Videos
Loading the player ...
- 提供个人资料
- plasmo Industrietechnik GmbH is the market leader in the field of quality assurance solutions for automated metalworking production. We are an innovative company that is absolutely specialized in the area of quality assurance.
While our headquarters are based in Vienna, we maintain a worldwide network of plasmo branches and partners.
我们的客户从质量保证领域的我们的解决方案中收到,使他们能够实施安全,高效和成本优化的生产。
Product Portfolio
Applications
- Produce Quality. Always.
我们发现质量保证自动化解决方案metalworking production processes. Our solutions are independent from the plant or laser manufacturer. This is important because our customers wish to obtain the best solution for their own application.
汽车
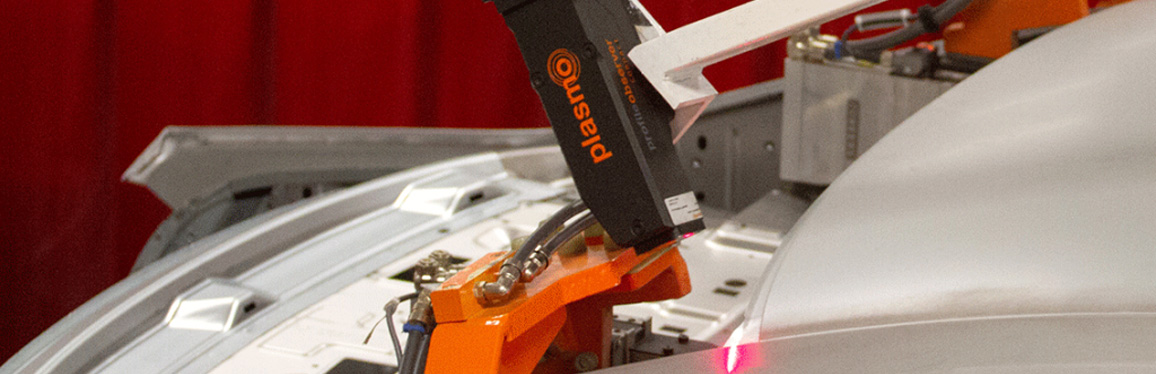
- SEAM INSPECTION FOR LASER BRAZING
At a glance
Seam Inspection for safety-relevant components, e.g. on roof seams, rear trunk lids and water channels of vehicles
Challenge
Automated welding and soldering is essential within industrial production for countless industries. Guaranteeing perfect quality through testing of high volume weld seams and an increasing number of variants require 100% error-free processes. Especially for brazed seams by robots, as there are for too few trained employees available for the visual inspection. Also, the requirements are particularly high when the “just-in-time monitoring systems” have to check the seam sections with traces of powder or smoke.
plasmo’s solution
Quality inspection plays a key role for repeatable and reliable product quality for metalworking manufacturing. To monitor and optimize laser brazing or laser welding seams, the plasmo profileobserver offers the perfect solution. The system recognizes, captures, analyzes and documents the seams as well as geometry and surface. Depending on the manufacturer, fault types and individual tolerances are defined according to internal and external standards. If the profile reading exceeds the specified tolerances, the profileobserver signals that the corresponding assembly (soldered seam) must go to the rework station and the error is displayed directly on the screen.
- Immediate result = no lost time or wasted cost
- 无损
- Efficient
- Unproblematic integration into serial processes
- Features for additional evaluations
- 使用方便
- Flexibility
- Low-maintenance
Result – seam inspection
Through the use of an optical seam inspection system, it is possible to detect existing defects in the seam quickly to minimize cost and optimize the production process. This ensures that only parts with perfect quality are in the downstream production process. Also, all results are documented and stored for the further development and optimization of the soldering process while ensuring guaranteed quality assurance at all times.
-
Tubes and pipes
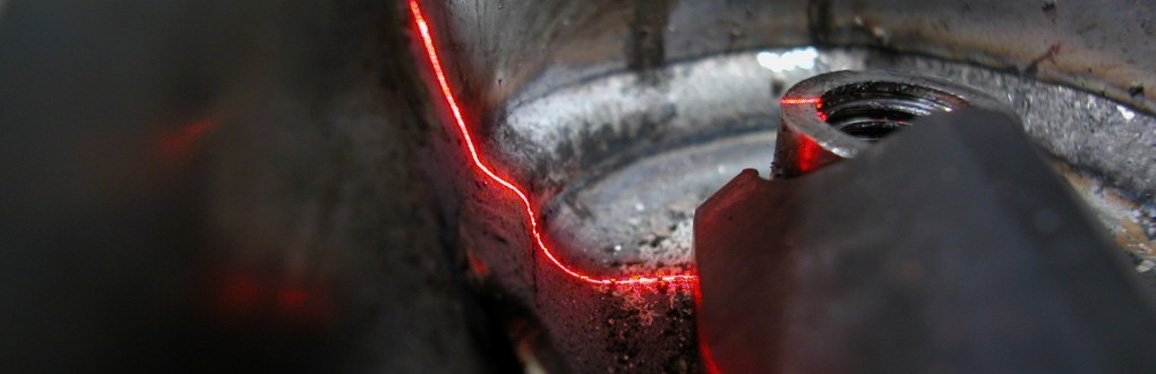
- QUALITY ASSURANCE FOR PIPES AND PROFILES
At a glance
Quality assurance for standard and endless pipes, tailored tubes and profiles requires innovative solutions. These can dramatically reduce manufacturing costs and rejects. Everyone knows the negative impact resulting from component failure – expensive production loss, extended downtimes, long inspection intervals or even safety risks are only some examples. In this context, process-monitoring systems can produce technologically relevant highlights.
Challenge
Continuously increasing requirements for quality and economic efficiency challenge customers to optimize products and production processes on an ongoing basis. In view of high productivity and the precision as a tool, these extremely fast processes are becoming constantly more significant in modern manufacturing technology. The implementation of high-tech systems for quality assurance in the production process can result in dramatic savings in weight and costs for simultaneously higher quality standards.
Our customers, for instance in the automotive sector, are among the major innovation drivers and an important sales market for pipes and profile manufacturers. Every vehicle includes many meters of (endless) pipe or pipe-like profiles (tailored tubes), even though invisible. The specifications defined by the EU for a reduction of CO2 emissions have resulted in significant additional challenges for manufacturers and suppliers.
plasmo’s solution
During the welding of pipes and endless profiles, the aspects of ease of welding must additionally be considered. Many issues are relevant, from the design of complex profiles and suitable materials through to the ease of the manufacture. Practical quality assurance is particularly important in this context. In many pipe/profile systems, the weld is no longer visible and any control must be performed inline. In addition, it is crucial that any defects are identified immediately so that the cause can be remedied as quickly as possible. As a result, rejects can be reduced significantly.
的plasmotest sequences are as follows:
- Process visualization: Identifying the potential for production increase and statistical analysis of the processes. In addition, improvement of the process understanding by system operators as well as detection of systematic errors.
- 通过OK/NOK决策进行故障检测:这涉及故障的定义,在过程中或之后直接消除有缺陷的部分。目标是对整个焊缝进行100%无疲劳和客观控制。
- Accurate meter-by-meter traceability: Continuous control of interrelations of multiple productions steps ensures subsequent analysis and definition of critical sections.
Selection of the testing equipment
Sensor- and camera-based test procedures as well as ultrasound offer solutions for a wide range of technological challenges for processing speeds of up to 80 -120 m/min, in- and online. From the visualization of the processes and fault detection through to the traceability of components and production steps. Modern online systems are used to ensure early detection of cracks, damage, edge offset, pores or pressure of rollers, etc., that might be produced during the welding process.
Result – quality control
焊接过程中产生的裂纹和损坏是通过在线监控系统提早检测到的,并通过在无限过程中的轮廓或管道上的时间延迟的标记系统确定。特别是在不锈钢管道的情况下,在某些情况下,这些在线系统可能会降低涡流或放射线检查的程度,在某些情况下是法律要求的,因为可以事先完成返工。
An online monitoring system detects cracks and damage from the welding process at an early stage and is characterized by a time-delayed marking system on the profile or pipe during continuous processes. Due to these online systems, the partly legally prescribed tests with eddy current or x-ray can be reduced, especially for stainless steel tubes, since a post-processing can take place first.
-
添加剂制造
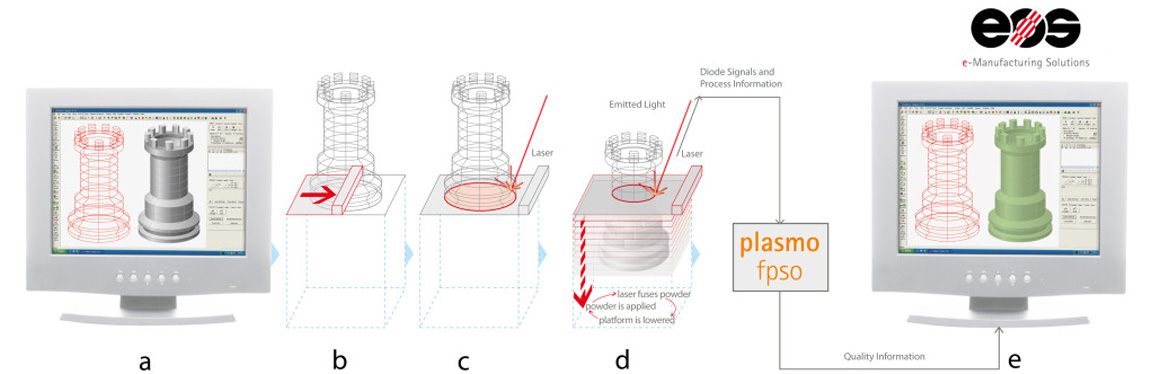
- 添加剂制造
At a glance
Engineers have always aspired to design parts without having to take the restrictions of conventional manufacturing methods into account. 3D printing using metals offers new possibilities with high geometric freedom. Even though the market for this manufacturing technology is currently relatively small, this technology is predicted to offer great future potential. Sales of 3D printing systems, the service of these and the respectively required materials are expected to quadruple to € 6.8 billion in the next 10 years.
Challenge
For optimal utilization of the manufacturing process even in safety-critical applications, such as, for example, in medical technology or in astronautics, essential requirements must be fulfilled. These include an understanding of the manufacturing process, the knowledge of the achievable, directional mechanical-technological properties as well as the use of appropriate quality assurance systems. The 3D printing systems for metals currently available in the market are exclusively controlled, resulting in an increasing demand for controlled systems in the industry.
作为PAM项目的一部分,开发了针对注射成型应用的原位过程监测,除其他外,这是一个制造过程,该过程通过水平或垂直连接的体积元素(主要是分层)生产组件。3D打印过程是开发产品的最短方法,从想法到市场成熟。该过程允许即使是最复杂的几何形状,也可以无问题的生产。传统的制造方法(例如转弯或铣削)迅速达到了极限。结果,设计几乎没有更多的限制,这要归功于几何自由是他的过程必须提供的最重要的优势之一。
The basis for making components from powdered metal are 3D CAD data that are used for generating the physical layers. Following application of a new powdered layer, the metal particles are solidified by application of energy in the form of laser radiation, which produces a locally restricted weld pool.
As presently only controlled systems are available and it is presently not possible to detect the above-described fusion defects in the construction process, the industry has a growing demand for controlled systems. The area of use of metal 3D printing is restricted due to the lack of quality assurance in many industries. Based on the detected fusion defects, a fault pattern could be defined for the quality assurance system to be developed. One approach towards implementing this process monitoring consists in the use of a photodiode-based measuring system that detects the process light produced when melting on the powdered metal. The thus determined measured values together with additional machine parameters represent the basis for monitoring the welding process.
Solution
与工艺监测系统实施有关的所有工作均在制造商EOS的eosint M 280金属零件的激光烧结系统上进行。能量的应用由200 W ytterbium纤维激光器具有1064 nm波长。该系统的整体安装尺寸为250×250×325毫米。
The photodiode-based plasmo fastprocessobserver measuring system is implemented at two different measuring positions. One of the measuring positions is located within the process chamber while the second one is situated outside on the camera adapter of the scanning optic. In the process chamber, the reflected light is captured by four fiber optic cables of a quadruple fiber oriented towards the construction platform. At the camera adapter, the reflections are detected directly in the laser beam path, also by fiber optic cables. The fiber optic cables of both measuring positions ultimately lead to the measuring system comprising the plasmo fastprocessobserver, which converts the optical signals of the fiber optic cables via photodiodes into corresponding electrical signals. These are then recorded via high-speed modules of a data acquisition system. Aside from the process light, this data acquisition system also records other machine data, such as for example the scanner position. One measured data file is produced for each layer and is used as the basis for evaluations.
The recorded process data is evaluated using specifically developed algorithms that include statistical evaluations for every layer. These comprise, for instance, mean value and standard deviation of the reflected radiation, relative distribution of the voltage readings of the process light for a division into voltage ranges, current welding angle, etc.
A CT scan of the samples was produced to assign the recorded process data to the produced component. This shows a significant increase in the number of inclusions in layers exposed to reduced laser output. Based on the evaluation algorithms, in particular the algorithm used for allocating the recorded process light to the corresponding scanner position, this inclusion should then be recovered in the logged process data.
Result
The following procedure was applied to find the imperfections, which were present according to the CT scan, in the recorded process data: As it was not known beforehand what made up the inclusion in the recorded process light at the two measuring positions, the area where the fault could be found had to be restricted first. Owing to the high resolution of the CT scan, the area could be restricted to a few layers having a thickness of 0.03 mm in the direction of the design height. According to the CT scan, the inclusion to be found extended over 6 layers. By investigating the time sequences of the recorded process light, it was eventually possible to detect the air inclusion in 5 layers.
Once the fault had also been identified in the process data, the measured scanner position was used to allocate the time signals locally – referred to as localization – so as to determine its recorded position on the construction platform. This could successfully be done through appropriate parametrization of the algorithm.
-
Customized solutions
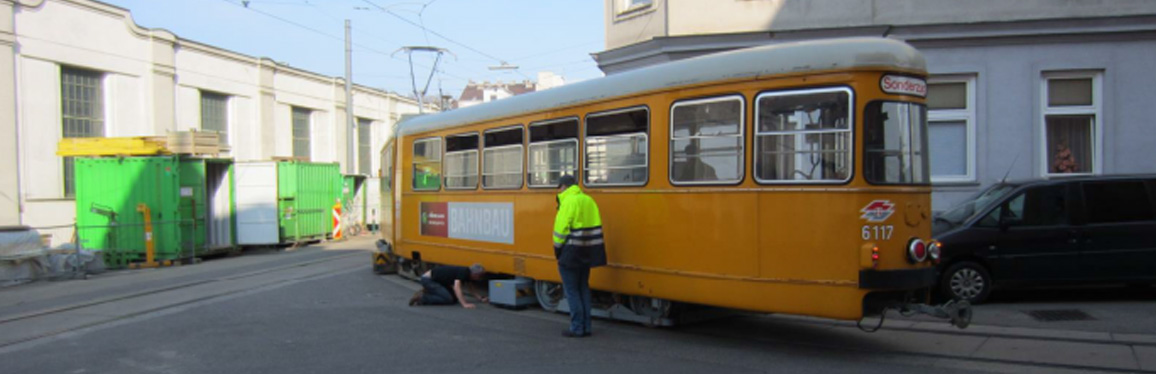
- RAIL MEASUREMENTS
At a glance
Plasmo Railobserver是由各种项目合作伙伴开发的,这是研究合作项目“ Plasmatram”的一部分。定义的任务是以前所未有的准确性来测量维也纳电车道的整个铁路网络,以尽早发现任何磨损或有缺陷的斑点,这些磨损或有缺陷的斑点会给轨道带来高压力,并一次又一次地导致轨道交通中断。
Thanks to a very fast camera technology, the geometry of the rail can be measured with the highest accuracy at a driving speed of 60 km/h.
Challenge
控制任何轨道损坏都需要绝对精确,重复准确性和稳定性。开发了测量系统所需的测量和评估软件。在此过程中必须满足几个标准。
一方面,必须确保在测量旅行期间在监视器上显示的实时值驾驶的工作人员在测量过程中能够立即检测到轨道上的任何重大缺陷。
此任务需要处理大数据量和实时计算必要的测量变量。此外,这些数据数量必须实时显示和保存,以促进随后的维护数据库中的存档和可用性以进行进一步分析。
Solution
的plasmorailobserver was integrated into the measuring vehicle of Wiener Linien. It was thus possible to test the measuring system repeatedly in the urban environment under real-world conditions and to adapt the thus derived findings and general conditions to achieve the best possible measurement results. A special bracket had to be developed and manufactured for optimal integration of the measuring system in the measuring vehicle. In addition, the entire wiring was integrated and a separate measuring station for the system was created. In order to achieve the required high accuracies, the prototype used lasers operating at a high light energy.
此外,开发了一种特殊的压缩算法,该算法实时压缩了数据,并且在其原始大小的十分之一中不损失约90%,即使在数百千兆字节的范围内也可以有效访问单个配置文件。
To ensure that the plasmo railobserver met the requirements in the road network, the optical system was designed to withstand the dynamic challenges. In addition, special calibration elements were developed with the goal of achieving an absolute calibration of the measuring system and, in subsequent continuous operation, to provide the operator with the option to check the necessity for re-calibration at periodic intervals. Furthermore, an accurate optical measurement was required to measure and to compare the two rail tracks on an absolute basis. The thus derived measured variables (e.g. track width) were crucial. Thanks to the high resolution of the system, it was discovered in the course of the project that elements left and right of the rail could also be recorded and measured.
Result
该系统将在未来提供更大的好处。特别是,该原型现在允许可靠的检测和测量导轨结构,例如开关,开关舌,交叉等。作为下一步,将来对这些元素的连续监视将以前所未有的精度自动化。目的是利用该项目中获得的发现来为自动维护时间表做出贡献,并考虑有关地铁区潜在用途的后续开发步骤。长期目标是为能够在国际层面覆盖各种铁路类型的城市地区建立铁路监测系统。(例如,凹槽和平底轨)。
-
工艺链
- Production line integrated testing systems from plasmo guarantee the currently highest possible quality in industrial production in real time. While camera-based systems are predominantly used in the pre- and post-weld sectors, diode-based solutions have become the standard for inline tests.
-
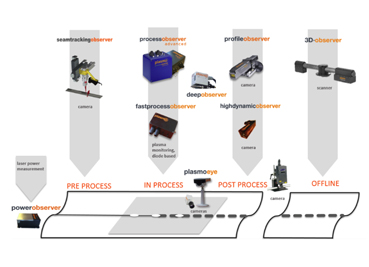
加入流程的质量保证产品
-
- 来自Plasmo的生产线集成测试系统可确保实时的工业生产最高质量。虽然基于摄像头的系统主要用于焊接扇区和后扇区,但基于二极管的解决方案已成为内联测试的标准。
-
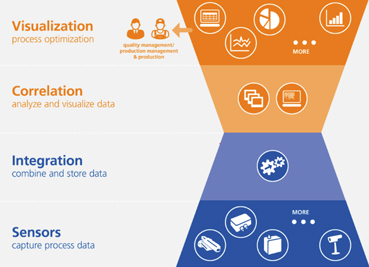
plasmo Quality Suite
-
- We work on the individual problems of our customers and find solutions. The plasmo Quality Suite comprises 3 levels.
-
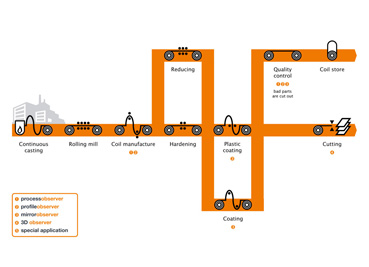
Coil manufacture process chains
-
- The visual presentation shows the process of chain of coil manufacture and processing. From the delivery via diverse production steps through to the finished products. Example of the application of plasmo solutions are also listed.
-
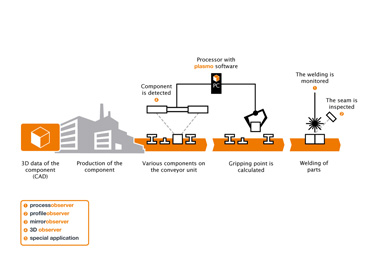
Automated component handling
-
- This graph illustrates the process chain in automated production on the example of the manufacture of a steel girder used for bridge construction. Based on the 3D CAD data of the respective, freely selectable component, the position of these is detected on the conveyor of units following production (plasmo solution: 3Dobserver). Testing of the subsequent welding process can be done either during welding (plasmo solution: processobserver series) or after completed process (plasmo solution: profileobserver series)
-
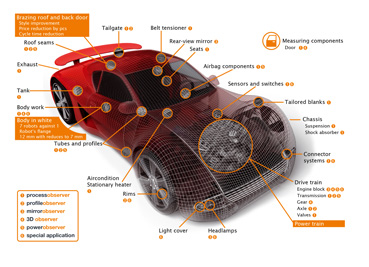
汽车
-
- 您可以在此处找到我们的解决方案和您可能应用的应用程序的概述。指示的数字是指可用于相应应用或解决方案的等离子体产品。
PRODUCE QUALITY. ALWAYS.

- Depending on the material and product specification we use for testing the joints different technologies. Metals, mixed compounds and plastic parts are welded or glued, assembled and mounted. Metal parts are soldered, screwed, welded or pressed into the plastic compound. The respective testing method depends on the product and the request.
-
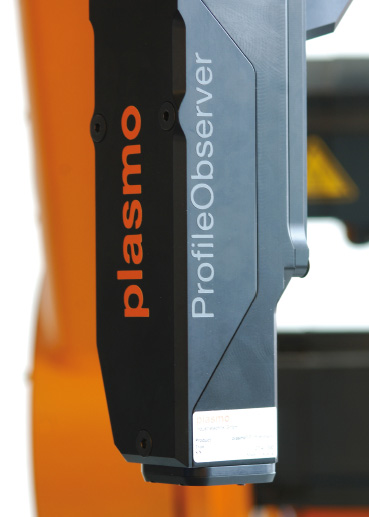
profileobserver compact
-
- 的plasmoprofileobserver product family stands for highest precision in the fast and reliable detection of surface defects such as seam elevation, edge notches, cracks, splashes, seam width, seam position pores and other geometric forms.
特点与优势
- 非接触和非破坏性(NDA)
- 高速视觉系统(最多30,000张图像/s)
- Precise measuring results with high dynamics
- Almost independent of the surface
- Reduction of the production costs through early detection of defects.
- Reliable detection of the surface defects:
- Seam elevation/dips
- Edge notches
- Cracks
- 飞溅
- Seam width
- Seam position
- Pores
- Changes in laserpower
- 焊接速度的变化
- 统计模块和趋势分析模块
- Subsequent traceability up to the seam
- Seamtracking
-
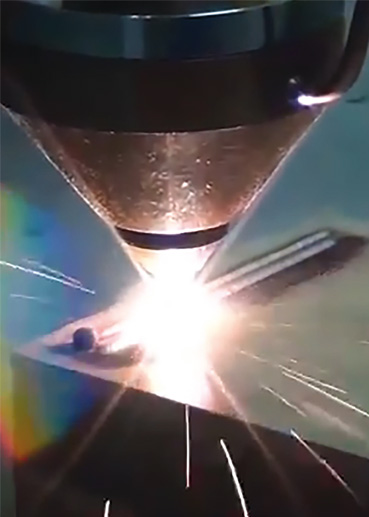
FastProcessobserver
-
- Fast Quality Inspection
- Extremly fast: Quality inspection for very fast laser processes
- High adaptablility: Customized software development
- 新范围的QS:激光切割,添加剂制造,激光清洁,脉冲激光焊接,粉末涂料,覆层,…
- Improved production by self-learning process
-
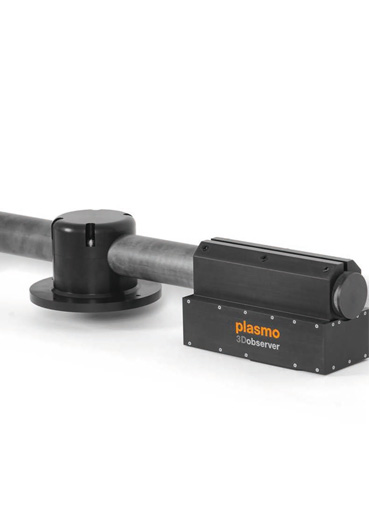
3D observer
-
- The 3D observer is an optical sensor system capable of fully identifying, capturing and measuring three-dimensional objects and their location in a space (in relative or absolute coordinates). It then supplies these data to a robot or linear axis system, for example, as commonly employed in many automated production processes. The 3D observer provides information regarding the location, the 3D contour or gripping point of objects in the production chain. It is also capable of solving tasks which require the simultaneous use of both 3D and 2D optical technology. The process is flexible, extremly quick and does not depend on the material or the colour and is almost independent from the surface. Thanks to the high processing speed, this unique 3D scanning process allows 100% control of the production process.
-
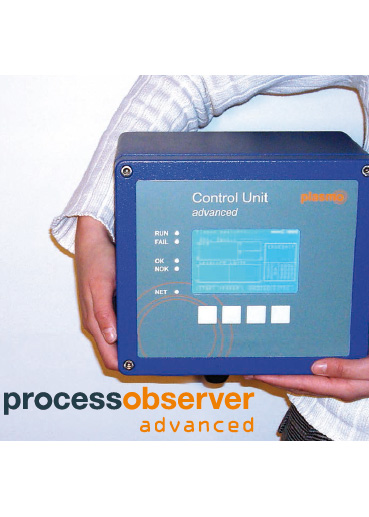
processobserver advanced
-
- 的plasmoprocessobserver advanced offers you a hi-tech device that monitors and documents welding, cutting and drilling processes in real-time without damaging the workpiece. All data recorded is available for a detailed offline analysis.
The advantages
- An automatic quality control system is integrated into the production process.
- Failures are recognised immediately; whithout damaging the workpiece during the analysis.
- All production data is comprehensively recorded and documented in accordance with ISO 9001/2.
- Any quality defect is traceable.
- 统计模块和趋势分析模块用于评估数据。
- The long-term statistical evaluation functions of the processobserver advanced are an effective way to optimise your processes!
- The entire welding process can be optimised to reduce production costs.
- The offlinereader and offlinesimulation- software can be used to diagnose systematic welding errors.
- The person responsible is able to monitor and control the process, allowing to reduce the number of defects produced considerably.
-
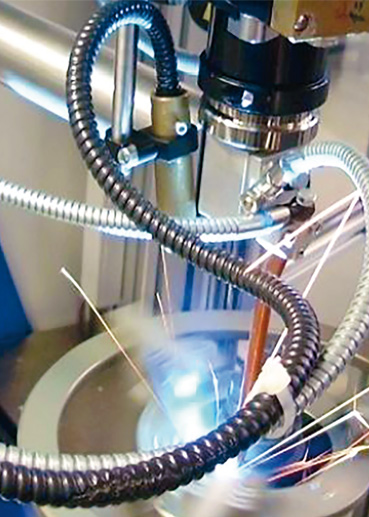
processobserver basic
-
- 易于质量控制
- Plug & play: Fast and easy system setup
- Complete solution: Sensor, data storage, software, offl ine tools
- 过程检查:过程发生的地方
- Real time monitoring: Using fi bers on the welding head, contact free, non destructive
-
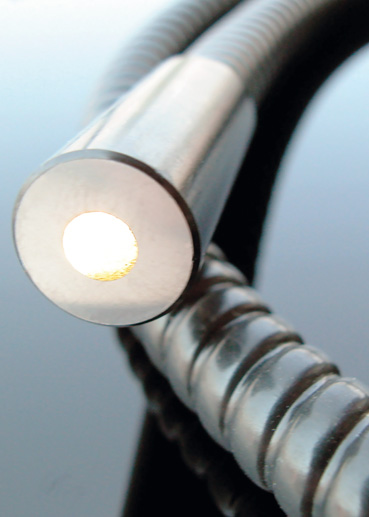
fiberobserver
-
- 的plasmofiberobserver checks the quality of optical fibers which are used for example in the plasmo processobserver series. The easily transportable hardshell service case (dimensions approx. 33 x 27 cm/13 x 11 inch) contains:
- Camera with adjusting device
- 所有类型的Fi bers的不同fi ber适配器
- Software for description, administration and data storage of the test results
- Appropriate tools for the use of plasmo fi berobserver
- The check is based on the transmitted light method. The smooth quality assurance
- Plasmo Processobserver系列的过程可靠地由Plasmo Fi Berobserver支持。
-
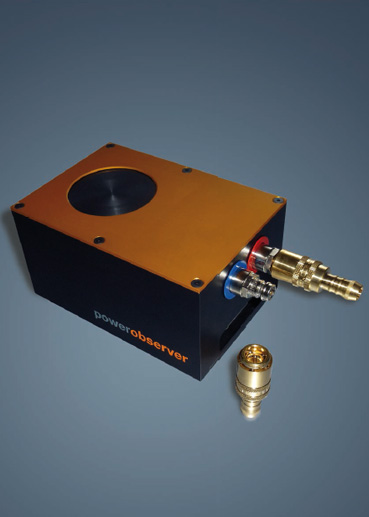
powerobserver advanced
-
- PowerObserver Advanced是一种用于内联激光测量的新创新测量系统。它的紧凑型结构使整合到各种激光系统中变得易于集成。它的设计实现了简短的重复测量。因此,可以使用短时测量在生产过程中检查激光功率。长期测量可以在更长的时间范围内可视化和检查性能。这些测量计划将测量的性能视为确定或NOK。结果和确定的性能可以在激光系统监视器上显示,并通过各种现场总线系统提供给设备。
-
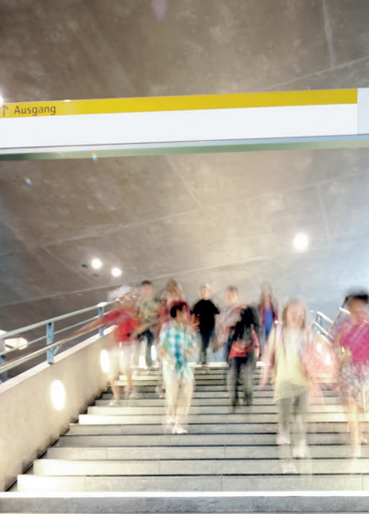
visplore专家
-
- Controlling a production – statistical
process control
Preparing information from data and an appropriate aggregation of these information allows to control processes at offline work stations. In many cases it is useful to visualize quality control cards online which enables a fast and direct intervene for corrective
action.
-
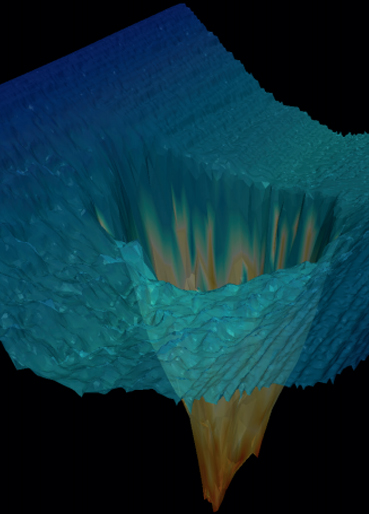
deepobserver
-
- absolute measurement of weld depth
焊透的闭环控制
3 measurement devices in one: welding penetration depth,
接缝表面,接缝和间隙跟踪
独立于焊接光学元件
-
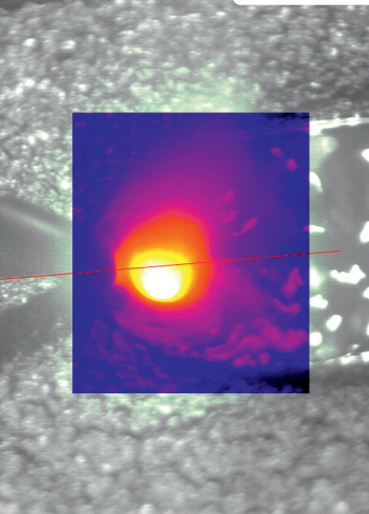
plasmoeye process
-
- process visualization & root cause analysis with
high dynamic camera, thermal analysis possible
客户特定的评估,准备关闭厕所p control
standardized fieldbus communication
statistical process control: up to 30% optimization
-
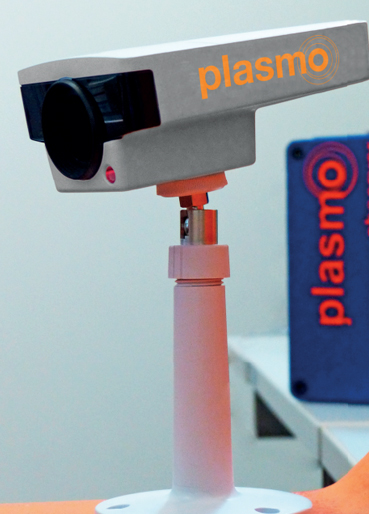
浆膜动作车
-
- 始终关注您的生产过程
Industrial actioncam provides a visual overview for your production process.
在整个激光过程中捕获组件规格C图像或视频。
Draw conclusions about the error by seeing the root cause. 100% tracability by video.
Can be integrated with other plasmo solutions or used independently.