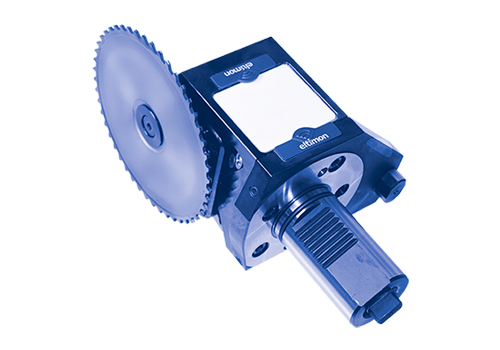
米imaticDTF
-
- Turn Cut Milling instead of parting off:
Faster parting off than anybody else!
Turn Cut Milling with PolySAW
- Short process times
- Process reliability
- Material saving
- Surface quality
- Absence of burrs
- Short chips
-
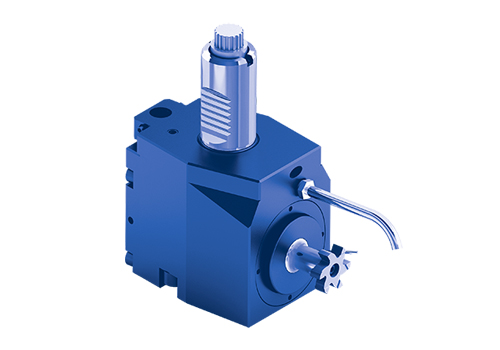
agMILL
-
- Compact Driven Toolholders with Interface for Carbide Inserts
Thanks to mimatic‘s cross-system expertise in the fields of driven tool holders and precision carbide steel cutting tools, mimatic has developed a compact new cutting solution.
The interfaces and holders that are usually located between the powered tool and circular milling insert are eliminated. Directly on the main shaft of the powered tool there is now the polygonal insert fixture for the cutting of threads, grooves and cut-ins.
-
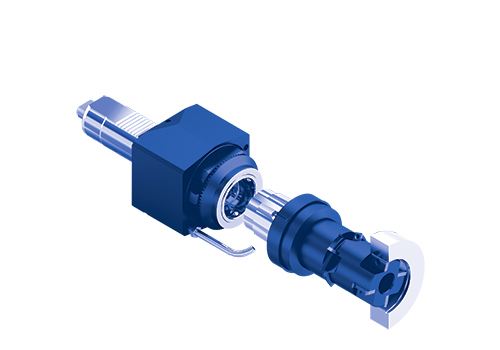
米imaticMi
-
- The Integrated Tool Solution
For more efficient machining on turning machines, mimatic applies its expertise in integrated and complex cuttting tools and its expertise in driven tool holders. The result is a cross-system tool solution for series production.
The central part of this solution is the modular quick-change interface mi, which connects the driven tool holder directly and without additional work to e.g. shell-type milling tools for combined machining (turning, planing, chamfering).
Cutting Tools
-
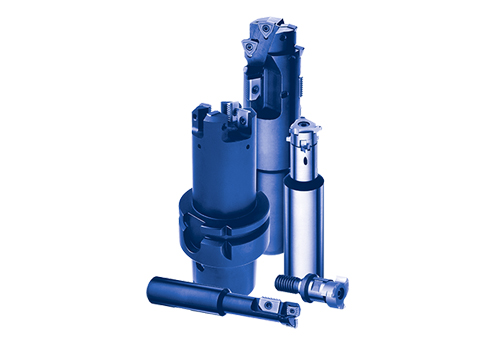
Special- and Combination Tools
-
- Do you have a special application or a production problem?
Ask us – we gladly accept the challenge and develop together with you a solution in the areas of:
- Milling
- Thread Milling
- Slots
- Chamfering
- Facing
- Grooving
-
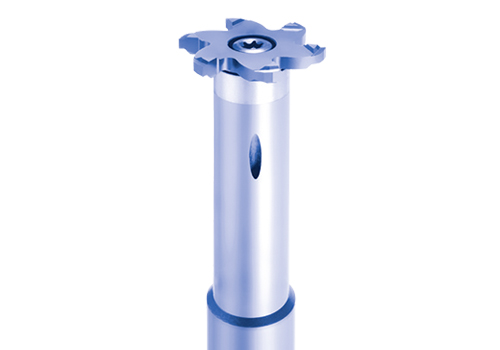
PolyMILL
-
- The affordable system with high performanceallowsthreadingand / orcirclipgroovingin high precision. The polygonal connection of insert and milling body improves the efficiency and precision of the process significantly:
- Longer tool life
- Higher machining volume
- Higher feed rates
- Shorter processing times
- High stability
- High security at interrupted cutting
-
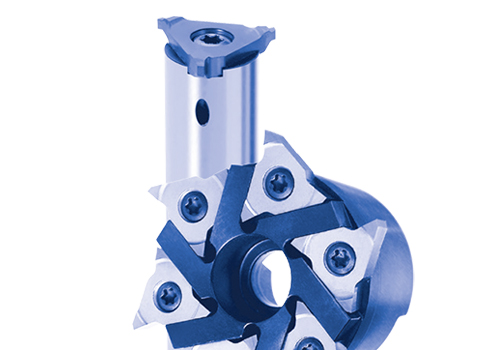
TriMILL
-
- Affordable and flexible system处理时间短、长时间的工具lifes.
- Deep, true to gauge threads
- Accurate free-form contours
- Accurate grooving
Bottom threads can be cut almost to the bottom without undercuts. By using the same pitches, the storage and acquisition costs decrease also.
-
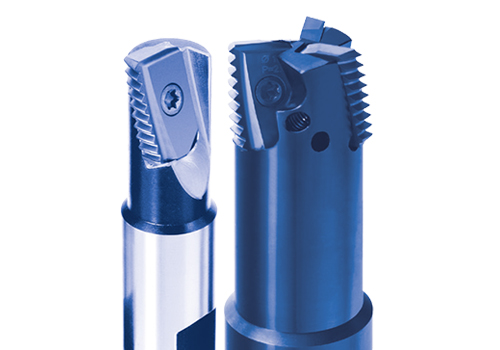
TrioCUT
-
- Smooth cutting and low cutting pressureresults in high surface quality and long tool lifes. Aconicalposition of insert pocket guarantees stability of the tool shaft. Further advantages are aradiallybackgroundthreadprofile, extremely high wedge angle, a more stable cutting edge as well as a positive rake angle. The optimum application area are fine threads and/or very short thread lengths.
- Thread milling
- Thread milling with undercut
- Drill milling
-
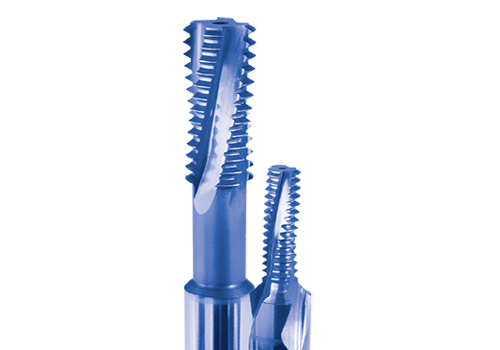
SolidCUT
-
- Extensive range of solid carbide thread milling cutters.
- Spiral-grooved grooves
- Soft cut
- Excellent surface qualities
- Also for thin-walled workpieces
- A tool for right- and left-hand threads
-
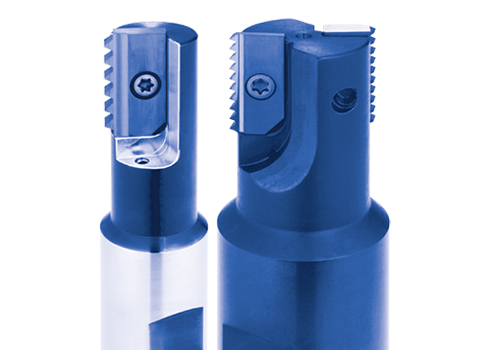
14,5 15 21 26
-
- Multi tooth thread milling cutters, ideal for short thread lengths and very rigid clamping of workpiece and cutter.
-
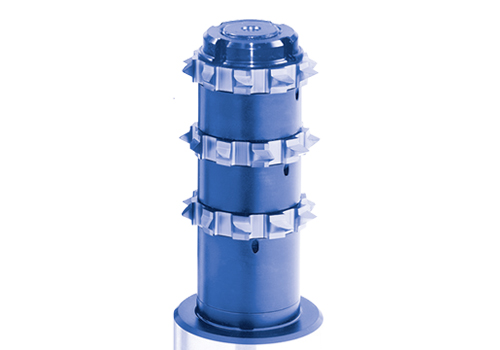
米imaticSTC
-
- Sectional thread milling for high-quality large threads from M24.
STC-1 with 10 edges
Biggest advantage for any long threads from M24: A shorter process time compared to cutters with inserts and easier assembly.
STC-2 and STC-3
Depending on the thread length (pitch, material) much faster than STC-1.
-
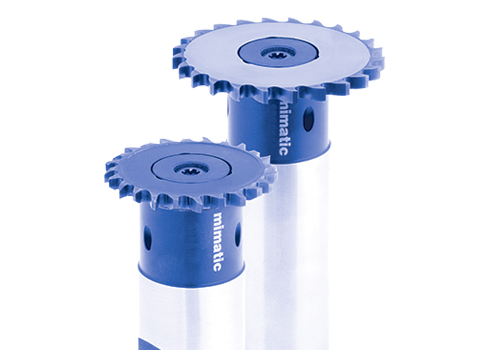
DeepMILL
-
- Slot milling, grooving, milling of cooling fins
with a up to tenfold cutting performance!
- Larger range of applications
- Defined tooth and cutting edge geometry
- 米imatic core competence:
- Polygon interface Quadrogon interface
- High performance coatings
- Internal coolant direct to the edges
- Clamping with only one center screw
- Special chip space geometry
- With DeepMILL can be milled up to shoulders
- Cutting edges on the face can be used for special machining operations
- On request: Increased cutting depths (S) achievable with reductions in speed/feed
- Re-sharpen-Service 2x
- Minimum distance for operations to shoulders: 0,001 mm
-
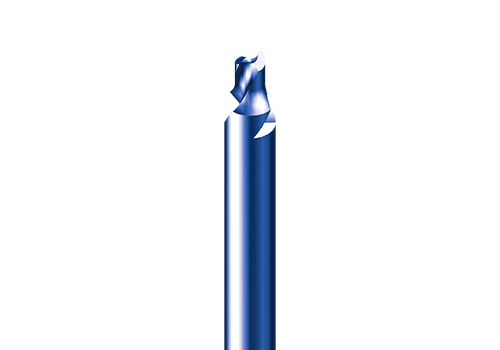
Keyway Slot Milling Cutters
-
-
- CNC-Turning Machines with Y-Axis
- Increased stiffness, higher precision
- CNC-Turning Machines without Y-Axis
- Optimized straight run-out
- Short Process Times
-
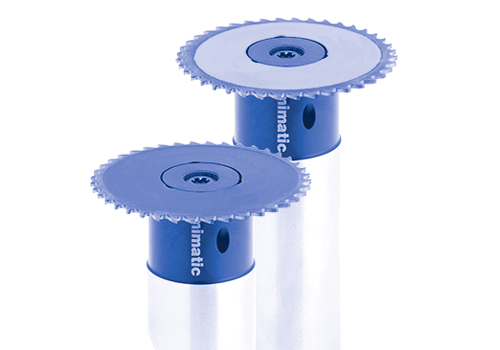
PolySAW
-
- Cutting, Sawing, Slitting
with a up to tenfold cutting performance compared to conventional carbide circular saws!
- Larger range of applications
- Defined tooth and cutting edge geometry
- 米imatic core competence: Polygon interface Quadrogon interface
- High performance coatings
- Internal coolant direct to the edges
- Clamping with only one center screw
- Special chip space geometry
- With PolySAW-G profiles can be machined up to the shoulder
- On request: Increased sawing depths (S) achievable with reductions in speed/feed
- Re-sharpen-Service 2x
- Minimum distance for operations to shoulders: 0.001 mm
-
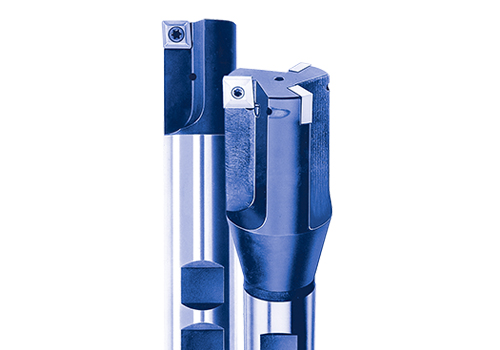
CT Tools
-
- Counterbores and Countersinks
- Fixed dimension countersinks are suitable for counterboring of pre-drilled or casted holes
- Counterbores are suitable for producing cuts for cylinder head bolts, ejector pins, on cuts, sealing surfaces
- Internal coolant
- Narrow tolerances ± 0,05 mm
- Long lifetimes
-
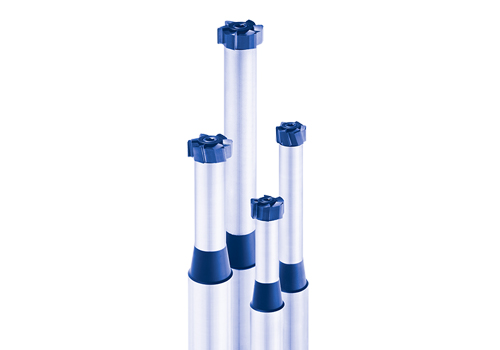
PolyREAM
-
- RPK-Reamers with Polygonal Insert Seat for High Chip Removal
A new generation of Reamers to machine blind and through holes in components with greater accuracy. The polygonal connection between the insert and the shank provides improved strength allowing greater cutting forces which in turn makes for economical machining.
Two basic types RPK 40 and RPK 42 are available, which cover a wide range of applications by their different shanks and cutting insert designs. Changing the insert is quick and easy. The front clamping screw absorbs none of the cutting forces and is merely there to hold the insert in place. Different overall lengths are available.
- High-tensile connection by polygonal insert seat
- Easy insert change
- Internal coolant supply directly to the cutting edge
- High concentricity
- Longer durabilities
- High precision
- Higher volume of metal removed by reaming
- Higher feeds
- Shorter processing times
- Special dimensions available
-
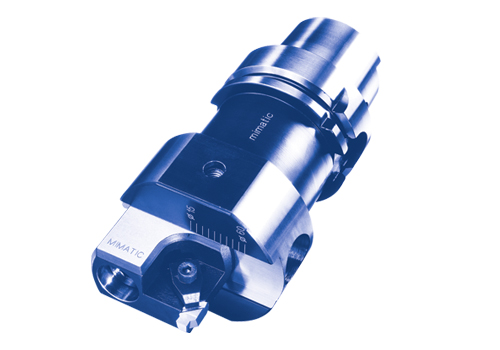
Axial Cutting Tool
-
- with scalable cutting diameter and fine-adjustment
This tool makes operations possible in workpieces, which cannot be clamped on turning machines.
Making grooves (DIN- or special grooves) up to a
- Cutting depth of max. 4 mm
- Cutting width of max. 6 mm
Driven Toolholders
-
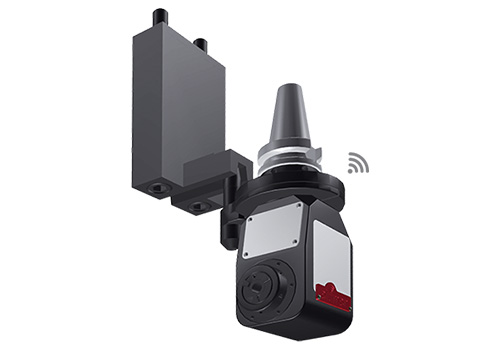
Angle Head BT30with eltimon– Industry 4.0 (IIoT) Ready!
-
- Angle Head 90° BT30 Ultra Light – eltimon® integrated for FANUC machining centers
-
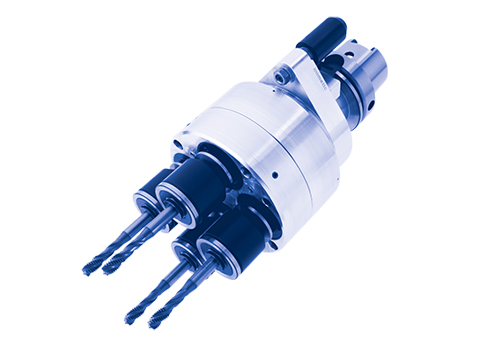
Multi Spindle Technology
-
- 米imatic® Multi Spindle Technology Increases Your Productivity
The multi spindle technology is characterized by the rule that almost no working issue resembles the other one. Our strength lies in our ability to prepare individual solutions for each of these cases.
The fixed multi spindle units are usable for drilling, thread cutting, countersinking, reaming and for multi spindle milling. Many tool interfaces such as mimatic® mi, HSK, collets, etc. are possible.
Our customers are mainly the automotive industry and machine tool manufacturers (HSC milling machines-, CNC machining centers-, special- and transfer machine manufacturer).
-
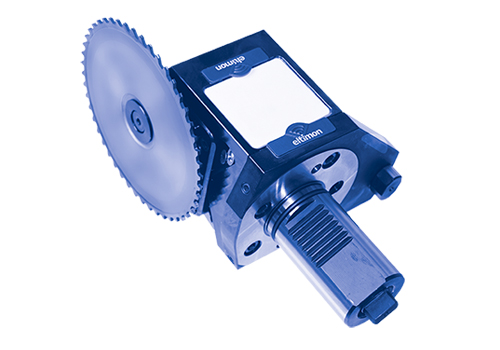
eltimon Tool Monitoring
-
- eltimon (electronic live tool integrated monitoring)
for digitization of live tools, angle heads in machining centers and driven tools in CNC lathes
- Visualization using eltimon-app on your mobile phone
- Data storage in the eltimon-core in the live tool
- Synchronization through eltimon-cloud
- Real time analyses, trends and status
- Augmented operator, decision-support, reminders
- Maximum lifetime for your live tools
Live Tools
-
-
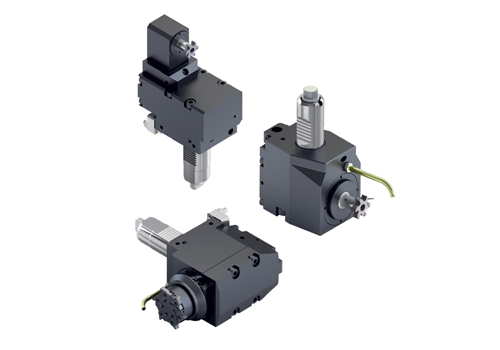
Design
-
- Our boring and milling units are suitable for most of the popular turning machines and lathe equipment manufacturers. We produce the following types:
- Straight and offset units
- Internal and/or external coolant supply
- Gear multiplication or reduction
- Single or multi-spindle versions
- Angle heads for the production of angled holes, by means of adjustable and fixed angles
- Sawblade holders for sawing or slotting of workpieces
- Every popular type of tool system can be supplied
-
Performance Values of Driven Tool Holders
-
- The torques Mmax specified in the tables below refer to shock-free processing (e.g. threaded cutting). For processes involving major shock loads (e.g. milling or multi-edge knocking), a value reduction of up to 50% and more needs to be taken into account. The values nmax and Pmax rendered are guideline values for short-time operation.
The permissible relative operating duration depends
- on the version of the spindle unit (with or without gear)
- on the presence of a cooling system and the type of cooling (external or internal through the tool spindle
- on the processing torque
在收取约60%的最大值working life calculated amounts to approx. 2.000 hours Spindle units with gears produce more noise at higher speeds!
Angle Heads Monoblock
-
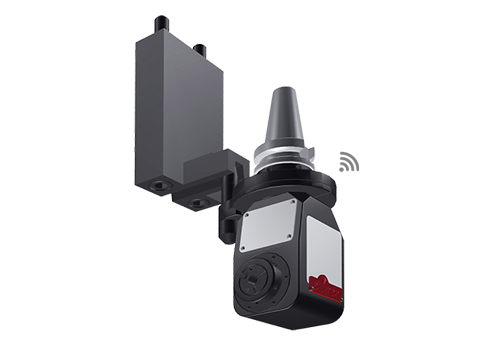
Angle Head BT30 with eltimon – Industry 4.0 (IIoT) Ready!
-
- Angle Head 90° BT30 Ultra Light – eltimon® integrated for FANUC machining centers
-
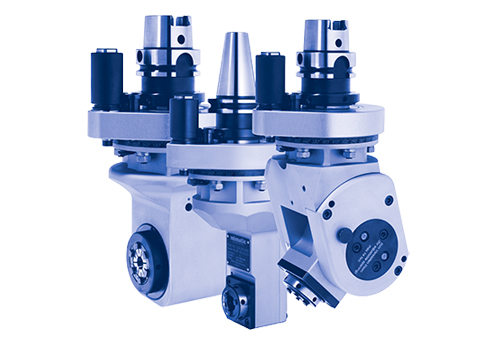
Monoblock Angle Heads
-
- Our program of monblock angle head tools provides our customers with the means for complete, integrated machining. It is now no longer necessary to repeatedly relocate tools, which means a considerable reduction in production costs, rationalization and the increase in flexibility over the entire production process.
-
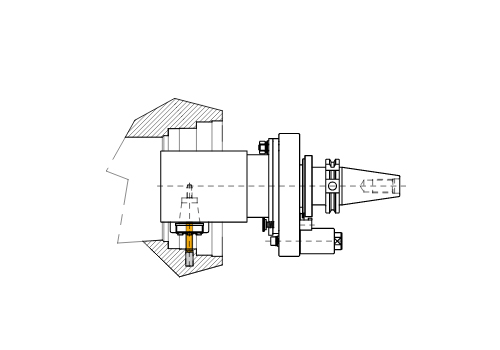
Features of the mimatic® Angle Heads
-
- 米imatic® angle heads increase the efficiency of your production. They allow you to work on inaccessible areas within housings or bores.
The angle heads can be used in all popular machine concepts, such as CNC machining centers with automatic or manual tool change and specialpurpose machines with fixed insert. They are optimally designed for the respective machining task.
We use ground bevel gears with helical profile as well as hardened and ground spur gears to ensure smooth operation and high power transmission.
-
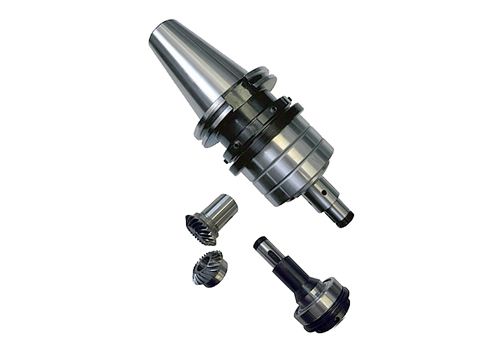
Design of the Angle Heads
-
-
- Output orientation is fully adjustable(0-360° via the 6 setscrews on the adjusting ring)
- Angle head can be rotated through 360° and is infinitely variable- additional 6 x 15° indexations for adjustable angle units
- Highspeeds up to 15,000 rpmandhigh torquesup to 150 Nm
- Thetorque support is designed according to ISO 9524 as standardausgeführt. This can be adapted by the customer.
- Differentstandard stop blockversions are available. If necessary, these are to be adapted and fitted to the machine tool by the customer.
-
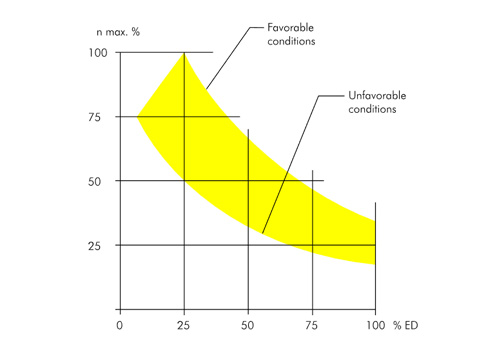
Performance Values of Angle Heads
-
- The torques Mmax specified in the tables below refer to shock-free processing (e.g. threaded cutting). For processes involving major shock loads (e.g. milling or multi-edge knocking), a value reduction of up to 50% and more needs to be taken into account. The values nmax and Pmax rendered are guideline values for short-time operation.
The permissible relative operating duration depends
- on the version of the spindle unit (with or without gear)
- on the presence of a cooling system and the type of cooling (external or internal through the tool spindle
- on the processing torque
在收取约60%的最大值working life calculated amounts to approx. 2.000 hours Spindle units with gears produce more noise at higher speeds!
Modular Tool Systems
-
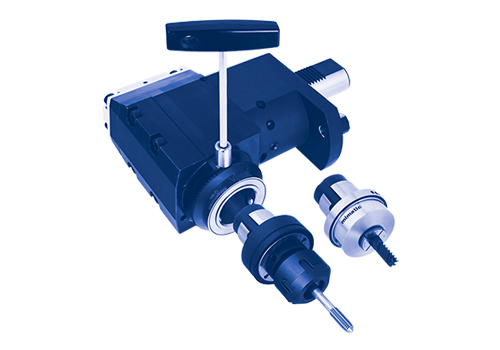
米imaticMi
-
- Modular Quick Change System
- Universal tool clamping system for all production areas
- Presetting of the tools off-line by length adjustment screw
- Tool change within seconds
- Concentricity of the interface < 0.002 mm
- Secure holding force by form-locking
- Very short design
- Toolholders in different sizes
- All toolholders with internal coolant
-
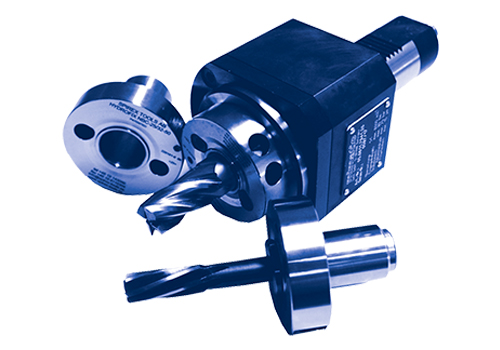
HydroFLEX
-
- 振动减少工具夹紧系统
for all applications (reaming, drilling, milling)
- For use in our mimatic® driven tool units
- Concentricity < 0,002 mm
- Holding forces up to 290 Nm
Clamping Technology
-
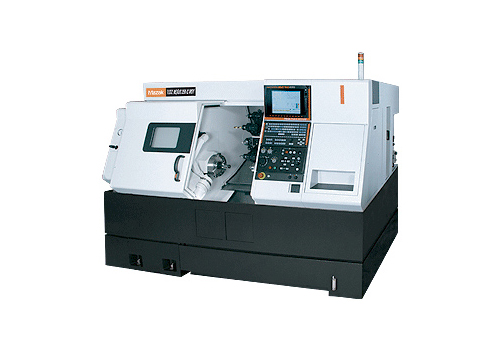
Static Toolholders
-
-
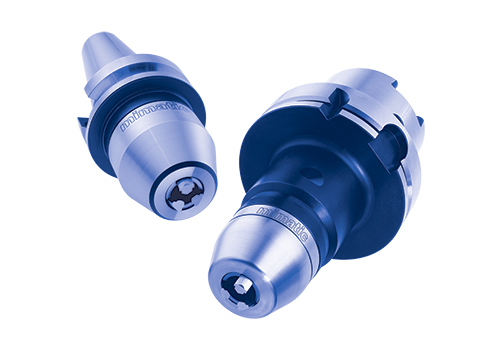
Precision Chucks
-
- Precision
米imatic® Universal Chucks guarantee maximum concentricity, reliability and tool life.
Force
Because of the particularly high clamping forces, mimatic® Universal Chucks securely lock tool in the chuck.
Flexibility
米imatic® Universal Chucks can be used flexibly for drilling, reaming, countersinking and milling.
-
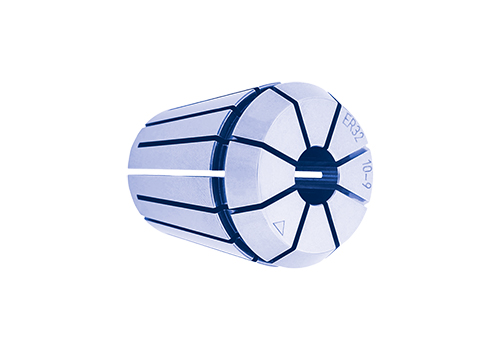
Accessories for Toolholders
-
-
- Collets
- Tap collets
- Seal discs
- Sleeves
- Reducing sleeves
- Wrenches